Wire Bonding insights at your fingertips
Here we regularly present news related to wire bonding. These may be our own activities, brief food for thought or summaries of interesting publications. So it's worth spending a little more time here.

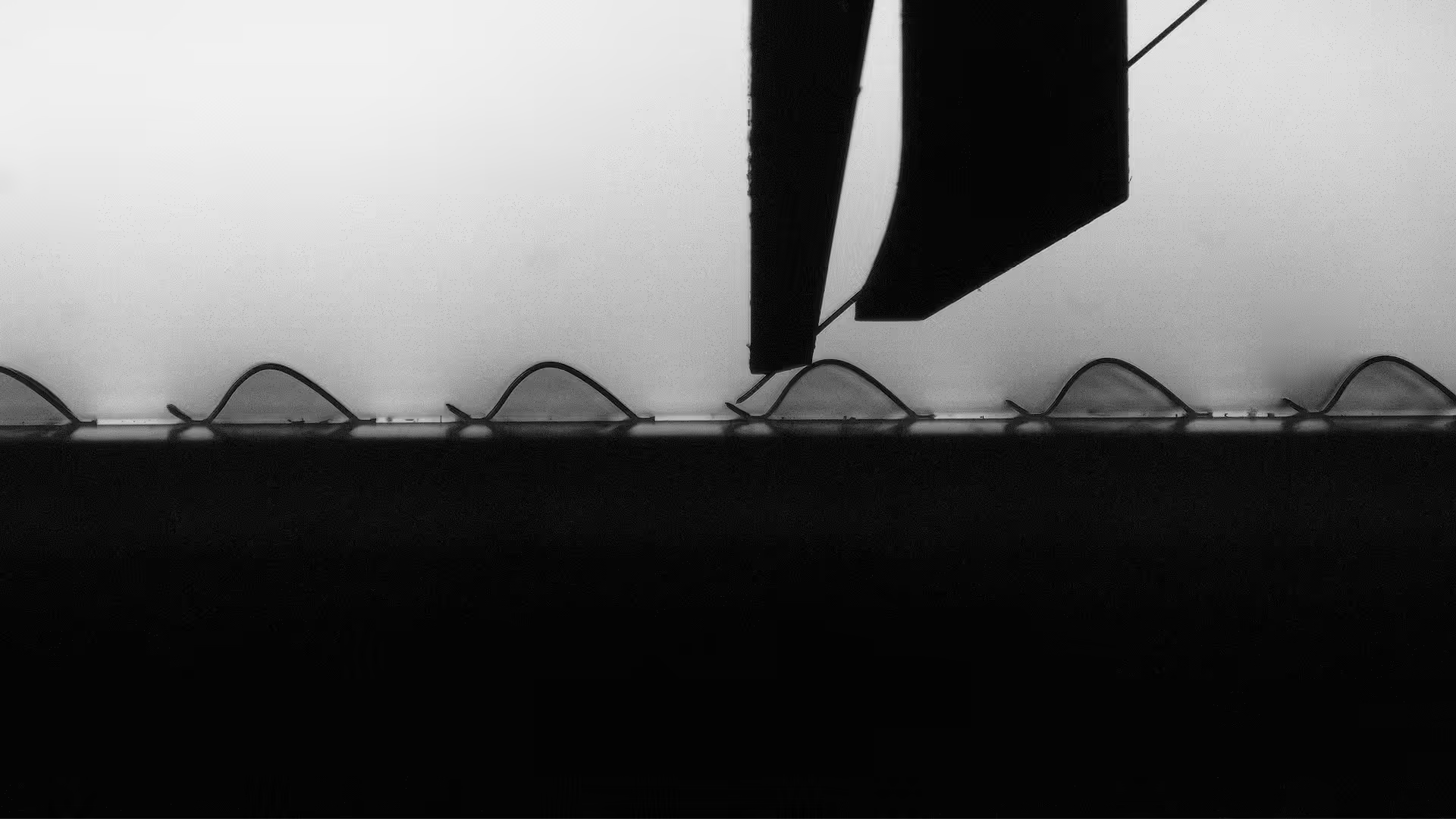
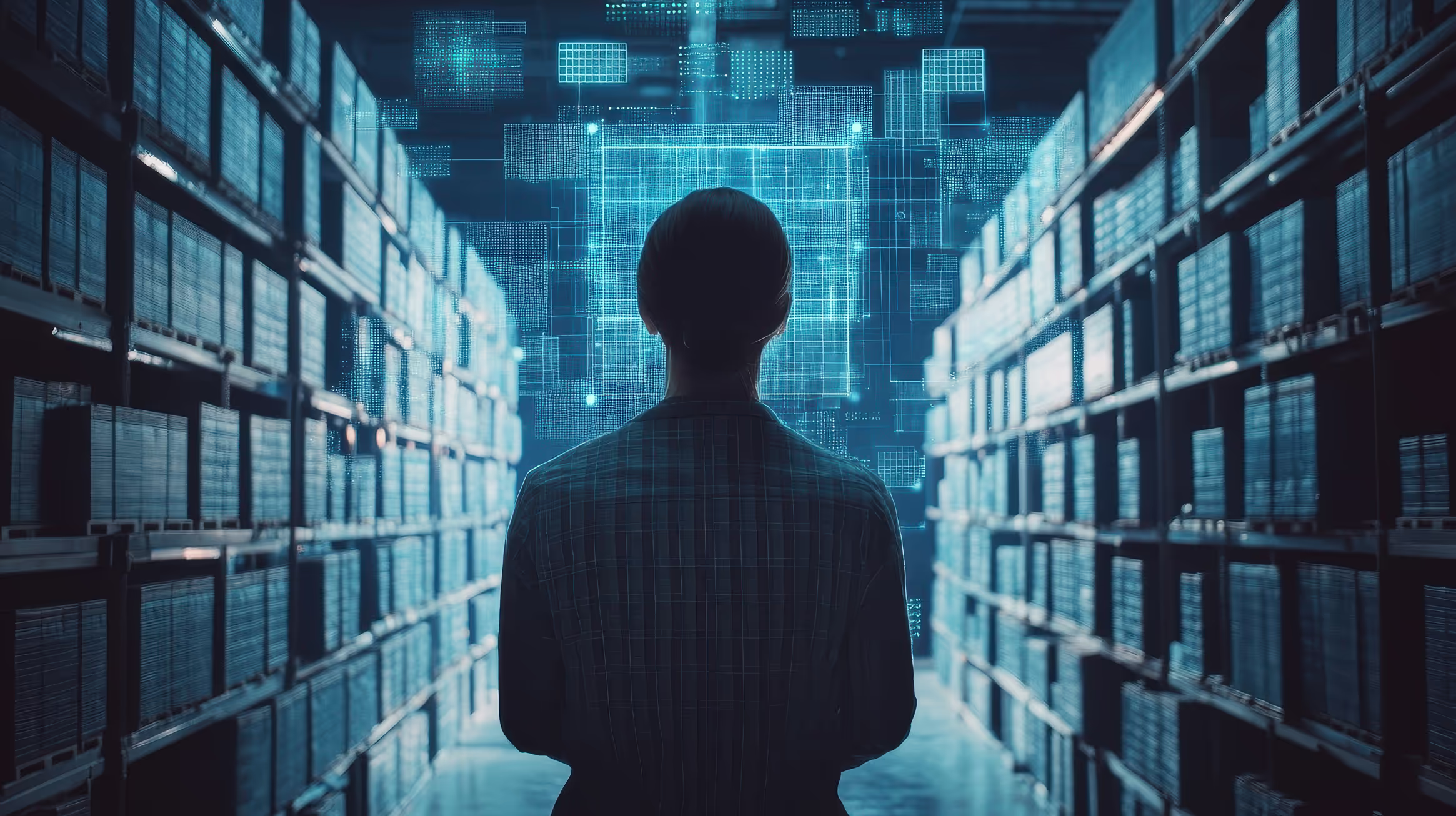
Successful Project: A Customer's Voice on Multi-Client Project’s Impact
Our project partner, KELLER Pressure, has just published an article highlighting the value of our collaboration through the Bond-IQ multi-client projects. In their article “Quality Starts on a Small Scale,” KELLER explains how Bond-IQ's research initiatives—such as QUALSi (focused on aluminum bonding wires) and surf:guide (defining bond surface standards)—are enhancing their understanding of critical quality factors.
We’re proud to see our work making a difference. Their recognition reinforces the strength of our partnership and our shared pursuit of engineering excellence.
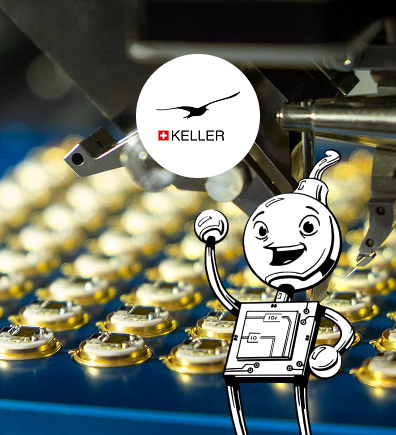
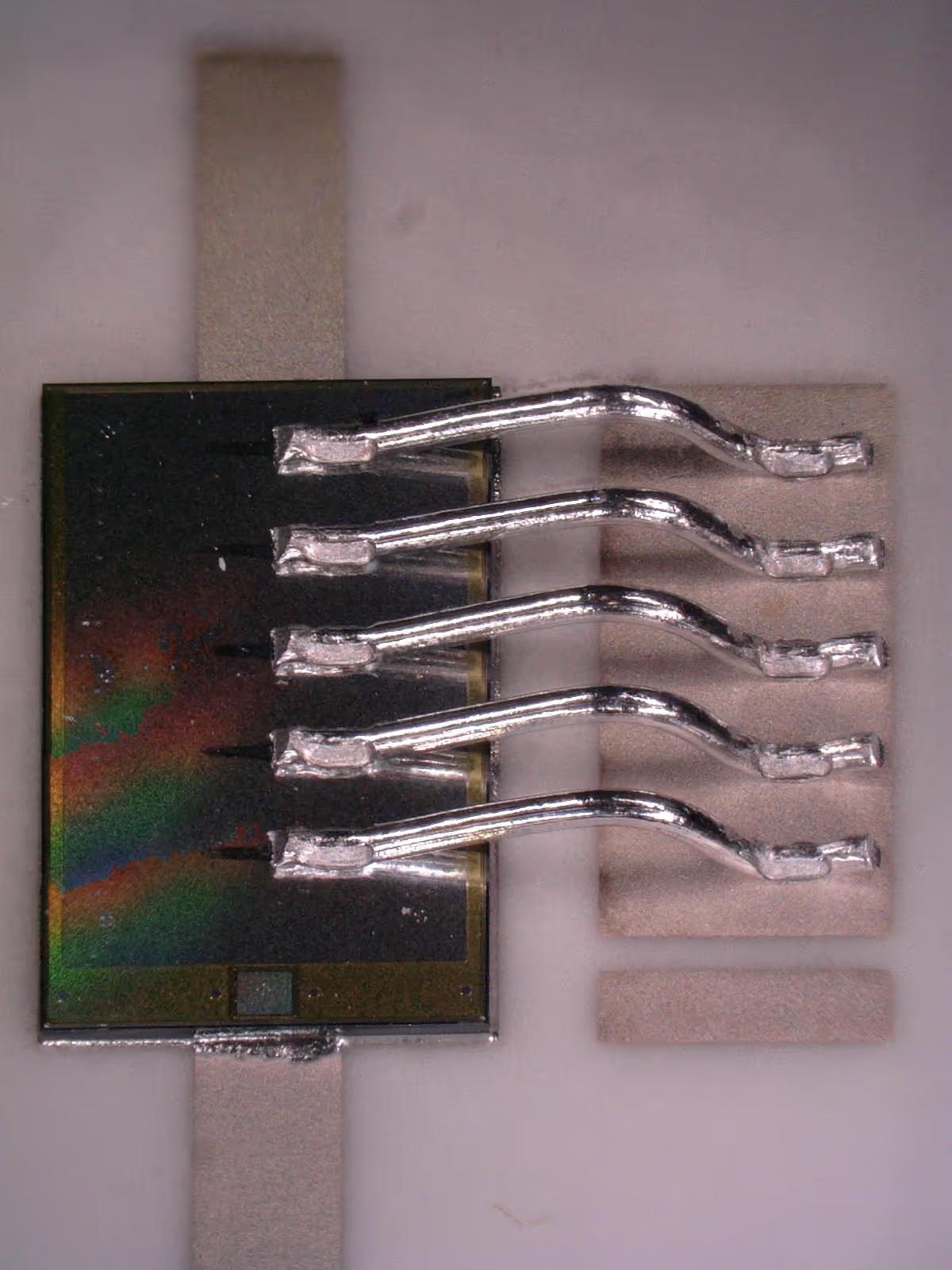
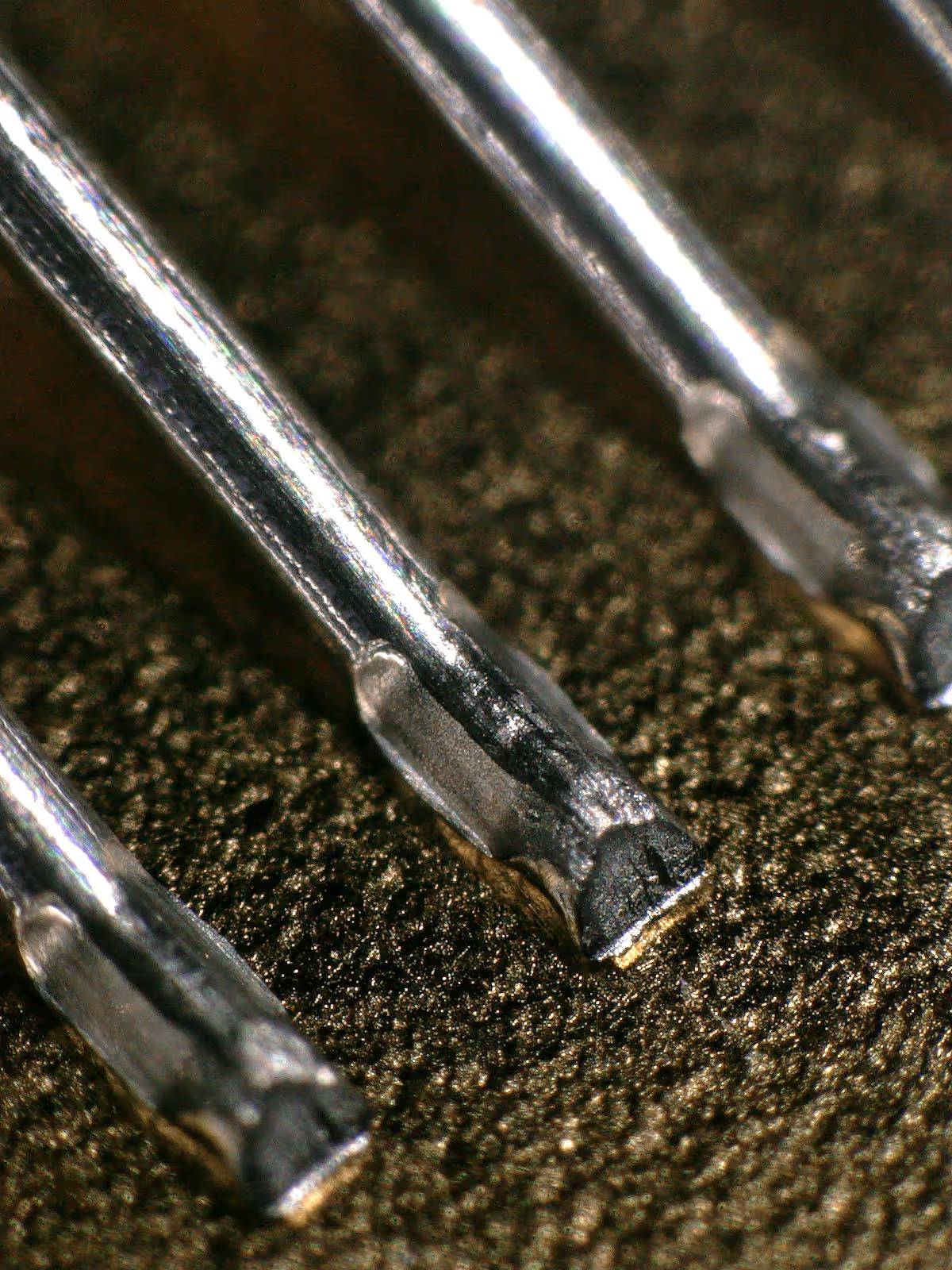
Wire Bonding Surfaces in Power Electronics
Despite ongoing miniaturization and performance improvements in power electronics, wire bonding is still essential today. Wire bondable surfaces must provide an optimal combination of electrical conductivity, mechanical stability, and resistance to aging and corrosion processes. This article introduces the most important industrially established metallizations for wire bonding, highlights typical sources of error and their effects on bond quality, and summarizes cleaning processes.
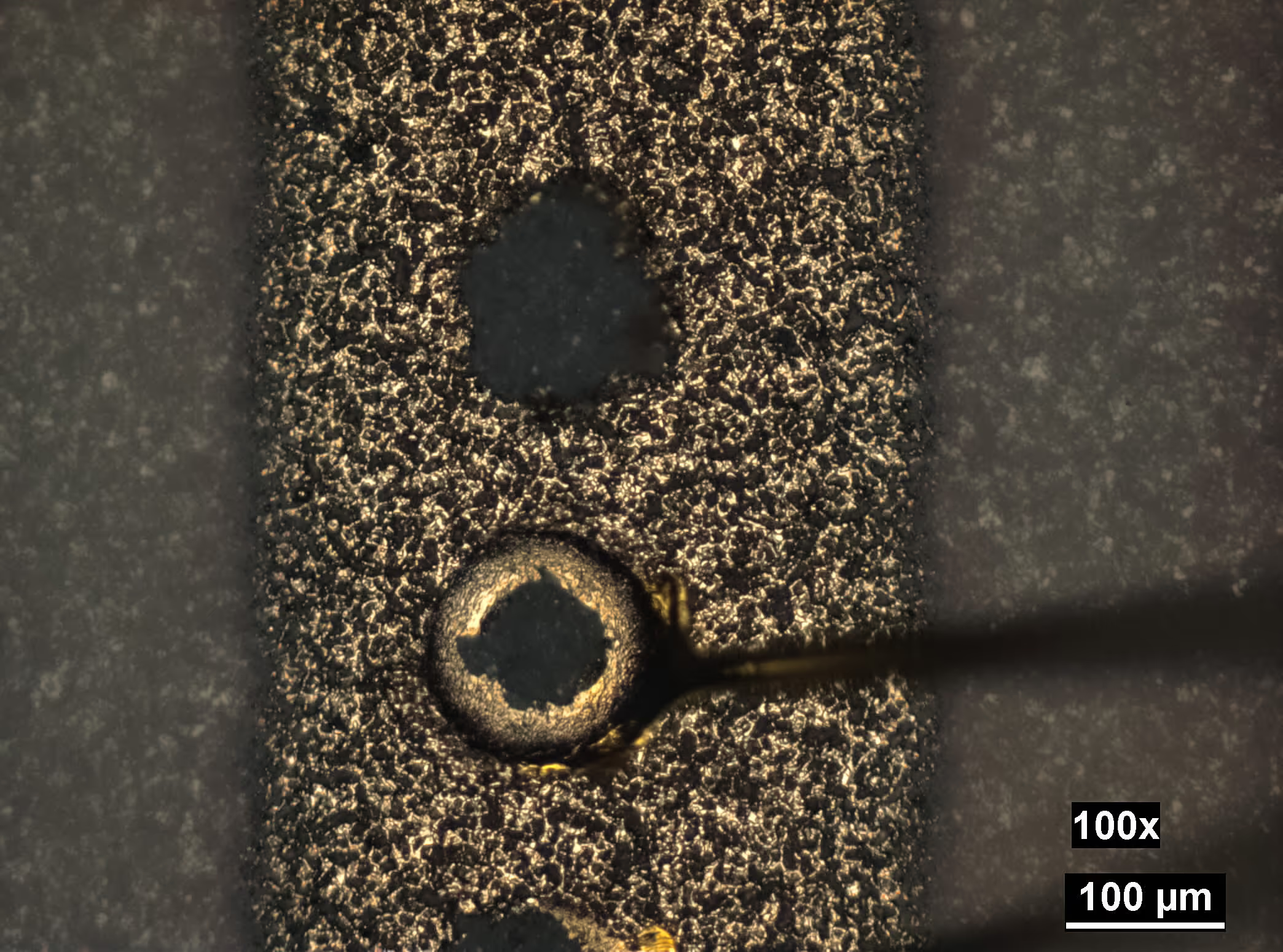
Thermosonic Bonding: Analyzing the Effects of Ultrasound, Heat, and Metallurgical Processes on Gold and Copper Wire Bonds
In the field of microelectronics, wire bonding represents a pivotal process, utilized for the interconnection of minute wires between a chip and a substrate. The research project is concerned with the comprehension and enhancement of the ball bonding process, which entails the utilization of gold or copper wires.
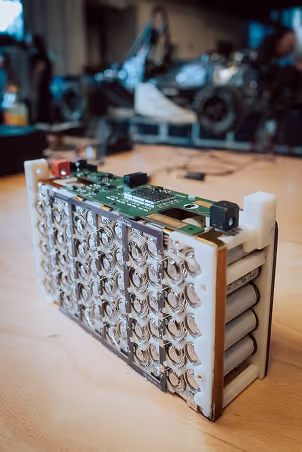
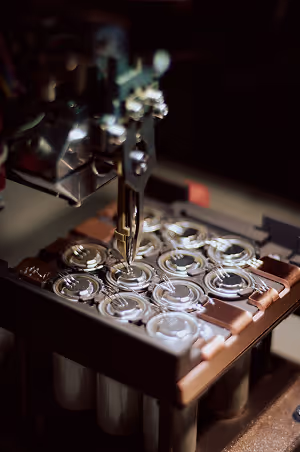
Racing Update 2024 - We are ready for the next step
We have designed the battery packs completely without bus bars. Direct connection of the battery cells, cooling through the back of the cells – i.e. wire bonding on the cathode and anode on one side of the battery cell – and 3 wires with a diameter of 500 µm per battery shoulder for maximum performance. Wire lengths of up to 20 mm that will not sag and cause short circuits despite the vibrations of driving. This allows us to achieve the highest possible level of miniaturization for this type of cell and significantly reduce weight for an even faster racing car.
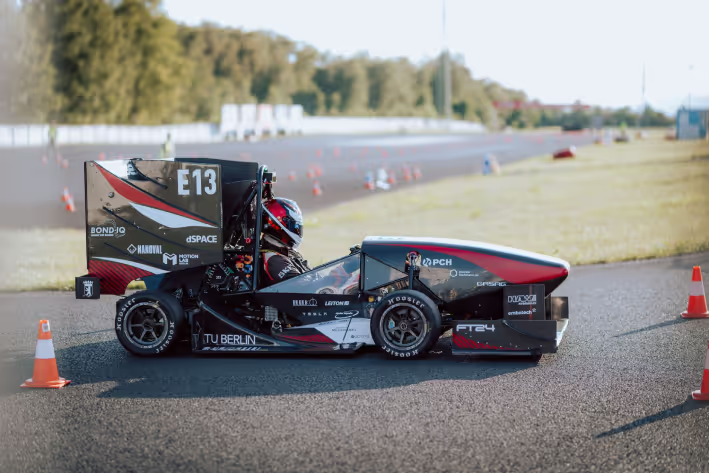
Evolution of Semiconductor Bonding Wires: From Gold to Copper and Silver Over 25 Years
This study examines the evolution of bonding wires utilized in semiconductor electronics over the past 25 years, with a particular emphasis on gold (Au), copper (Cu), and the emerging utilization of silver (Ag) wires. Bonding wires are of paramount importance for the interconnection of semiconductor chips with other components in electronic devices, such as mobile phones and computers.
How Ultrasonic Power and Intermetallic Formation Work in Thermosonic Ball Bonding
This research project is concerned with the subject of thermosonic ball bonding, a process which is employed in the field of microelectronics for the purpose of connecting components of a relatively small scale. The objective of the study is to enhance comprehension of the manner in which materials behave during this process. Thermosonic bonding is a process that employs the combination of heat, ultrasonic vibrations, and pressure to create connections between a wire, typically gold or copper, and a substrate, such as aluminum.
The study examines the formation of bonds and the microscopic alterations in the materials utilized.
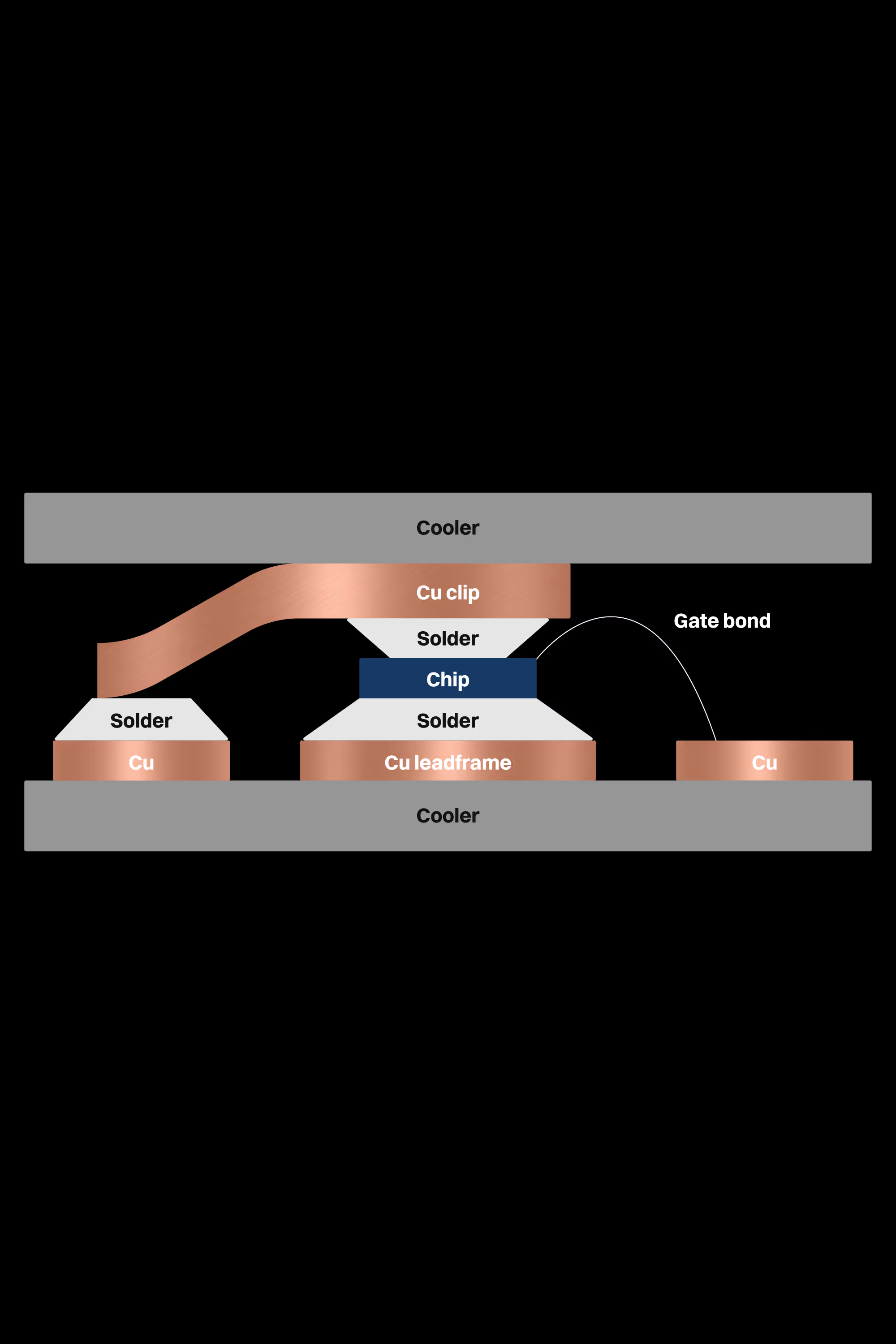
Can Copper Clips Solve the Reliability Problem in Power Electronics? A Look into Metallization Failures and Degradation
The publication's primary focus is on the reliability and failure mechanisms of the aluminum metallization layer utilized in power electronics. Power electronics, including the MOSFET (a type of transistor), are integral components in a multitude of devices, such as automobiles. Power cycling tests are typically conducted to observe the behavior of materials under conditions of elevated temperature and mechanical stress. Over time, these tests simulate the effects of real-world conditions on the chip, including temperature changes, which can cause wear and tear on the aluminum layer. This study examines the impact of switching from traditional aluminum wire bonds to copper clips on the performance and reliability of the module.
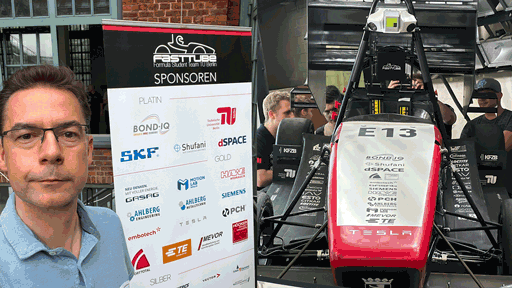
Bonding battery cells in the FASTTUBE TEAM racing car 2022
Since 2005, around 80 students from the FaSTTUBe team at the TU Berlin have been building a new racing car every year to take part in international and European Formula Student design and racing competitions. Since 2018 with an electric car and since 2020 driverless. Bond-IQ joined as a platinum sponsor in 2022, using thick wire bonding to wire the battery modules (including the driver architecture), which the development team converted from bags to 18650 cells in an impressive 3 months. As this technology is new territory for the FaSTTUBe team, we are always on hand to provide support. Whether it's a quick visit to check on a detail or a lightning-fast turnaround for a prototype. The FaSTTUBE team is fighting all the uncertainties and delivery difficulties of 2022. We will always be close at hand and will support you with all our strength and resources.
Racing Update 2023 - We improve the battery for an even better racing car
We have designed the battery packs completely without bus bars. Direct connection of the battery cells, cooling through the back of the cells – i.e. wire bonding on the cathode and anode on one side of the battery cell – and 3 wires with a diameter of 500 µm per battery shoulder for maximum performance. Wire lengths of up to 20 mm that will not sag and cause short circuits despite the vibrations of driving. This allows us to achieve the highest possible level of miniaturization for this type of cell and significantly reduce weight for an even faster racing car.
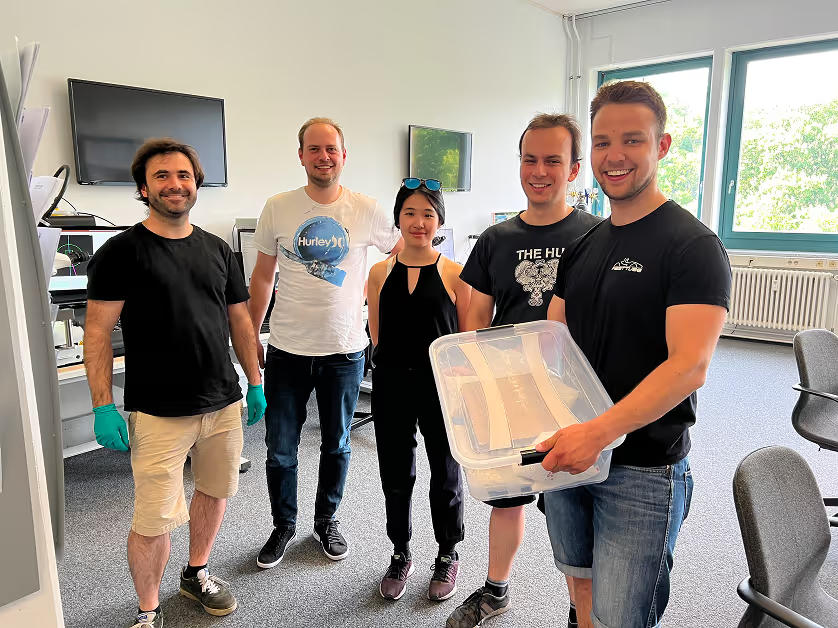
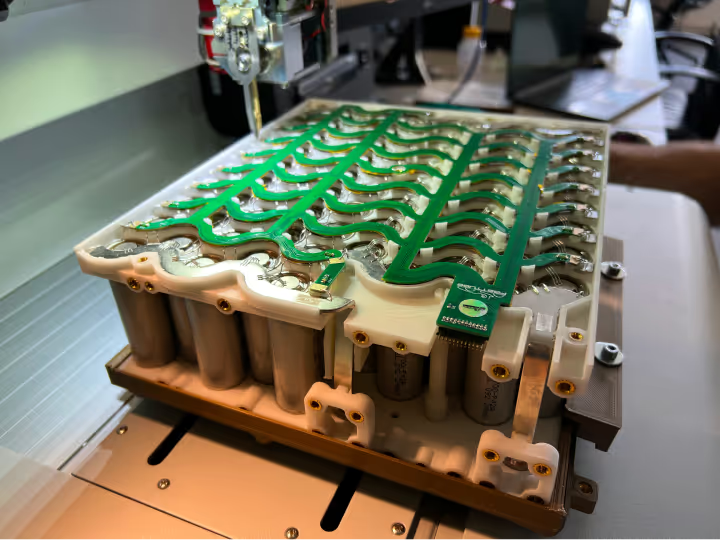
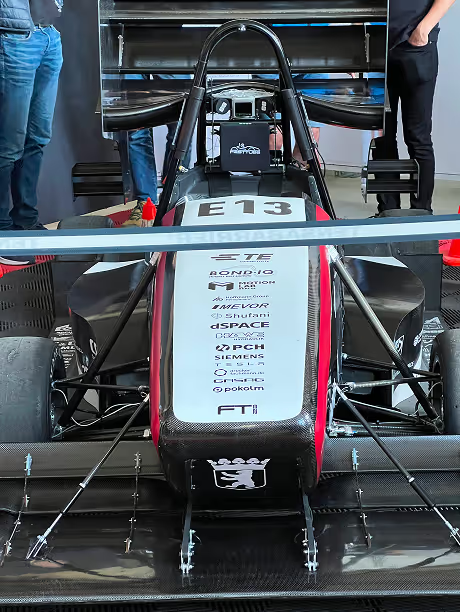
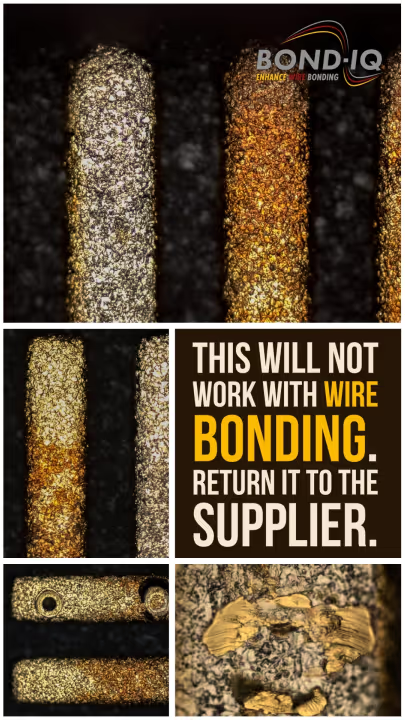
✅ Here the case is clear 🧐🕵️✅
It is simply not possible to achieve a stable wire bonding process if the surface quality is constantly changing. It is the supplier's task to ensure a homogeneous and good quality. And it is up to the customer who wire bonds to specify this quality. The supplier has to know which characteristics are important and how they have to be inspected. A visual inspection is the minimum here and should at least check the following details:
• Local discolorations and stains
• Drying stains
• Flux residues
• Solder spots#
• Filmic contaminations, e.g. oils, fats, fingerprints
• Local holes, scratches, scores
• Scoring marks resulting from mechanical processing, e.g. brushing, polishing, grinding
• Test needle imprints
• Exposed copper or nickel
There are always two sides to a coin 🥉. Those who do not care and specify well, but leave everything to their supplier, are part of the problem. So if you don't care, you then don't have to be surprised when things often go wrong. If it is as clear as in the picture of this post, the case is clear and the delivered lot goes back to the supplier - but that also costs resources and time, valuable time.
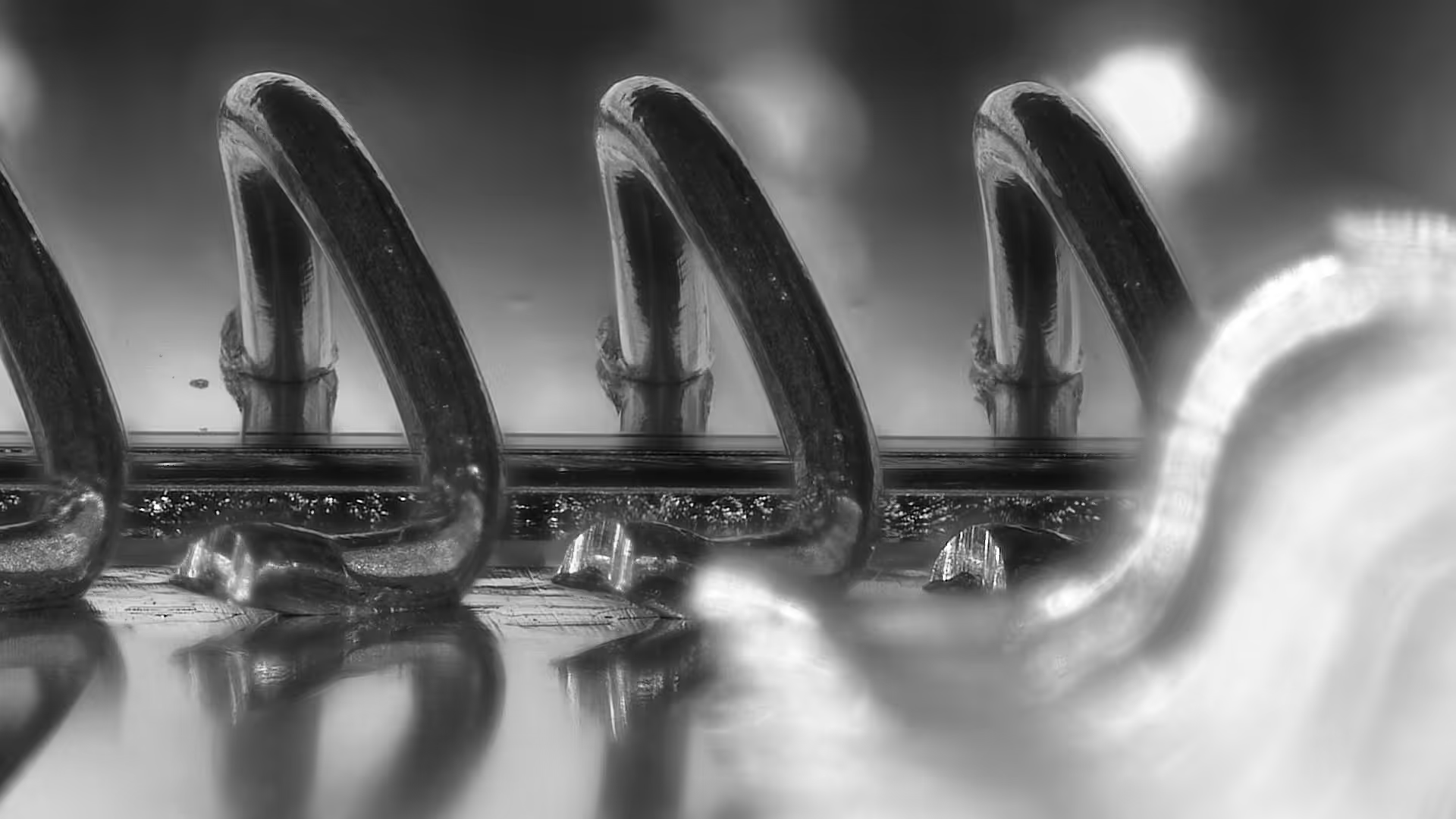
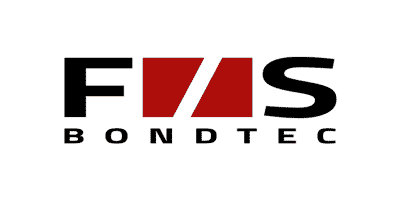
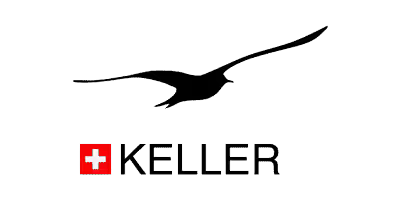
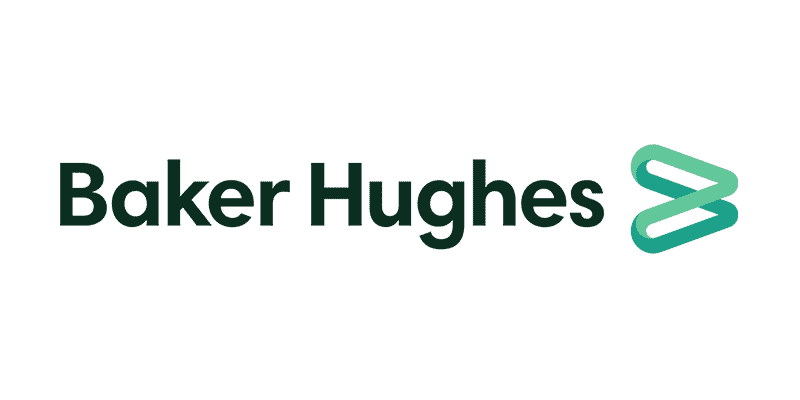
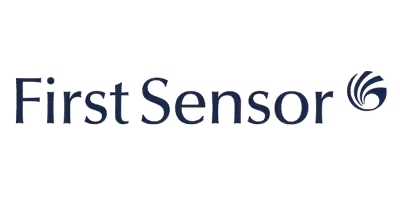
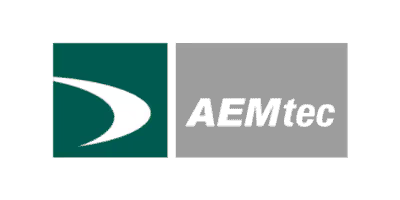

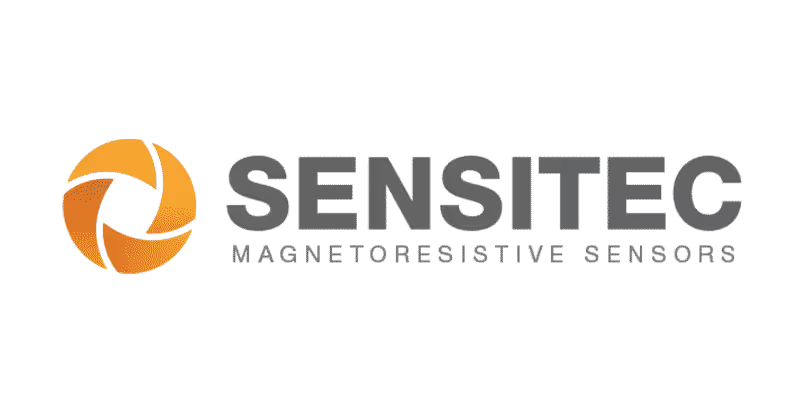
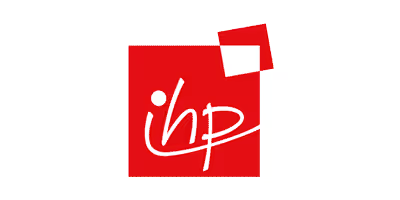
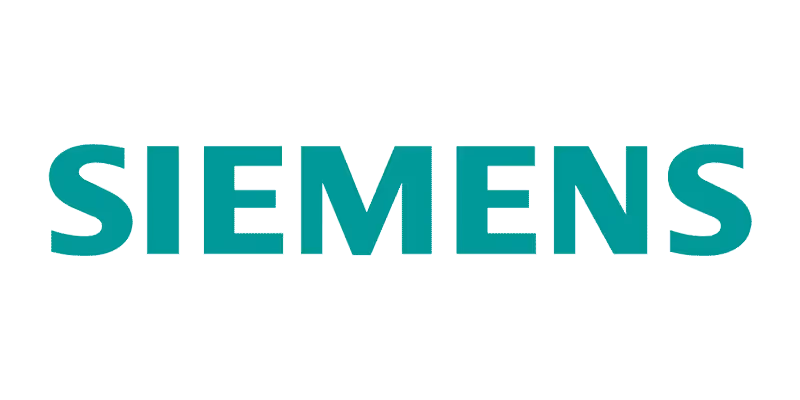
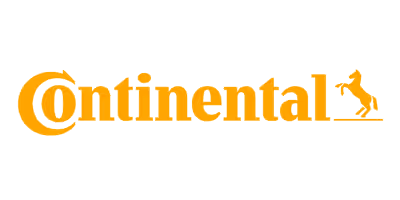
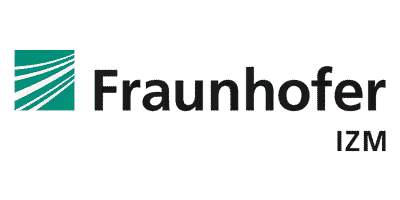
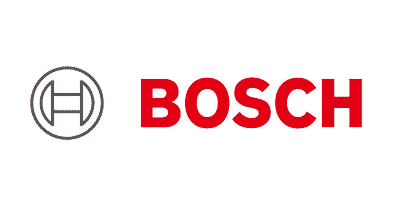
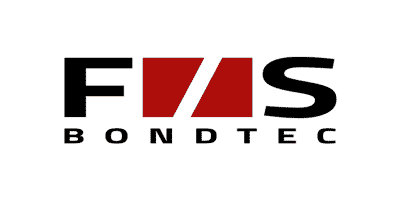
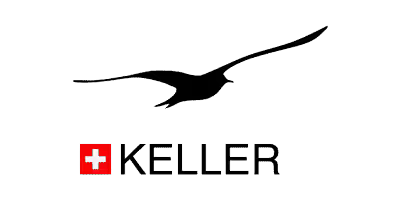
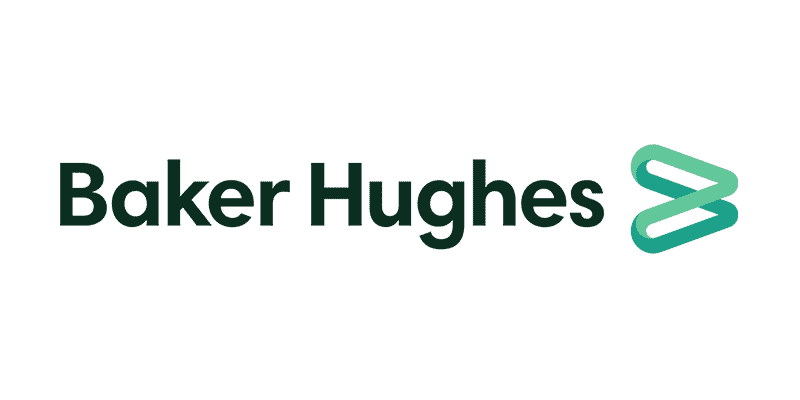
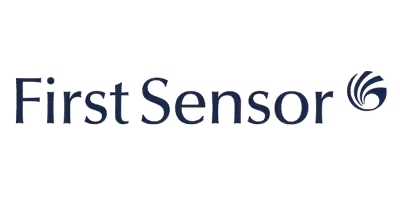
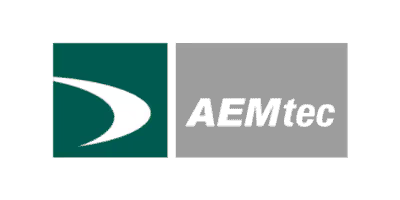

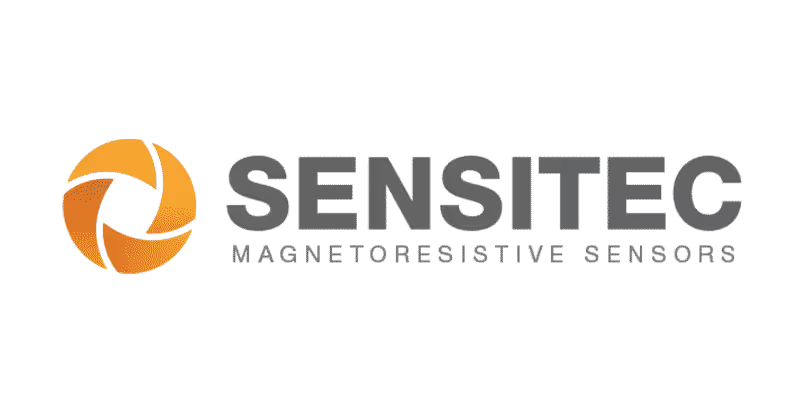
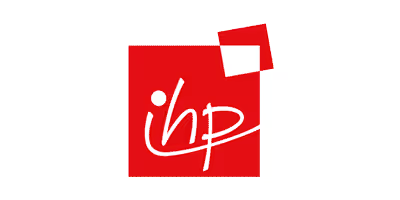
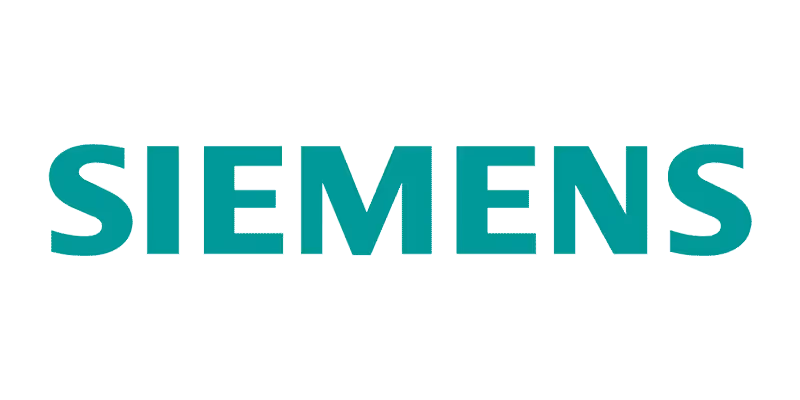
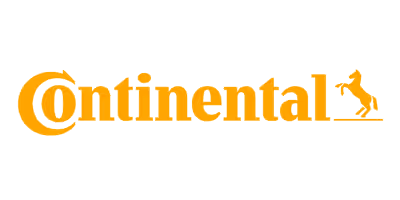
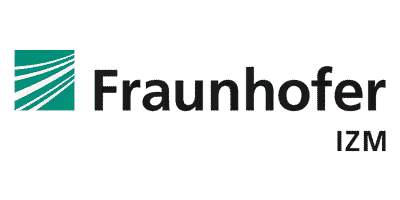
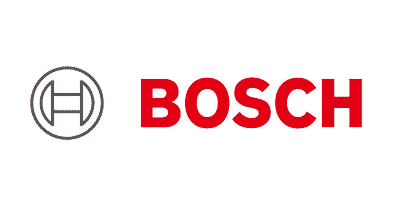
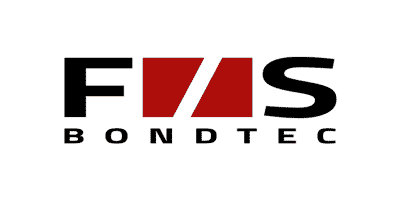
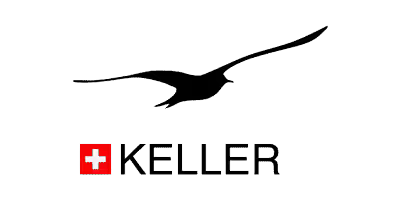
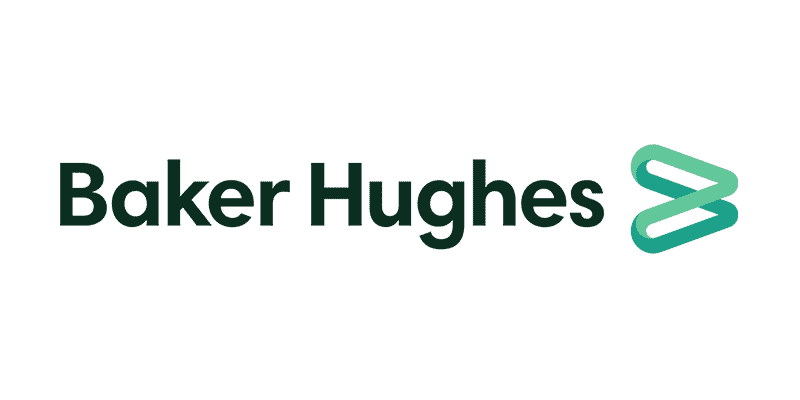
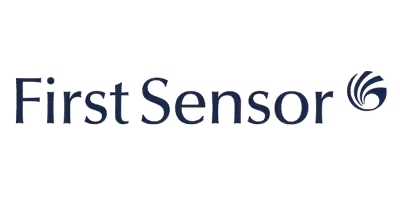
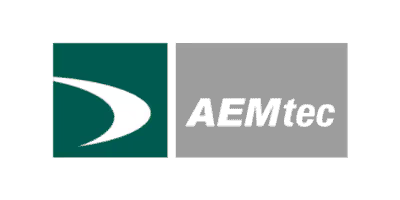

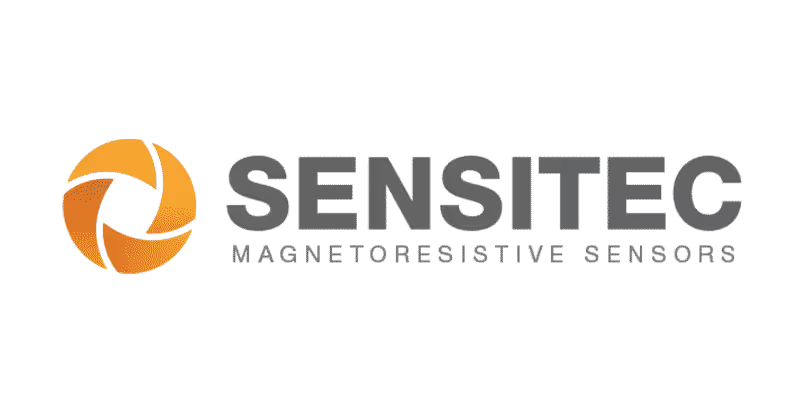
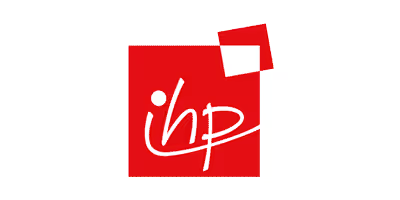
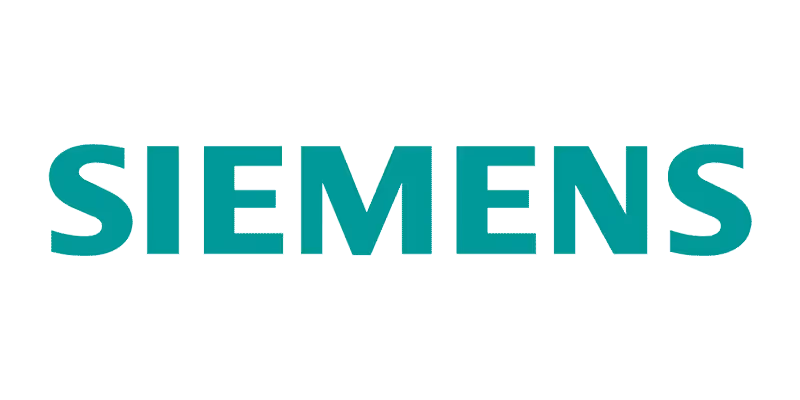
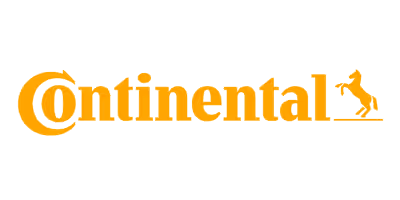
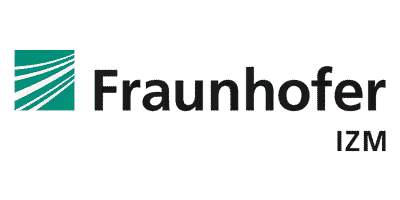
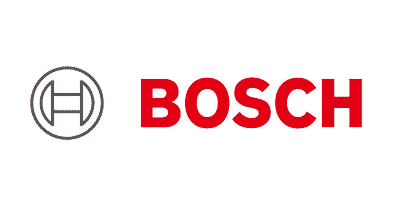
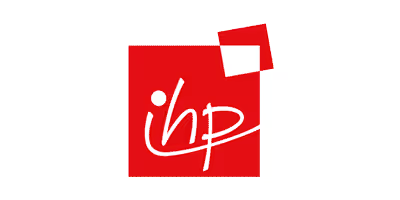
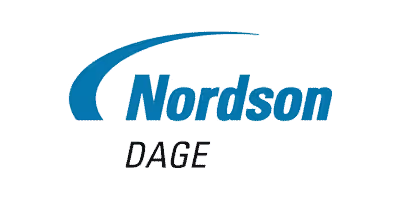
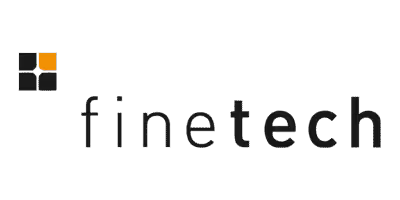
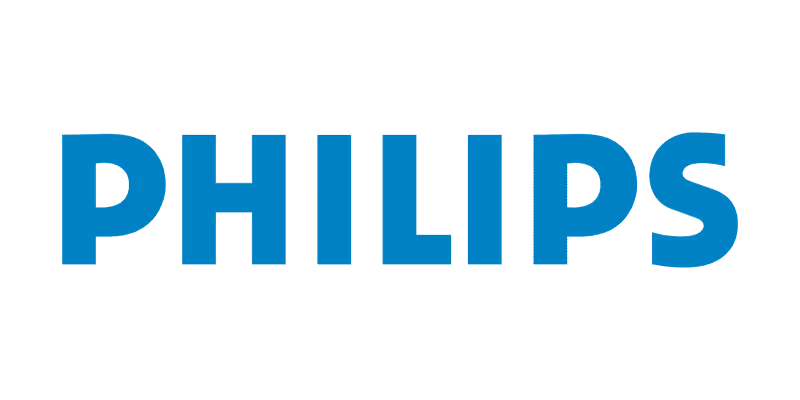
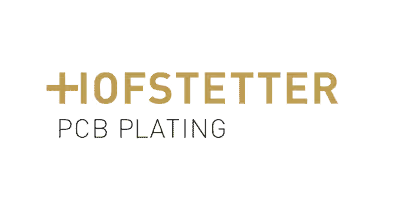
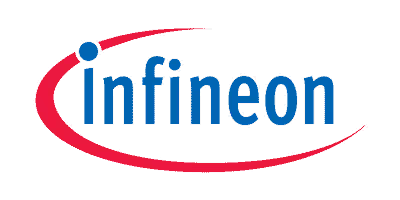
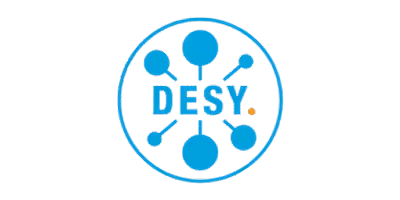
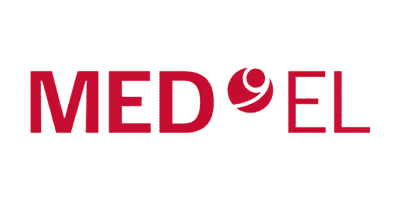
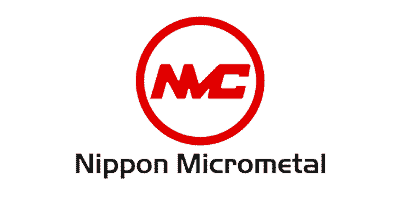
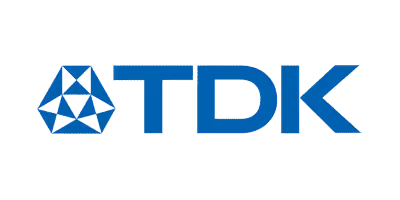
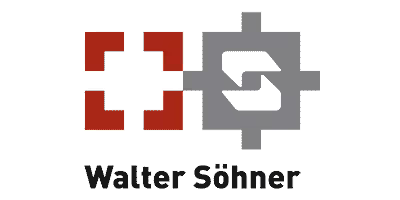
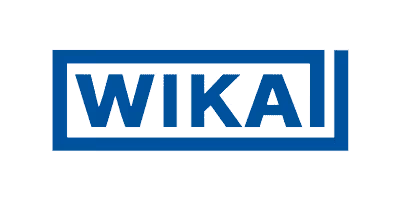
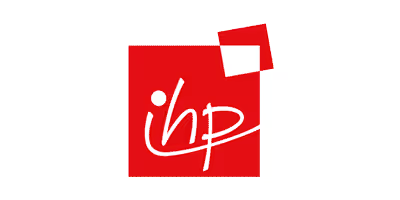
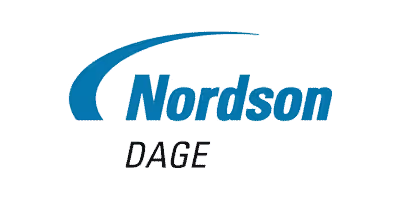
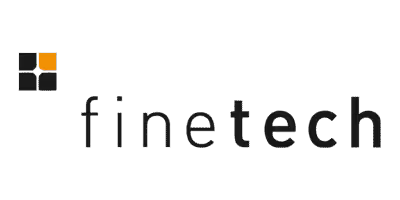
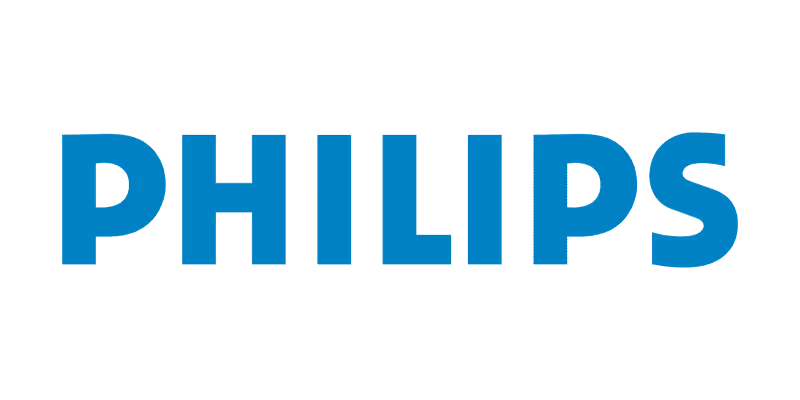
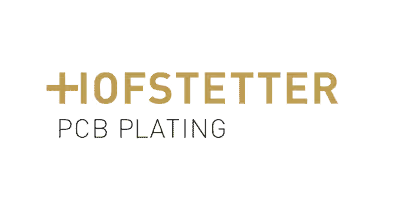
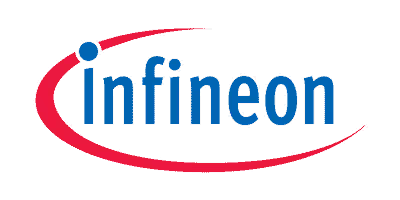
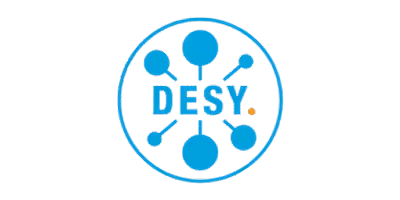
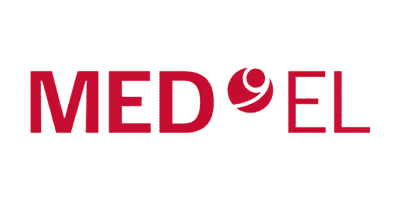
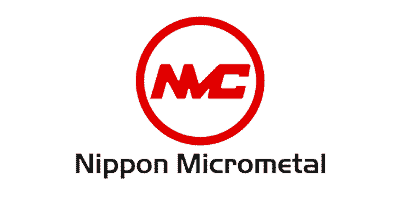
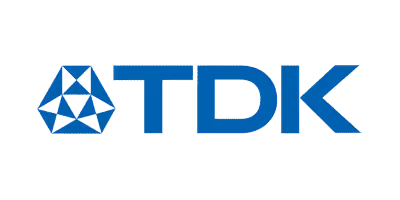
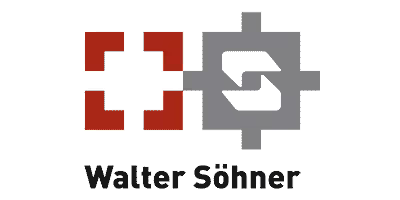
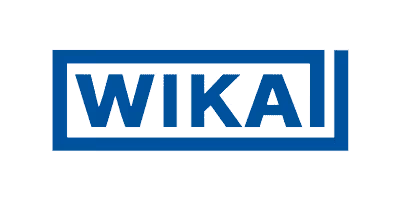
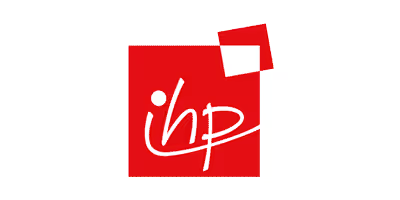
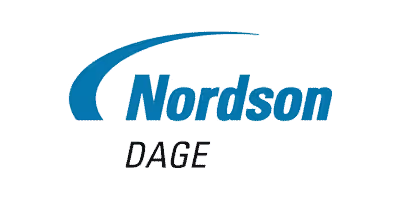
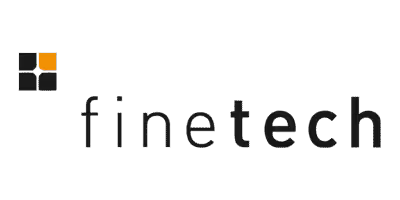
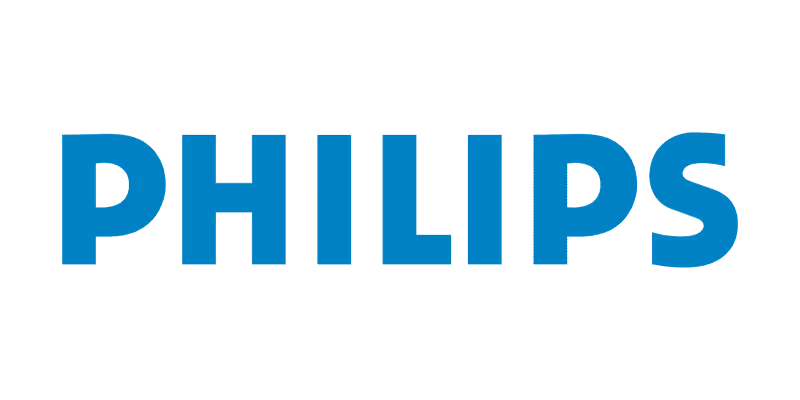
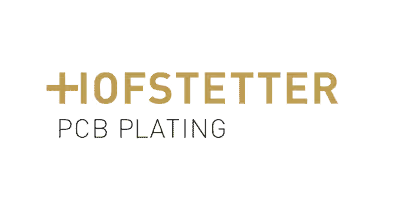
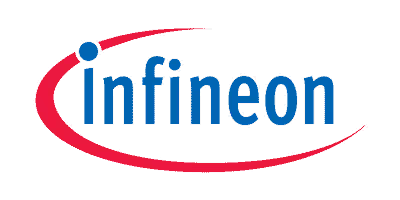
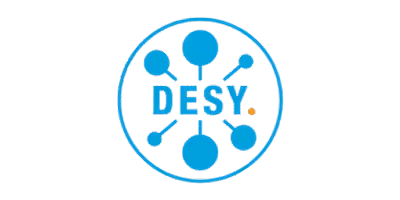
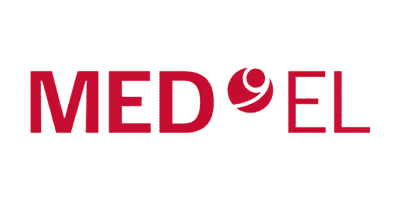
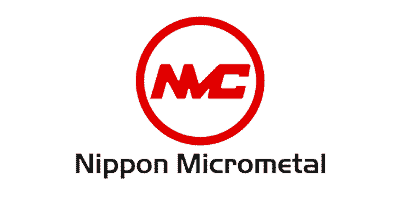
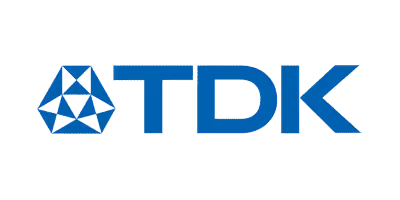
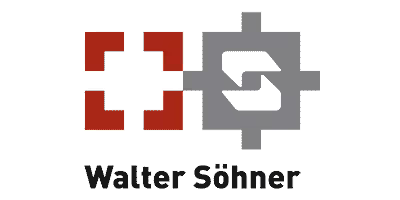
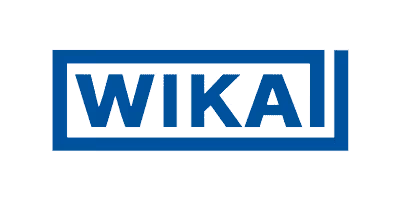
A New Approach to Wire Bond Testing Could Improve High-Power Electronics Reliability
The objective of this study is to enhance the reliability assessment of wire bonds in power electronics, with a particular emphasis on the Highly Accelerated Lifetime Testing (HALT) methodology. In the context of electronic devices, wire bonding refers to a technique whereby thin wires are used to connect semiconductor components. With the passage of time, these bonds may succumb to failure as a consequence of wear and tear, particularly in the context of extreme temperature fluctuations. The researchers developed a mechanical testing method to simulate the failure that would naturally occur in wire bonds over time, thereby enabling them to predict the longevity of the bonds in real-world conditions.
New Standards in Wire Bonding: A Detailed Analysis of DVS-2811 for Automotive and Power Electronics
The authors examine the advancements in wire bonding standards for the European automotive and power electronics industries. Wire bonding is a method of creating electrical connections between semiconductor devices and their packaging using thin wires, which are of critical importance for the production of microelectronics, such as batteries. The study concentrates on the DVS-2811 standard, which provides guidance on the testing and inspection of wire bonds.
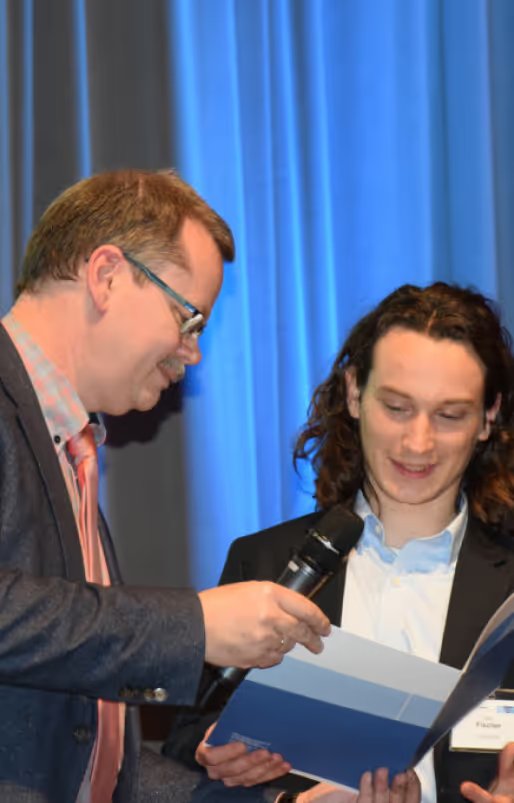
1st EBL Young Researcher Award at the EBL 2018
Felix Fischer (Microsystems Engineering student at HTW Berlin) successfully presented his master's thesis in a paper and a presentation at the EBL Conference 2018, winning the prize for the best presentation. The thesis was carried out at Fraunhofer IZM Berlin and supported by Bond-IQ with extensive experiments and know-how, with the aim of investigating the semi-autocatalytic Au plating system on electrolessly deposited NiP for wire bonding applications with AlSi1 wire, e.g. for chip-on-board (COB) technology. The ability of the plating system to significantly reduce nickel corrosion during the deposition process and thus counteract coating adhesion problems during bonding is of great interest to users requiring stable bonding processes. The work has shown, in some cases with complex analysis, that there are still pitfalls in the technology and that further development is needed to solve the problem. Felix Fischer is continuing his research on this topic at Fraunhofer IZM and Bond-IQ will support his work.
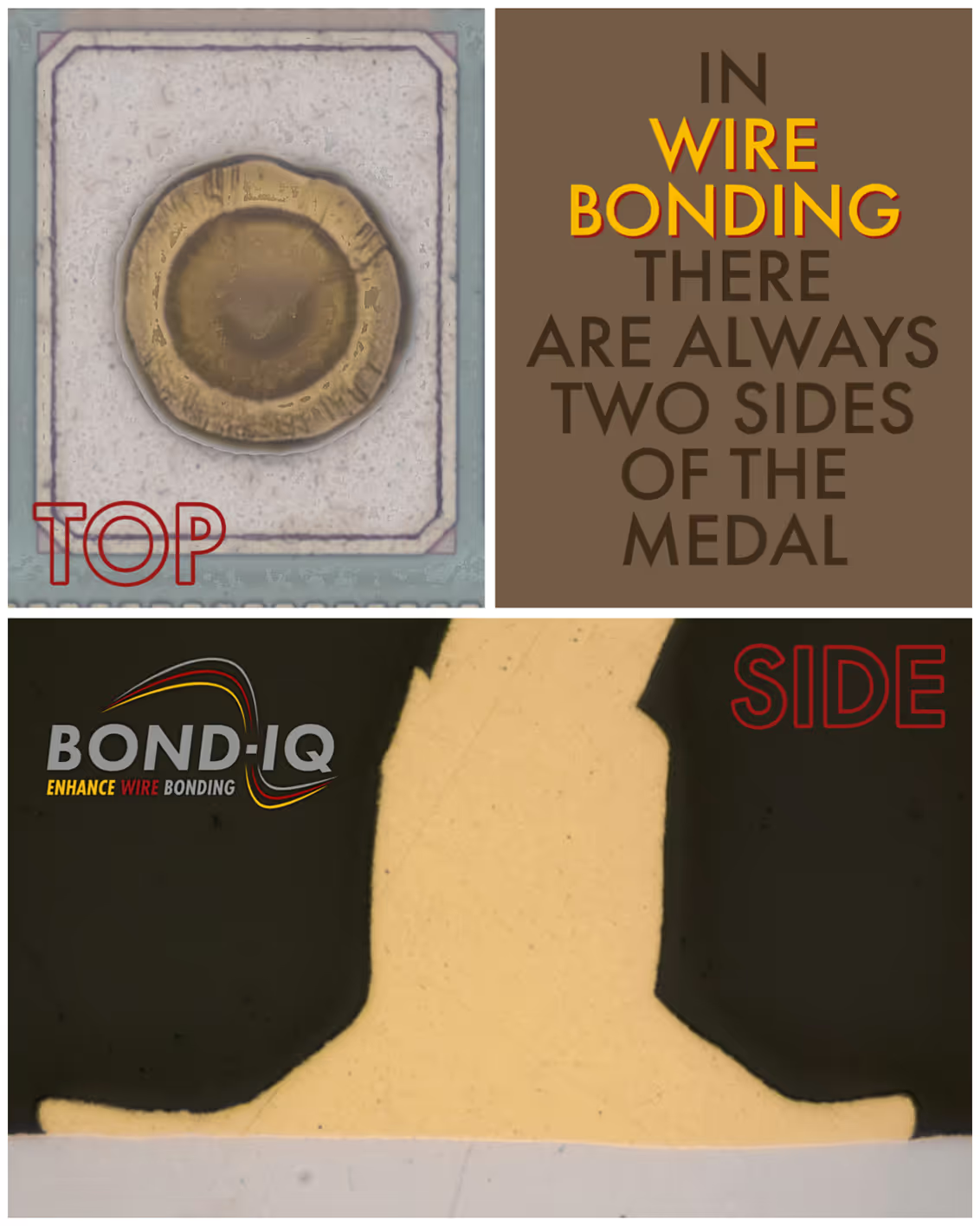
✅ Think about how closely you look to check your wire bond contacts. First impressions can be deceiving...
With ball bonding, the volume of the ball (FAB) is determined by the flame-off process. This spherical volume is then transformed into the typical shape of a ball bond. This ball bond has a height (MBH - Mashed Ball Height) and a diameter (MBD - Mashed Ball Diameter). Just measuring the diameter is therefore not sufficient to check whether the FAB has been flamed in a defined manner and whether the bonding process has run smoothly.
Even when the ball looks good in a microscope, fluctuations in FAB volume can have the following effects:
🔸 Mashed Ball Height too flat or too high
🔸 Changed energy coupling/stress in the bond pad
🔸 Fluctuating connection quality
🔸 Highly scattering shear test results
Regularly checking the height of a ball bond is therefore part of state-of-the-art wire bond process control. This requires the right testing equipment and well-trained personnel 🙋🏼♂️🙋🏼♀️👨🏼💻👩🏻💻👨🏼🔧🧑🏻🔧.
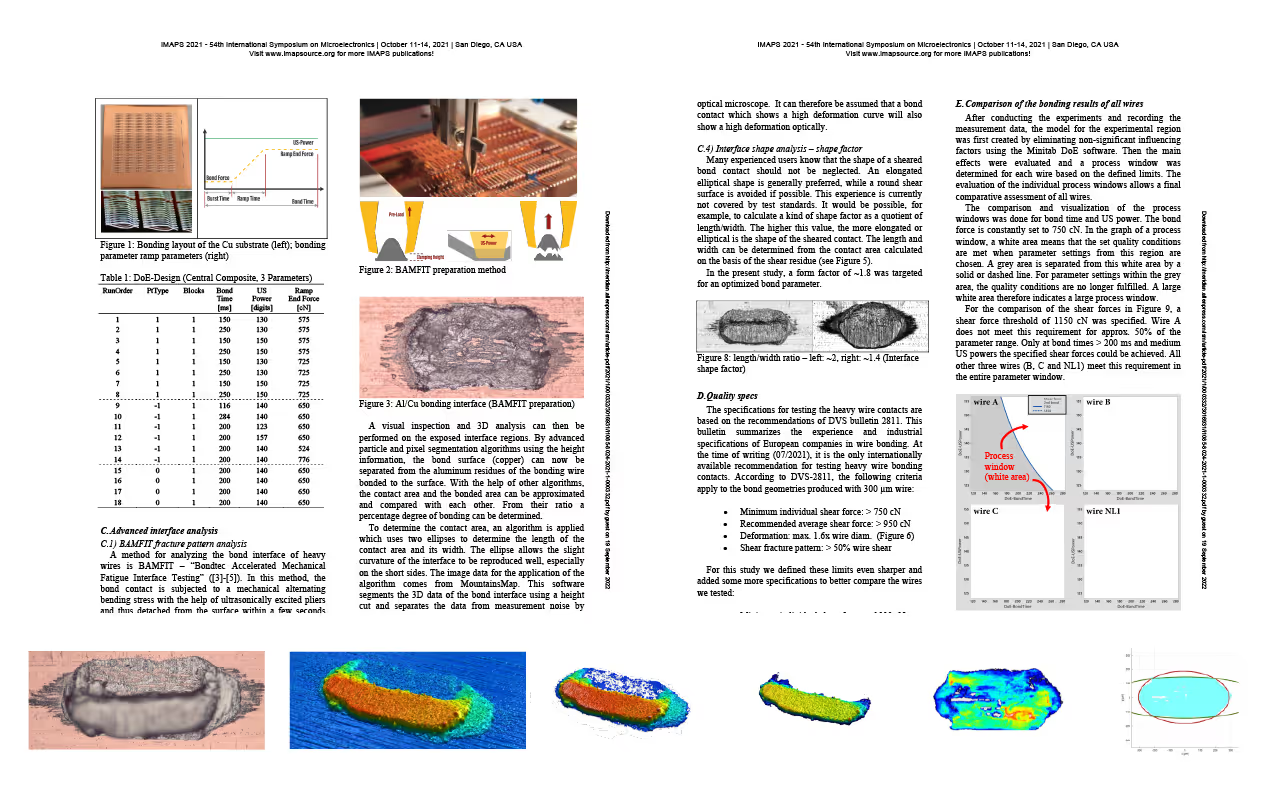
Advanced bonding interface inspection technique for process optimization in heavy wire bonding
Presented at the IMAPS conference in October 2021, this paper presents a novel methodology for analyzing the interface formation of heavy wire-bonded contacts. By combining the BAMFIT (Bondtec Accelerated Mechanical Fatigue Interface Testing) method, 3D fracture pattern measurements, and customized evaluation algorithms, this approach provides accurate data on the bonded interface area. Unlike traditional shear testing, this method directly measures the bonded area, allowing for improved parameter tuning for different material systems. The study examined four wire types with similar mechanical properties, using design of experiment (DoE) techniques to identify process windows and material-specific insights. The results highlight the benefits of accurately measuring the bonded area and illustrate where conventional shear testing has limitations in detailed analysis. This work provides valuable guidance for optimizing bonding processes and material selection.
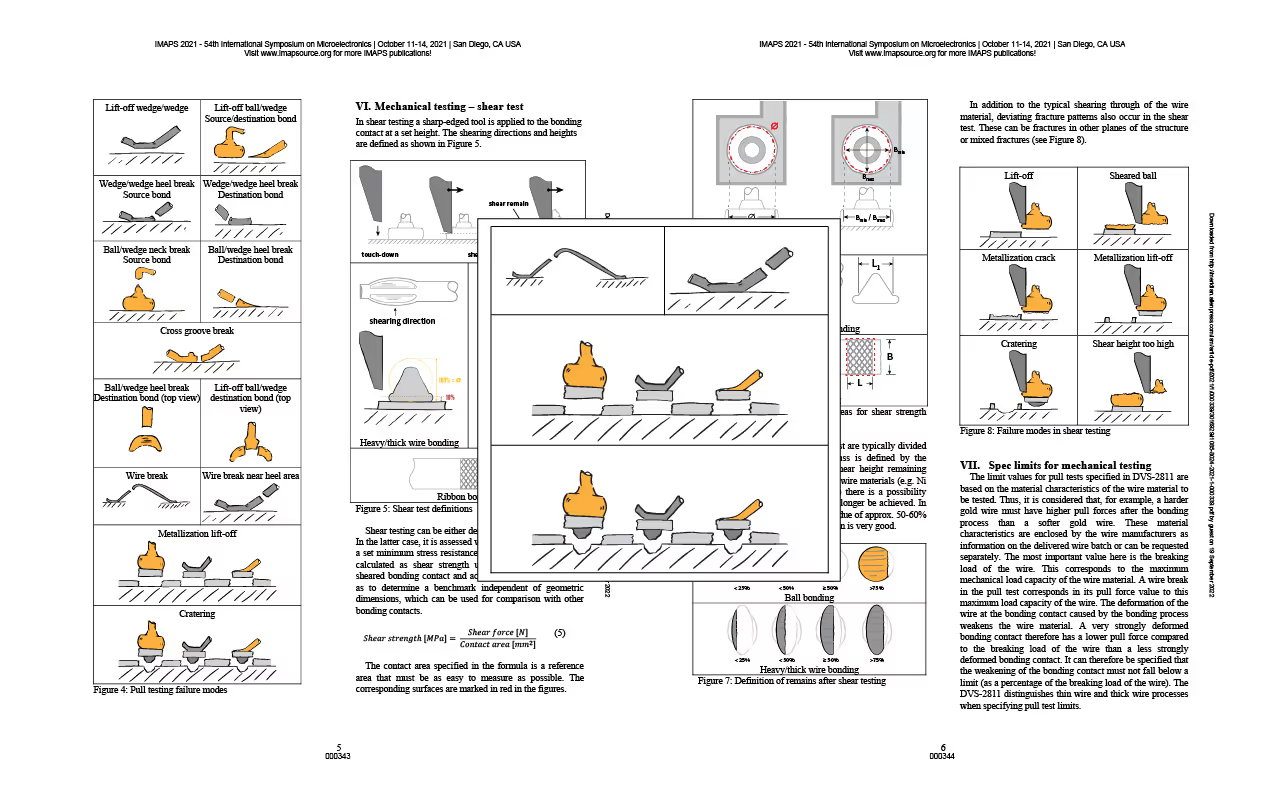
Revision of the wire bonding test standard DVS-2811
In February 2017, after more than 20 years, a revised version of the DVS-2811 test standard for wire bonding was published. From its start in September 2014 to its completion in December 2015, Bond-IQ worked intensively on the revision in a multi-client project, structuring and conducting the necessary experiments and coordinating the project. This work was done in close cooperation with Fraunhofer IZM Berlin. 25 project partners were involved and were fully convinced of the necessity and success of the project to revise the existing test standard. Just one year later, this was published as an official bulletin of the DVS Association under the previous number DVS-2811 with the addition of the version 02/2017. Since then, a comprehensive document for the testing of thin-wire and (still internationally unique) thick-wire bonded joints has been available. DVS Technical Bulletin 2811 is officially available from Beuth-Verlag in German and English.
Power Cycling and Wire Bond Reliability: The Critical Role of Wire Material and Diameter in Extending Lifetime
This research project examines the reliability of various types of aluminum heavy wire bonds utilized in power electronics, with a particular focus on their performance in MOSFET modules. Wire bonding is a common method used to connect electronic components, but the reliability of these bonds is of critical importance for long-term performance. The study examines the impact of varying aluminum wire materials and diameters on the durability of these wire bonds during power cycling, a process whereby the system is repeatedly turned on and off, resulting in temperature fluctuations.
Sintering and Copper Wire Bonding: Reducing Failure Rates in High-Thermal Power Modules
This paper presents a summary of the advancements in power electronic packaging, with a particular emphasis on the enhancement of reliability and performance under high temperatures. Power electronics are utilized in a multitude of devices to regulate electrical energy, and these systems encounter challenges due to the thermal stresses that are generated during operation. One area of focus is wire bonding, which involves the use of a metal wire to establish a connection between a semiconductor chip and other components.
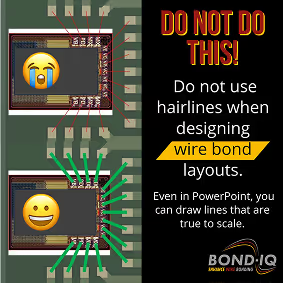
I often see hairlines in the layout program. Here you can zoom in beautifully - the line always stays thin. Everything fits perfectly. The surprise comes at the wire bonder when the first wires are pulled. Suddenly you realize that the distance between two wires is much too small. All of a sudden, you realize just how tight the tolerances are when there is just a slight shift or twist in the chip.
This can be avoided. 🤩
Even a simple presentation program like Powerpoint can do a good job here if no specialized layout programs are available at that moment:
Paste a screenshot of the layout in Powerpoint
Find a known dimension in the layout (e.g. chip size)
Insert a rectangle in Powerpoint and scale it to that dimension
Read the dimension of the rectangle in Powerpoint
Scale all lines and shapes relative to this rectangle
✅ Draw correctly scaled lines/rectangles as wires.
For number junkies: The effort here is between 45-60s per wire. So for a layout with 30 to 60 wires, you'll be busy for a maximum of 30 to 60 minutes. A time investment that pays off and can save a lot of money.
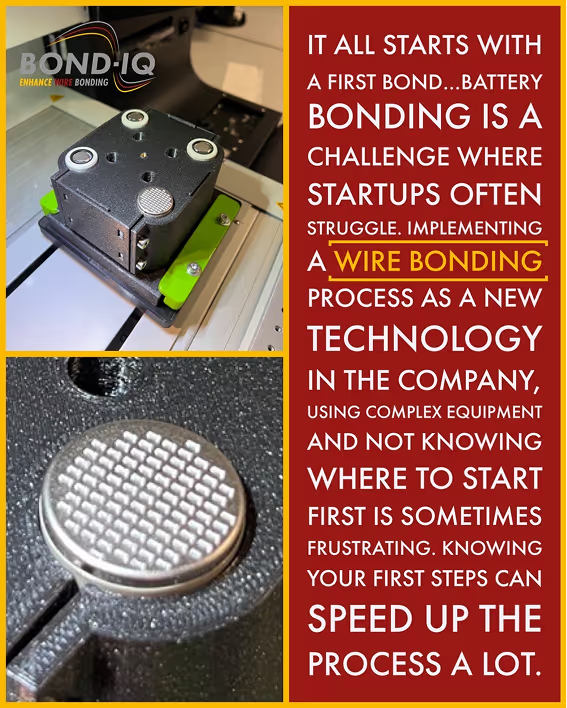
✅ Delving into the world of wire bonding of battery cells? Fantastic! Here's how to kickstart your journey in this technology.🚀
Master the Basics: Start with the fundamental principles, understanding the precise control of the three key parameters in ultrasonic bonding - ultrasonic vibrational power, normal force, and bonding time. They work together to create a strong bond between the wire and the bonding surface. Learn to use time controlled ramping of these parameters to get best bond strength and shear test results.
Learn about the correct quality testing methods. Pull-/Shear test is your friend but a good microscope is your forever-best-buddy. And start making friendship with laser cleaning.
Quality Assurance: Learn about the process integrated quality monitoring and control systems in wire bonders. This cutting-edge technology provides real-time feedback on bond quality, a valuable tool for improving yields and quality.
Practice Makes Perfect: Like any other skill, proficiency in wire bonding requires practice. Start with simple projects, gradually taking on more complex tasks as you build confidence and refine your technique. Find ways to use the available material as best as possible. Use individual cells and bond only the first bond - nearly every machine offers this feature (ask if you don´t know…be sure it is there).
Stay Updated: Technology evolves rapidly. Keep an eye on the latest developments in wire bonding, participate in forums, webinars, and workshops. Connect with industry peers on platforms like LinkedIn to share ideas and learn from their experiences.
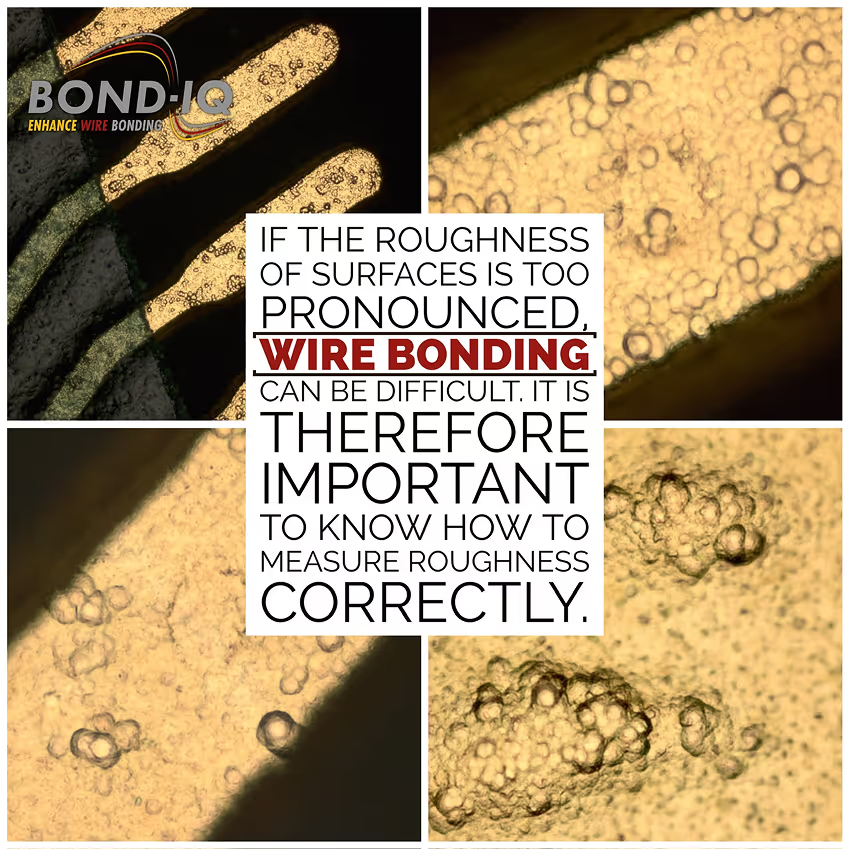
✅ In 2018, we successfully completed the „mikroRau“ project on the roughness of bond surfaces, which we coordinated for 26 industry partners. At that time, in addition to many exciting insights 💡, I had to learn an important detail about roughness measurement: For a defined, repeatable measurement that is traceable to roughness standards, specialized measurement technology is needed. Just "3D measuring" is not enough 🚫. This may sound plausible and not exactly like a grandiose novelty – but in my experience, many users underestimate exactly this point and measure with what they have 😱.
If the right equipment is available, it can be used in a variety of ways for quality inspection during wire bonding. I have summarized some examples here 👉🏻 https://bond-iq.de/wp-content/uploads/3D-measurement-wirebonding_EN.pdf
When measuring roughness, we were able to work out the following details:
✅ Be sure to work with surface roughness values!
✅ Use advanced optical inspection methods. These are ideal, especially for tests on bond pads.
✅ Pay attention to the limitations of the optics used and use methods that allow high critical angles for artifact-free measurement. The edge steepness of some bond surfaces overwhelms systems with low-cost solutions. Some methods are not suitable due to their principle.
✅ What cannot be measured reasonably cannot be corrected even with the best software 💻🚫.
✅ Ra values or Sa values are often used for evaluation, but they are rather unsuitable for bond surfaces ❌.
✅ Rz values or Sz values (or even better S10z values) are suitable for evaluation. However, this value expresses only one property of bond surfaces. It must be accompanied by other values. This is similar to the test methods for wire bonds (visual, mechanical and data-based) – here, too, one test alone is often not sufficient.
✅ Good software for analysis is expensive, very expensive 💰💸. But it has to be. Modern evaluation methods/algorithms can only be realized with it. Good software pays back this money in the end, because the use of templates speeds up the workflows considerably 🚀💯.
Reducing Wire Bond Failure: How Adjusting Bond Foot Angles Improves Power Module Reliability
The study focuses on wire bonding, a critical process for connecting electronic components within power modules. Wire bonding creates connections between a semiconductor chip and its supporting structure (substrate). In this research, scientists are examining how different angles at which the wire touches the chip, known as the bond foot angle, affect the longevity of these bonds. A larger bond foot angle tends to reduce the life of the wire bond because it introduces additional stress during operation. The team used both experiments and simulations to test the effects of varying bond foot angles on wire bond reliability.
Advancements in Copper Ball-Wedge Wire Bonding: A Cost-Effective Alternative to Gold in Semiconductor Manufacturing
The literature review examines advancements in copper (Cu) ball-wedge bonding, a technique utilized to establish connections between wires in electronic devices. Historically, gold (Au) was the material of choice due to its resistance to corrosion. However, the increasing costs associated with gold have prompted the exploration of alternative materials, such as copper. Copper offers superior electrical performance, but it also presents challenges such as oxidation (rusting) and increased hardness, which complicate the bonding process.
Investigating the Inaccuracies in Wire Bonding Pull Testing and Introducing a New Analytical Model for Improved Quality Control
This study examines the process of wire bonding pull testing, which represents a pivotal quality control step in microelectronics, particularly in fields such as automotive and sensor manufacturing. The process of wire bonding entails the formation of connections between small wires and electronic components. It is of paramount importance to ensure that these bonds are robust in order to guarantee the reliability of the final product.
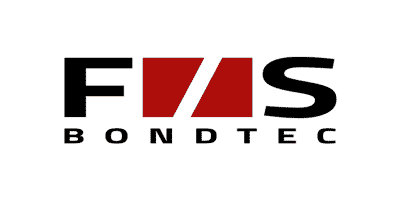
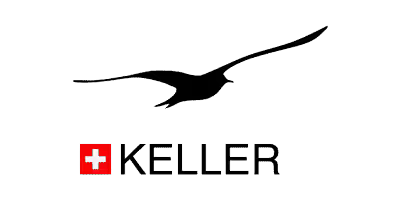
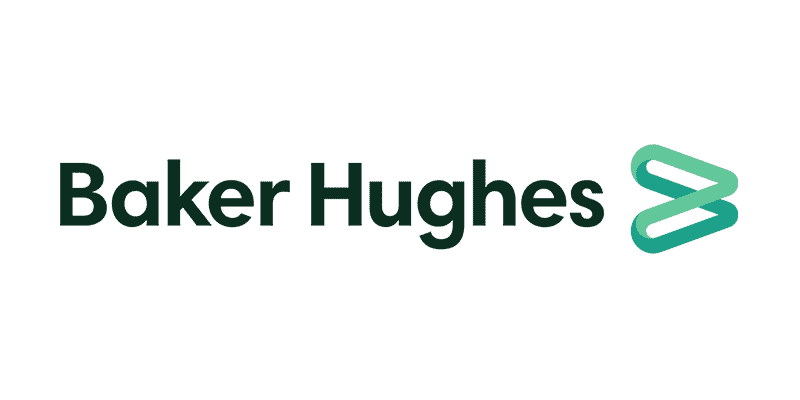
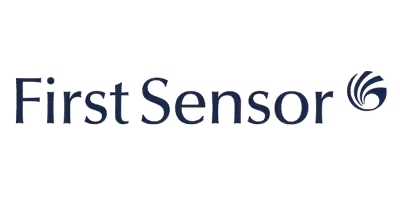
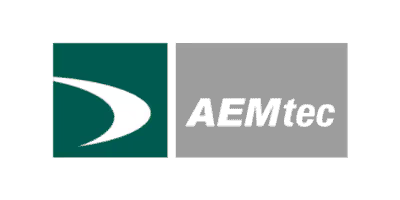

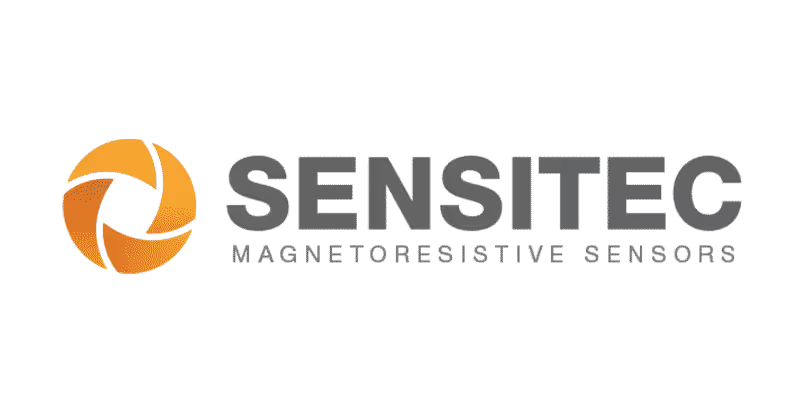
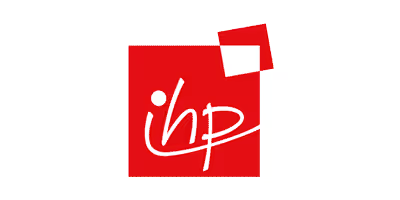
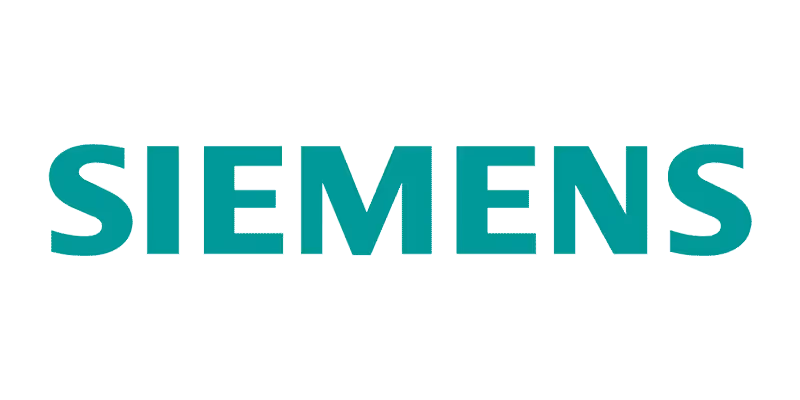
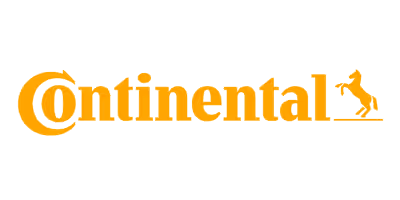
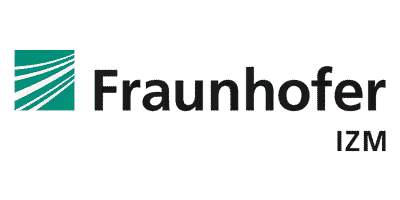
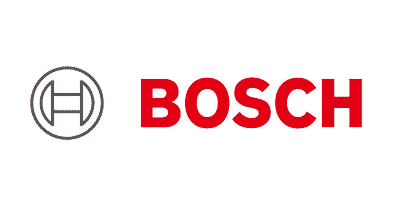
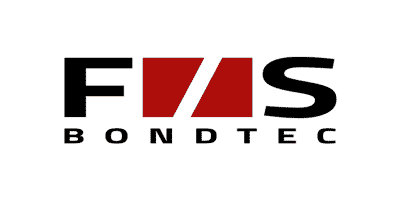
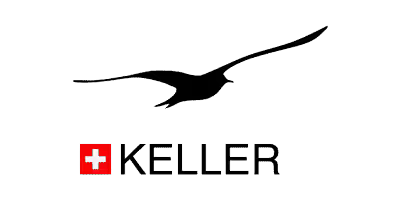
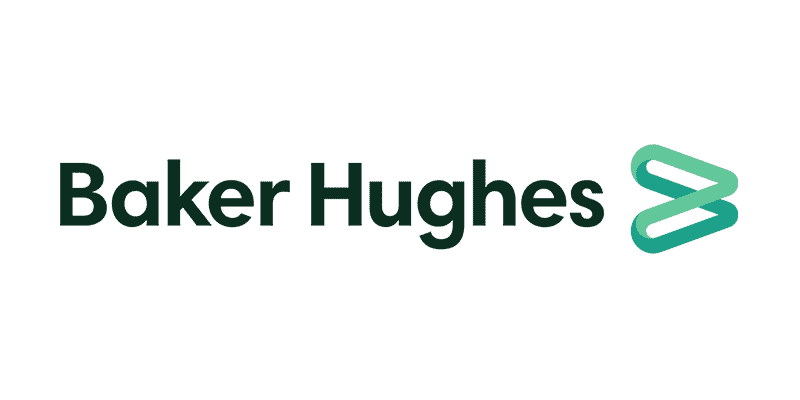
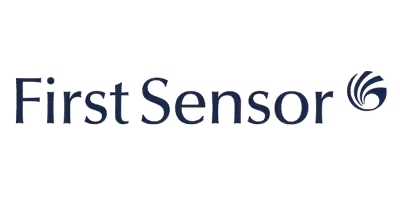
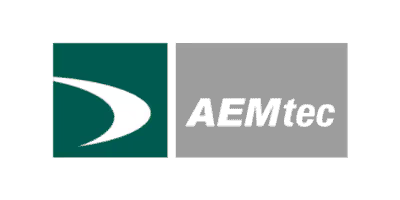

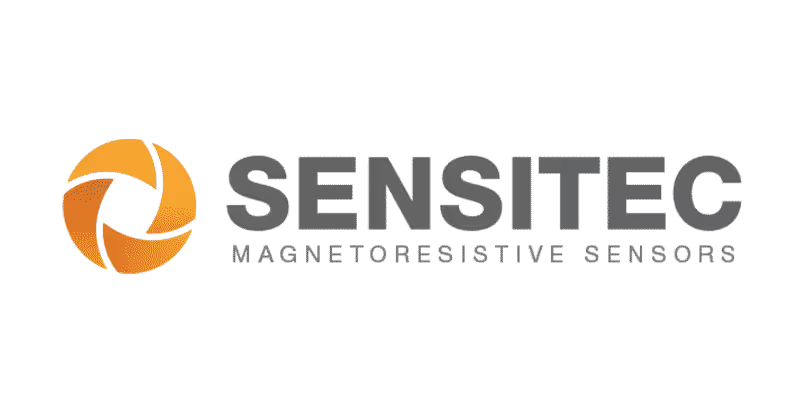
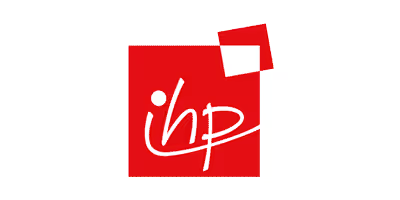
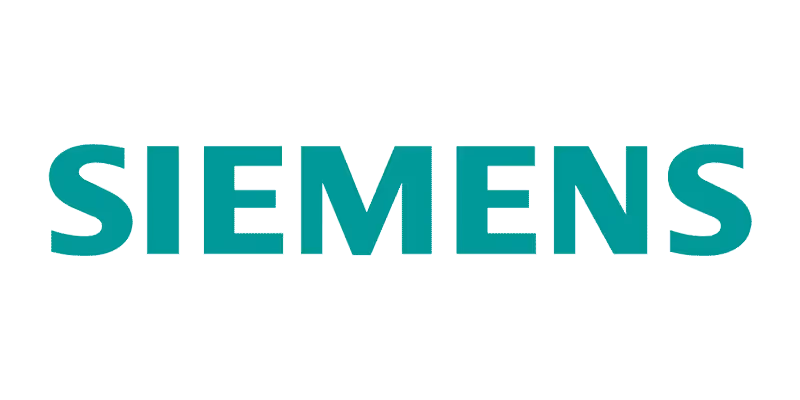
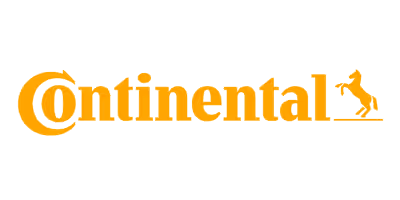
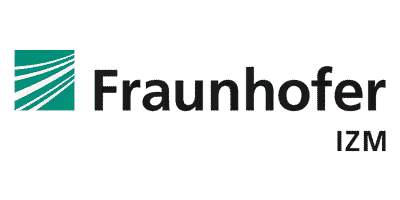
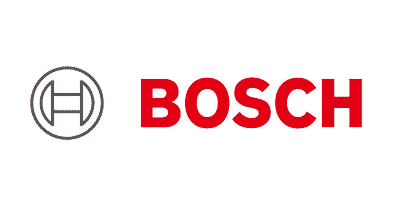
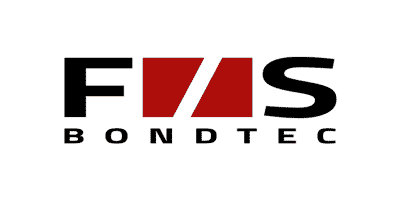
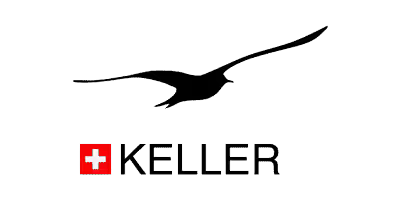
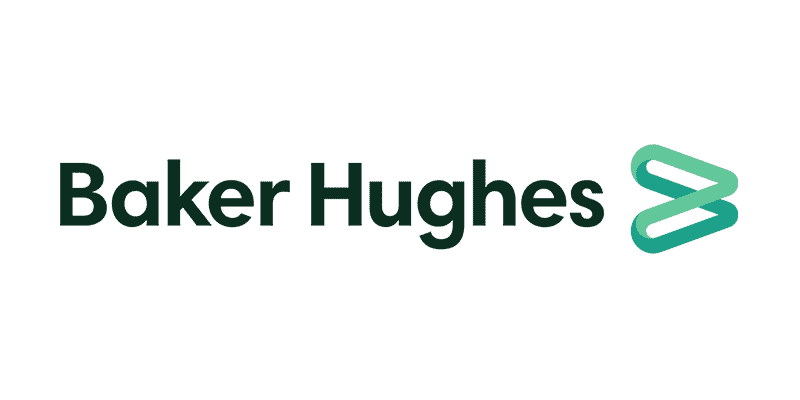
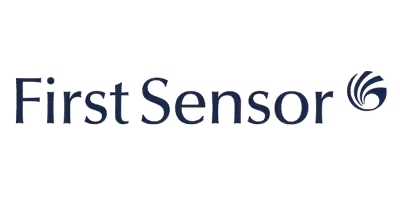
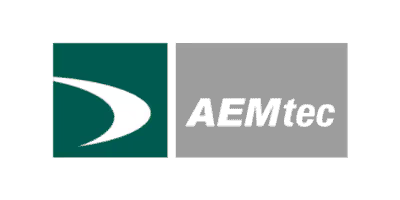

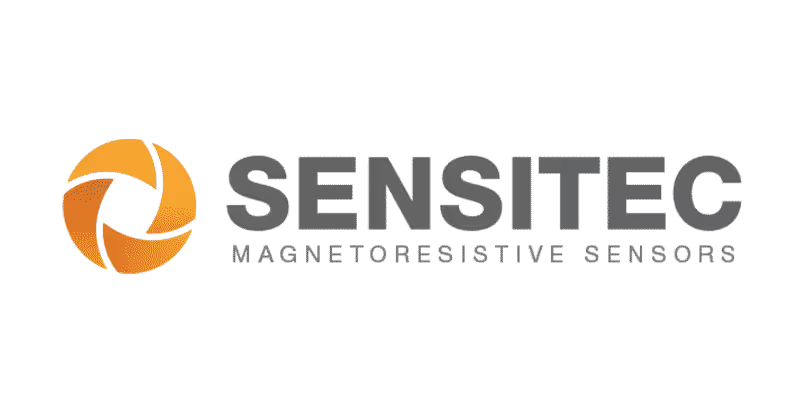
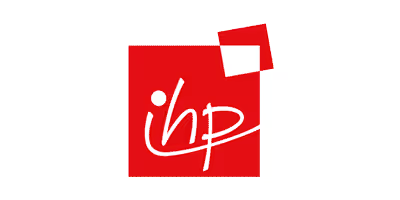
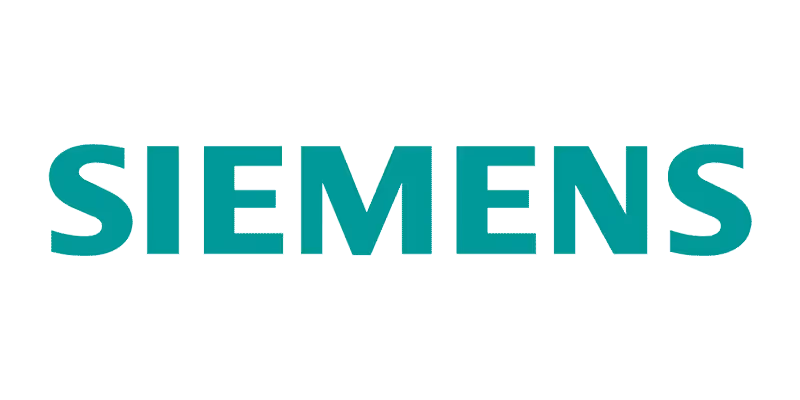
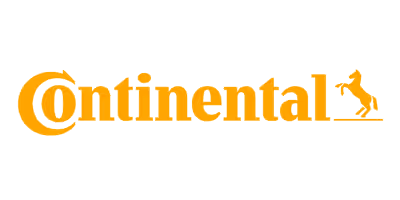
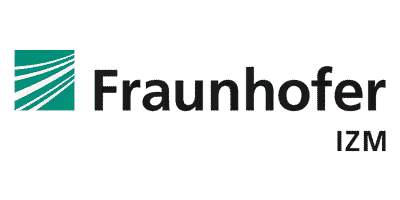
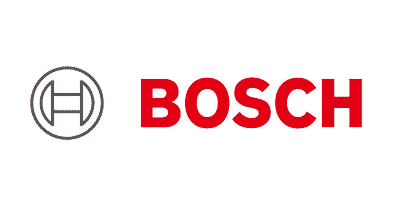
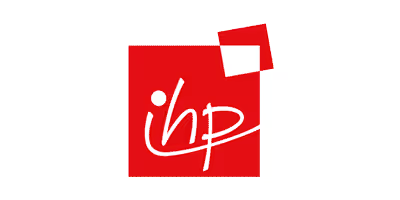
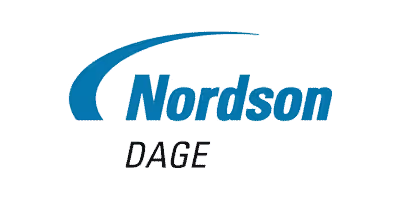
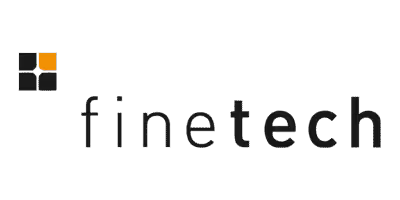
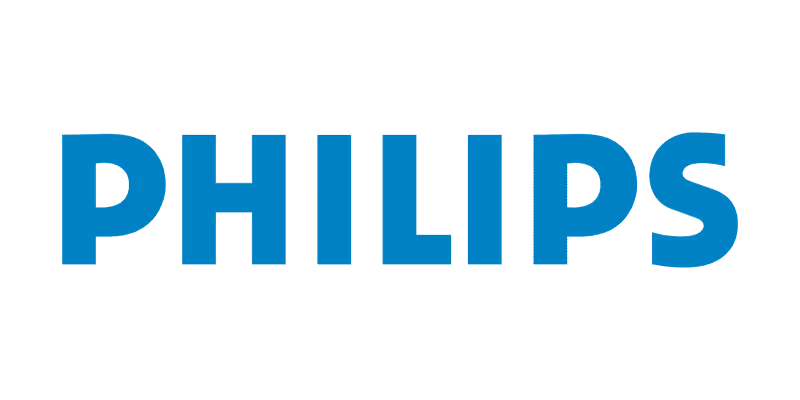
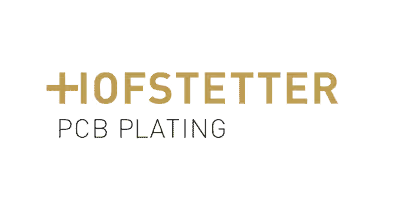
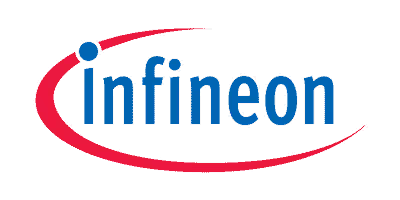
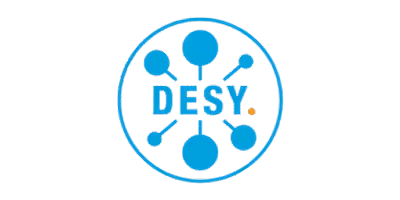
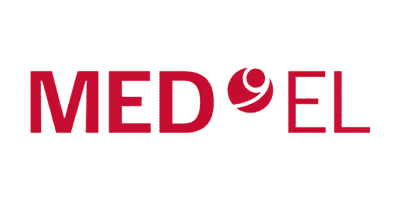
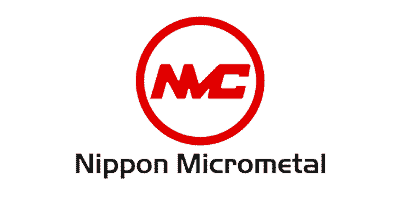
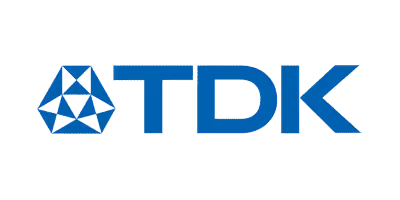
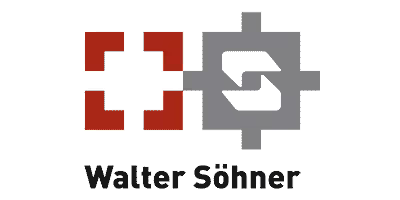
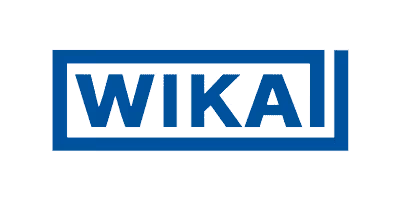
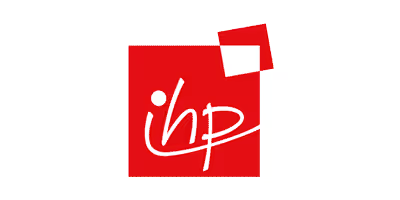
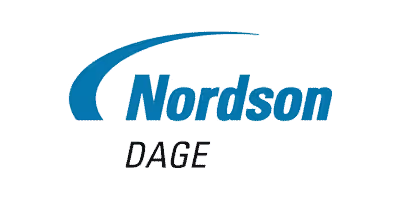
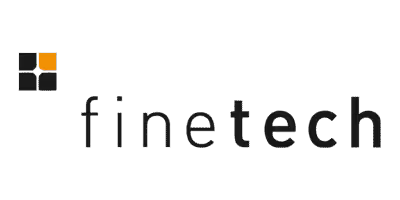
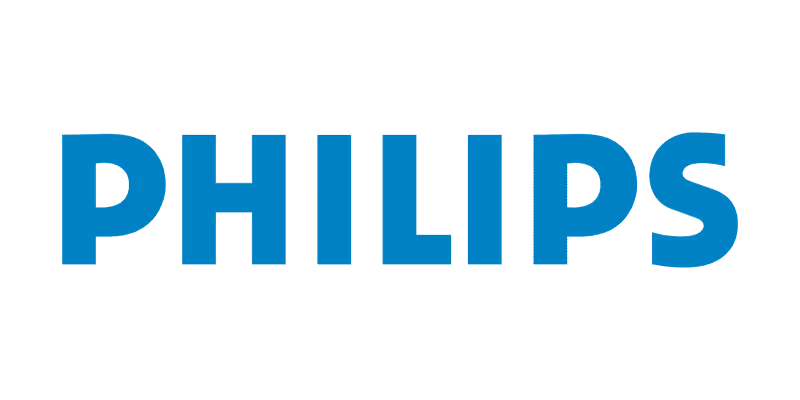
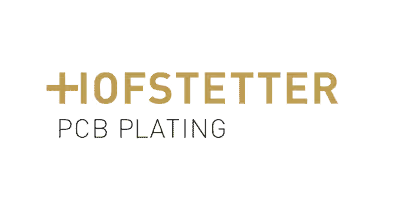
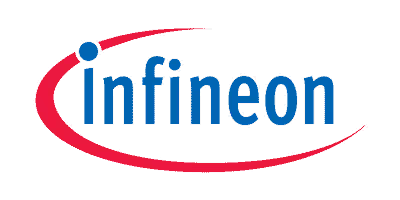
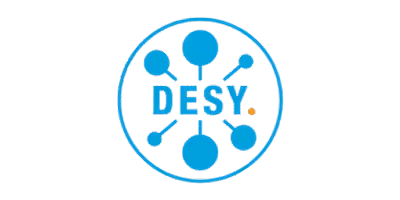
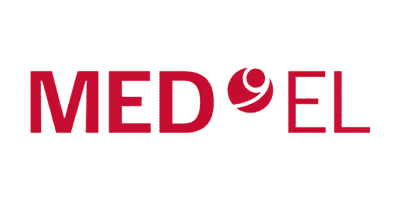
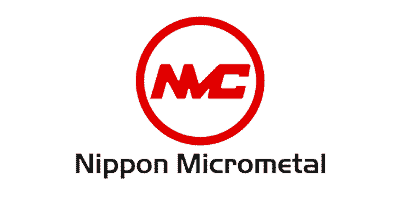
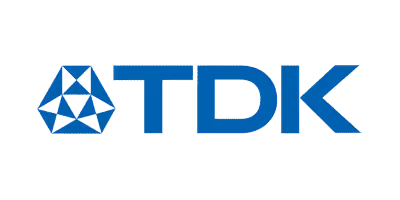
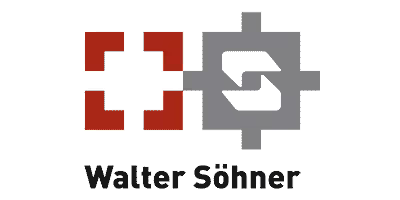
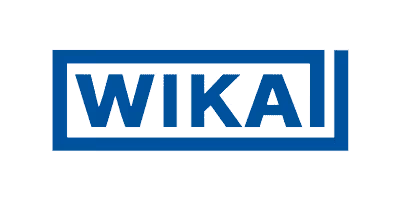
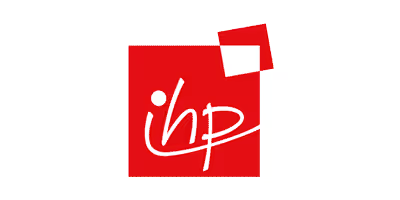
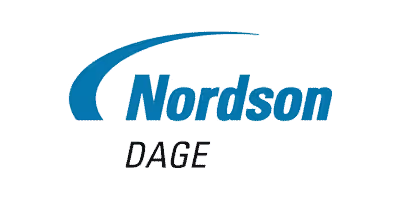
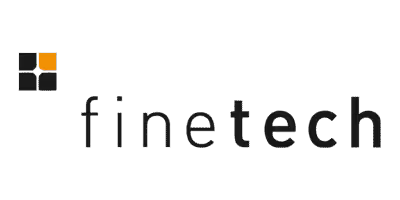
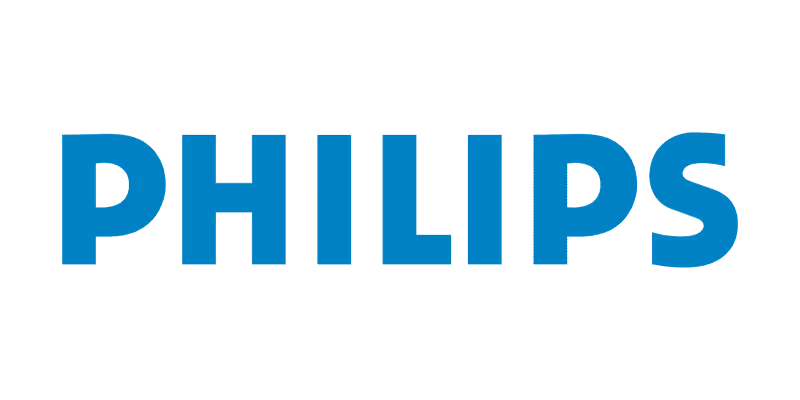
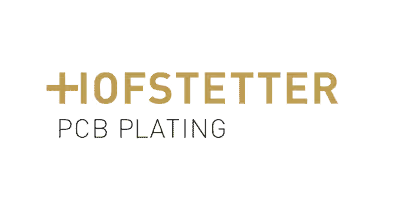
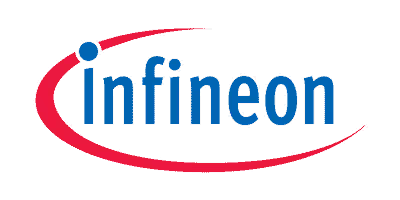
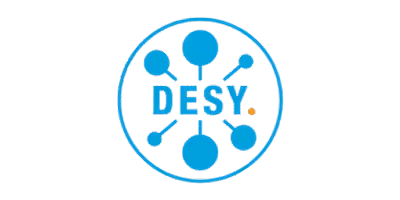
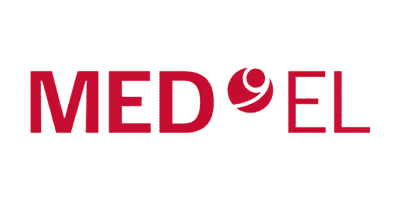
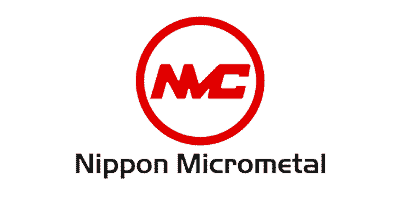
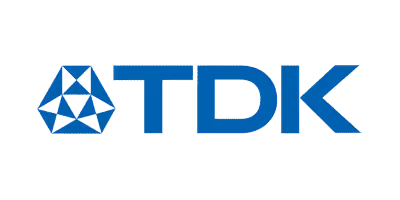
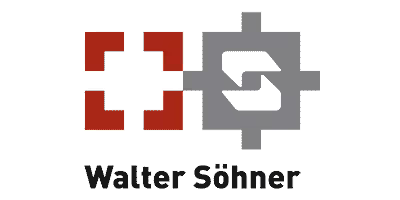
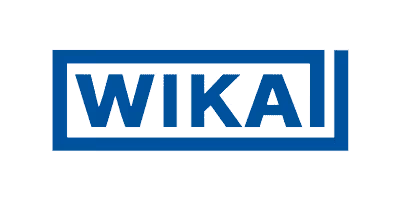
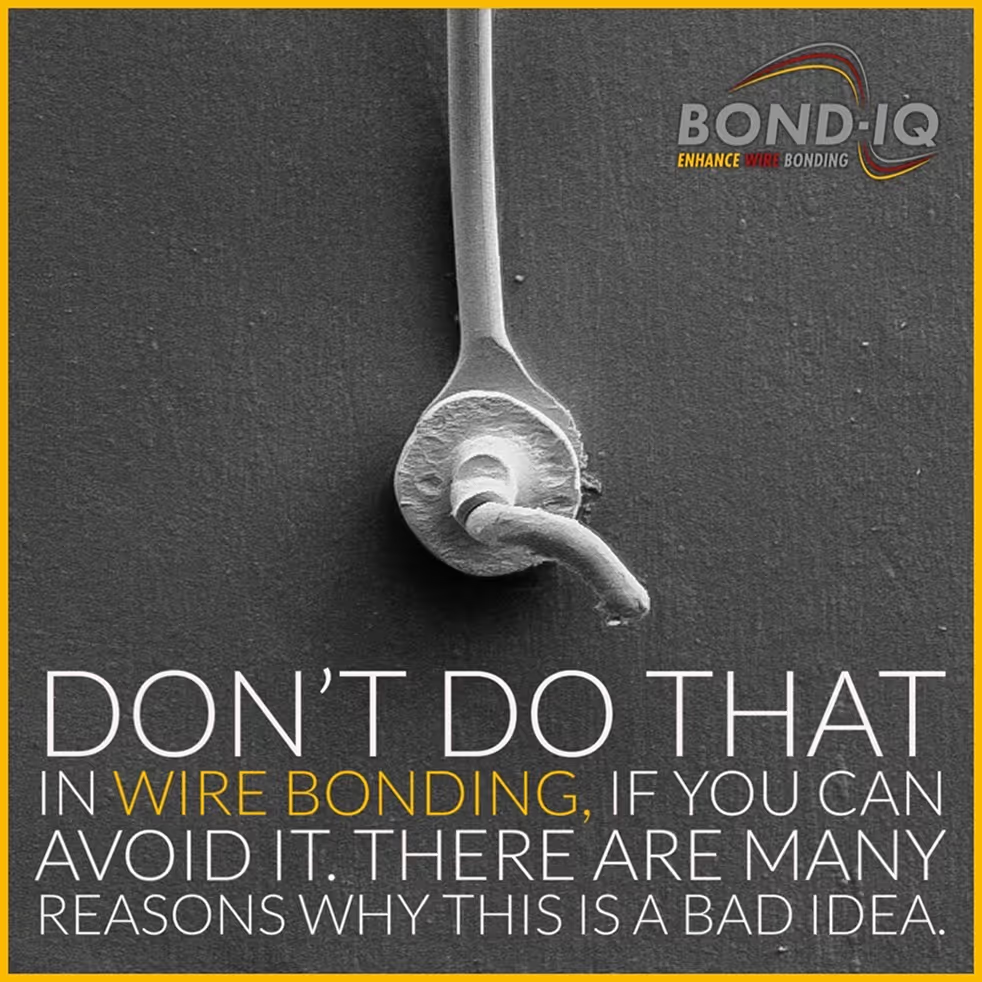
✅ If a wire bond contact cannot be reliably contacted on a surface, then there is a reason for this. Trying to secure this contact mechanically is actually not such a good idea. Or what do you think?
In older processes, I still see the so-called safety bumps (or security bumps) relatively often. The subsequently bonded ball is supposed to fix the wedge/stitch mechanically even better and thus ensure that the required quality is achieved and the product is manufactured sufficiently robustly. This has been proven to work. A pull test on a wedge secured by means of a safety bump usually withstands higher pull forces. All good, actually. But I still don't think it's a good method in terms of a robust process. The following thoughts on this:
💣 First of all, the root cause of the poor bond quality is not fixed. The problem gets a band-aid 🩹🚑🤕 on it. A bug fix without fixing the bug. The most common cause...contamination of the surface with any dirt from the manufacturing or pre-processes. So better get rid of it and bond on clean surfaces.
💥 What do you do if the wedge doesn't bond on the surface? Correct - you crank the parameters up. As a result, a capillary imprint is often left on the surface and destroys the metallization. The safety bump is now placed on this destroyed area. This is not a good basis for a robust contact.
📍 Where do you actually place the ball optimally? There is a regular discussion about this. Sure, you can optimize that by means of pull tests. But what if the position of the safety bump varies? Its safety function depends very much on where exactly it is placed. The problem: If it is placed incorrectly (or is even missing and this is overlooked), the contact is electrically ok and is delivered to the customer. Mechanically, this contact is then far from robust.
So what would be the better strategy?
Look at your process and solve the root causes of the problems. Acquire the necessary know-how so that you don't have to deal with such problems by fixing bugs. Train your staff well so they can find bugs and determine root causes. No matter how you do the math - good training always pays off!
⭐️ "An investment in knowledge always pays the best interest." (Benjamin Franklin)
⭐️Or just turn it around and make it a stitch-on-bump (SOB, SSB, BSOB) process. Yes, this process also requires a longer process time. But it is a much more defined process. Feel free to discuss it in the comments.