Efficiently perform failure analysis. Identify root causes faster.
You can rely on our expertise in wire bonding and the interpretation of analysis results. Our focus on this technology is your advantage. When it comes to wire bond connections, you can count on us for specific statements and interpretations.
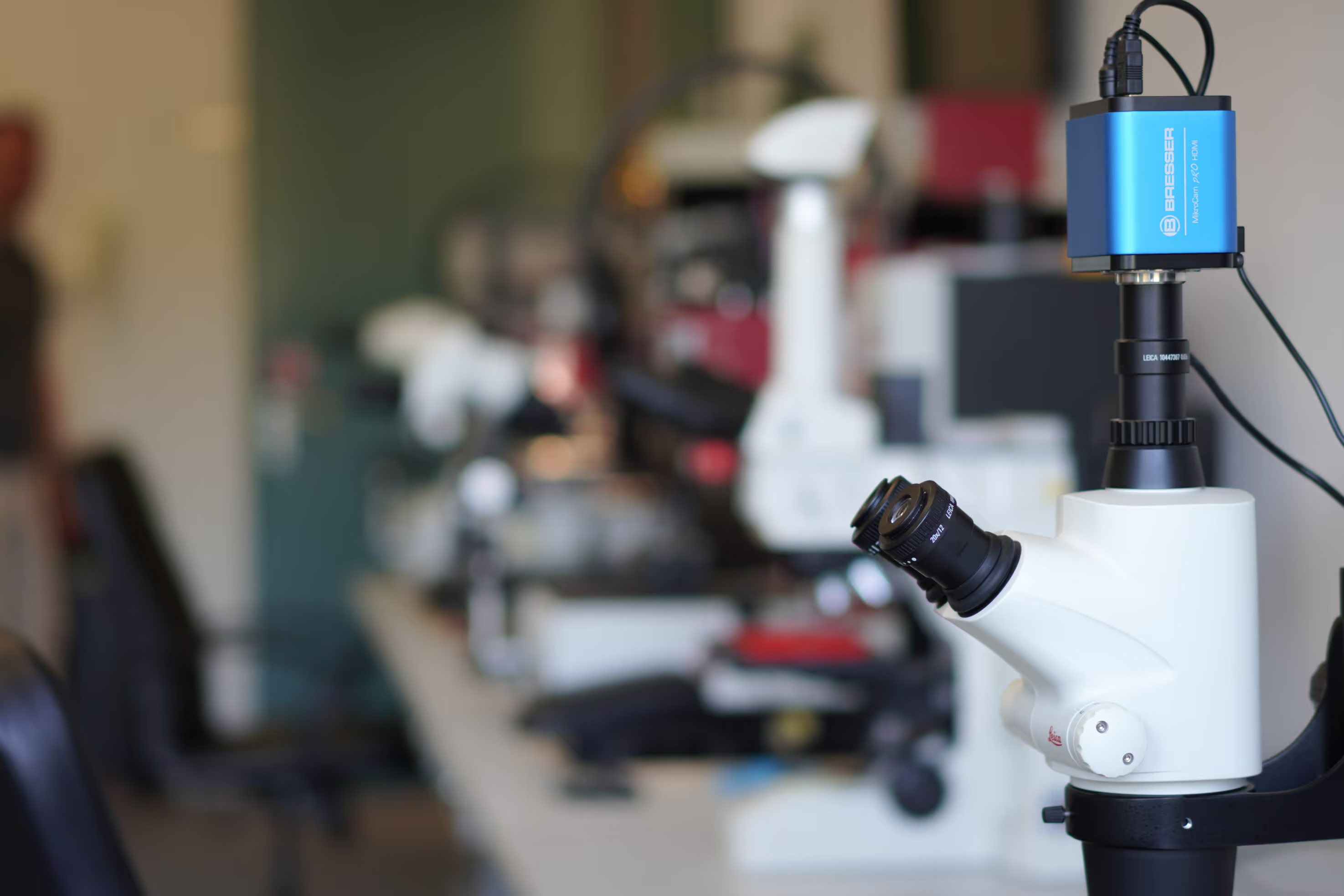
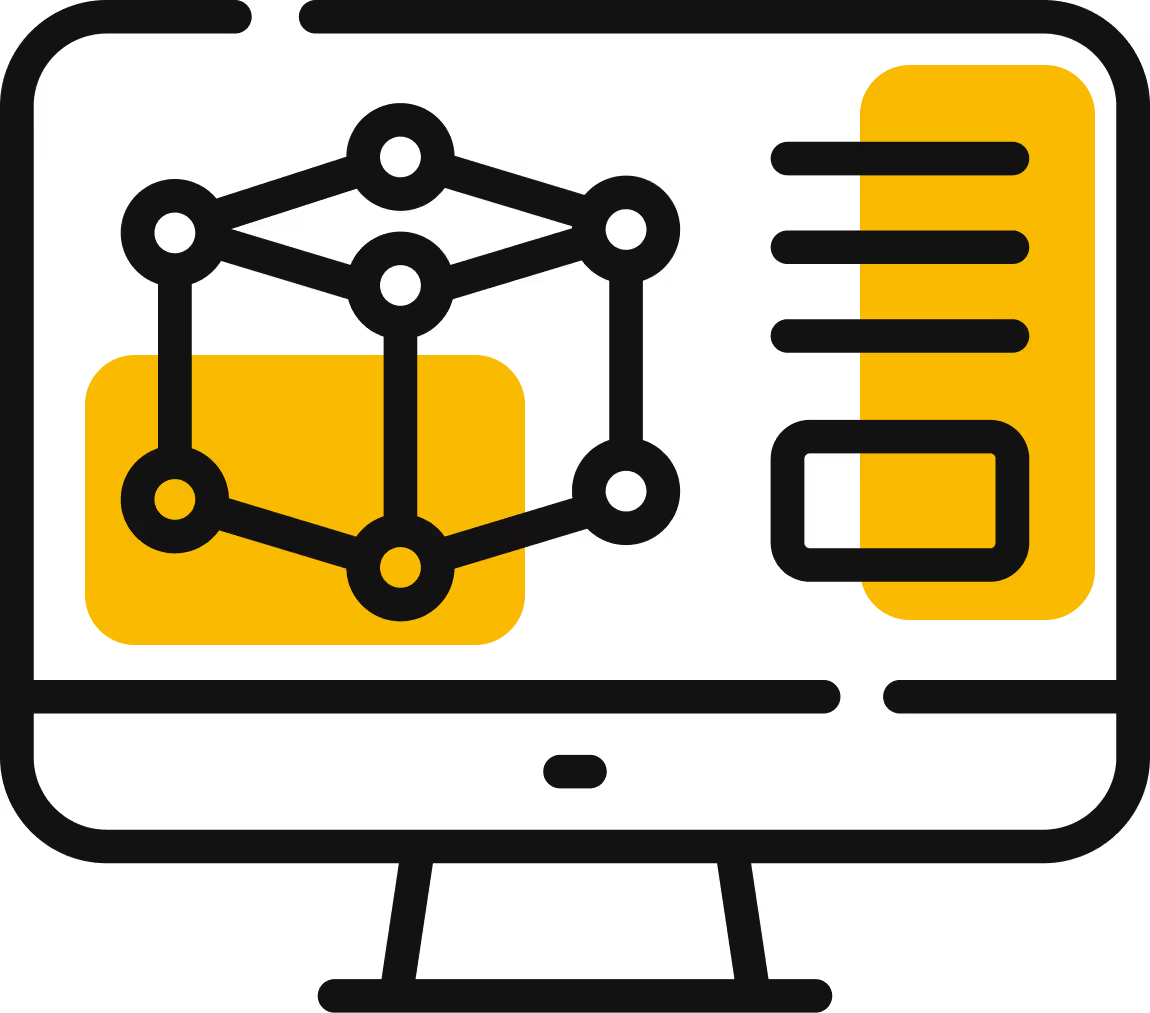
Transforming Analysis into actionable Insights
When an error occurs, it is usually important that the first analysis results are available quickly. However, the interpretation of the results and their implications for further analysis and process settings is much more important.
You can rely on us to know exactly how wire bonding works and how to interpret the analysis results. Our deep focus on this technology is your advantage. When it comes to wire bonding, you get specific statements and interpretations from us.
It is helpful to receive an analysis report from a laboratory that summarizes the results. But it is even better to get direct recommendations for your process or product from technology experts, which will help you reach your goal faster and more reliably.
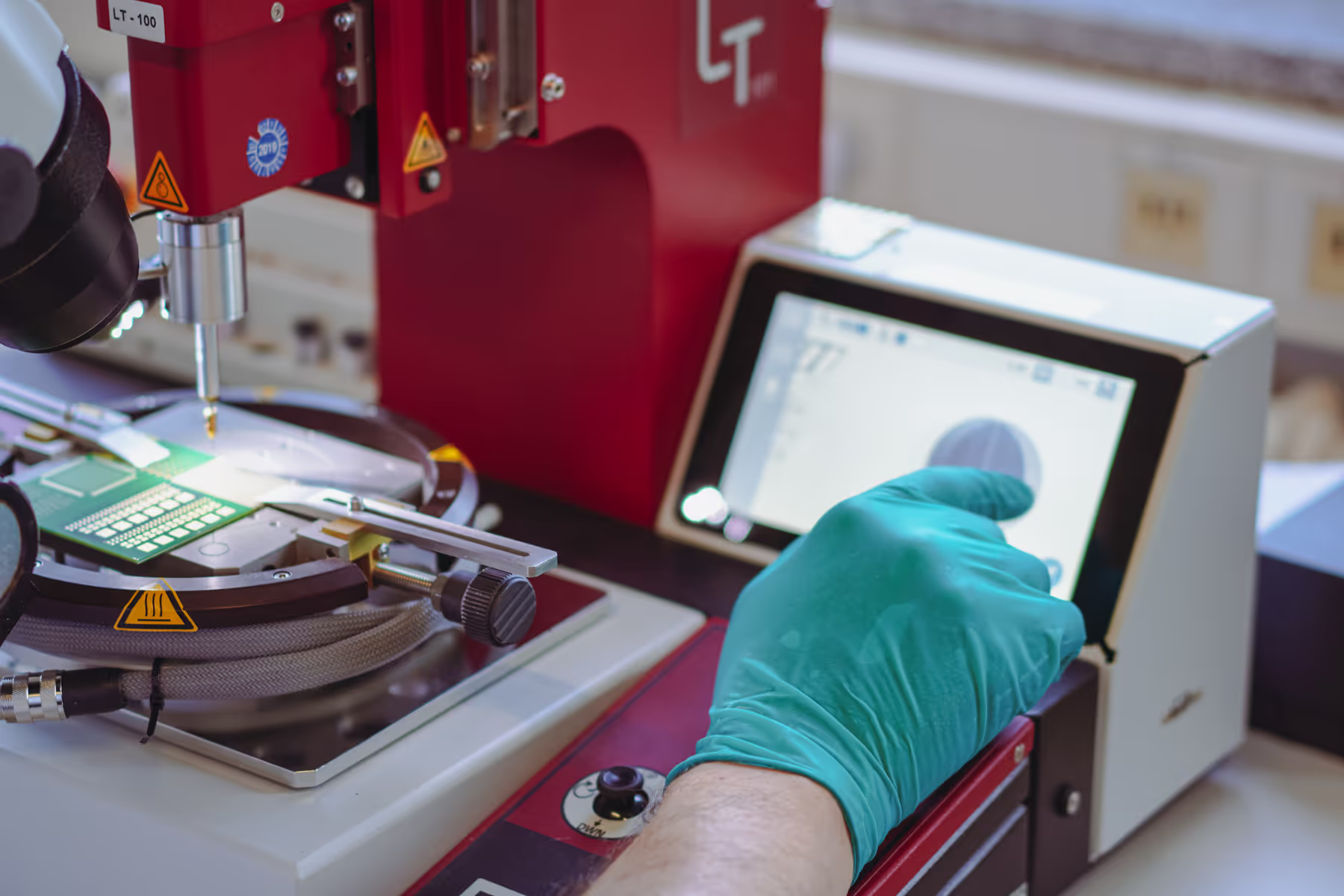
Methods generally used for failure analysis
Typical situations in which our customers request support
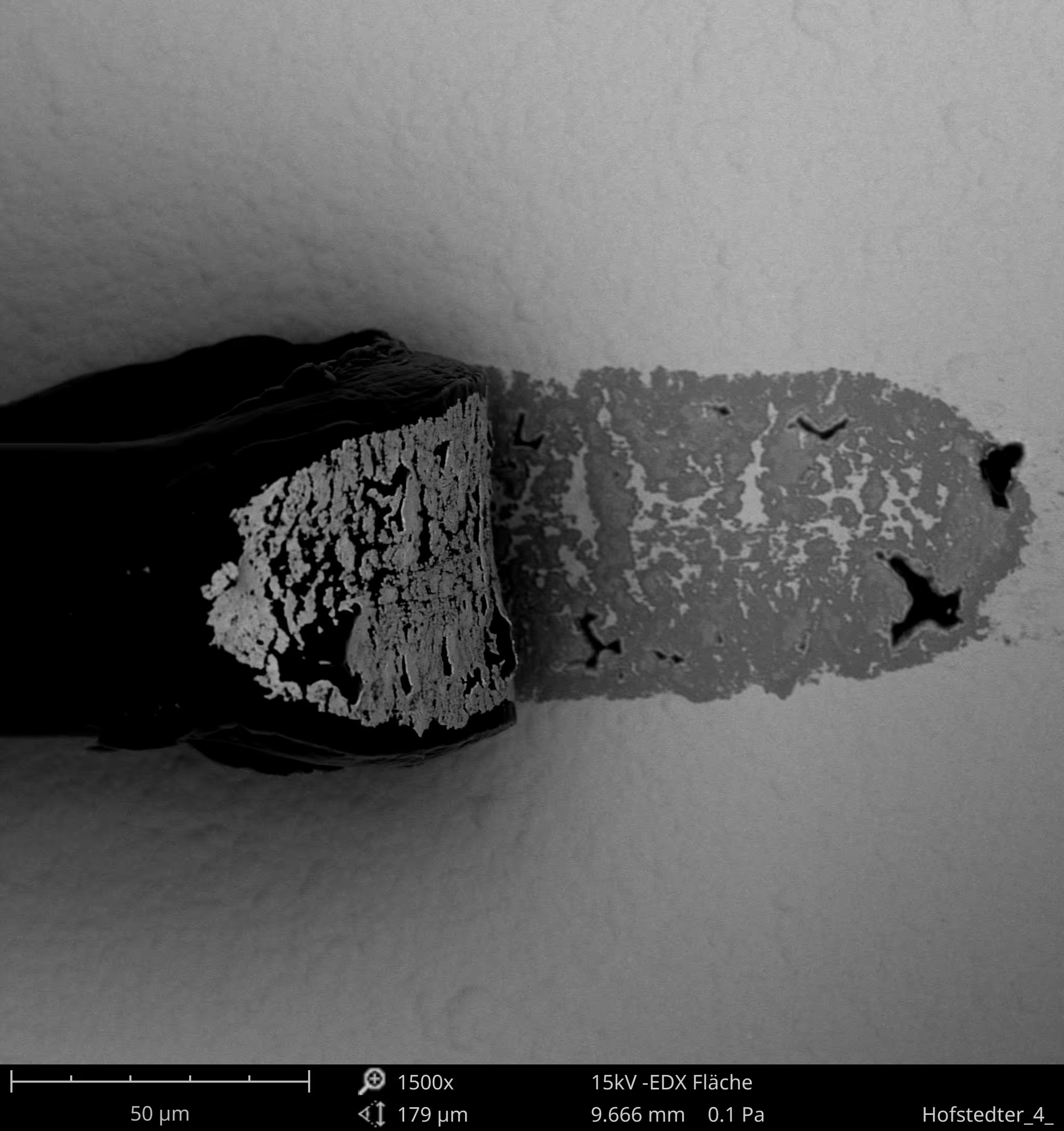
Request a remote consultation today
Failure Analysis
With more than 20 years of experience in failure analysis of wire-bonded assemblies, we have seen many causes of field failures, some of them complex. You benefit from our ability to quickly narrow down the causes and avoid unnecessary activities.
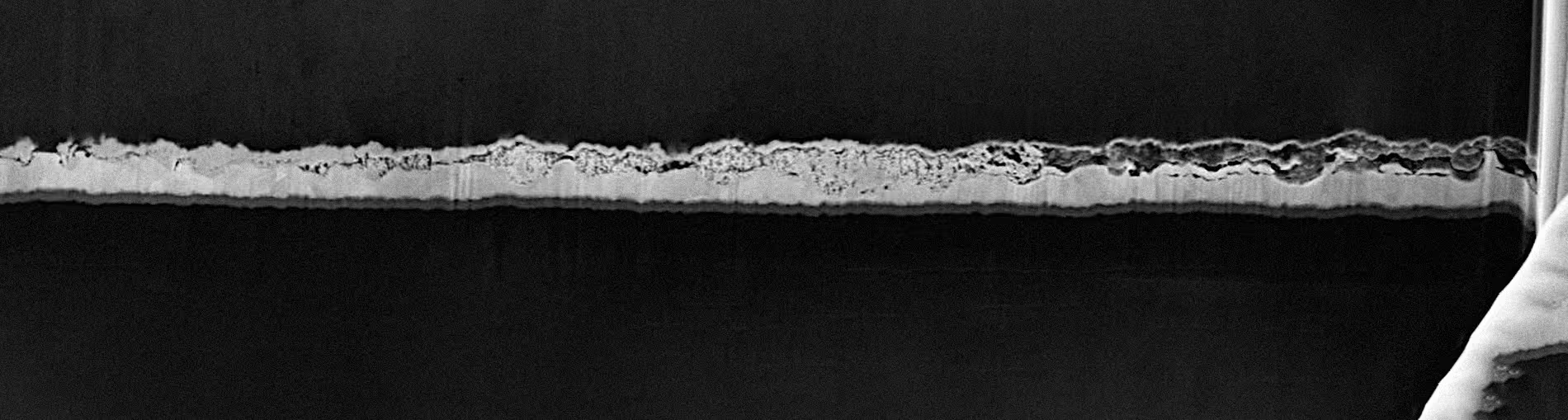
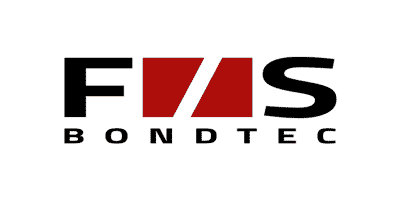
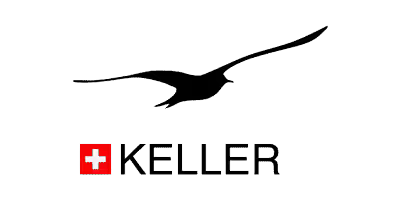
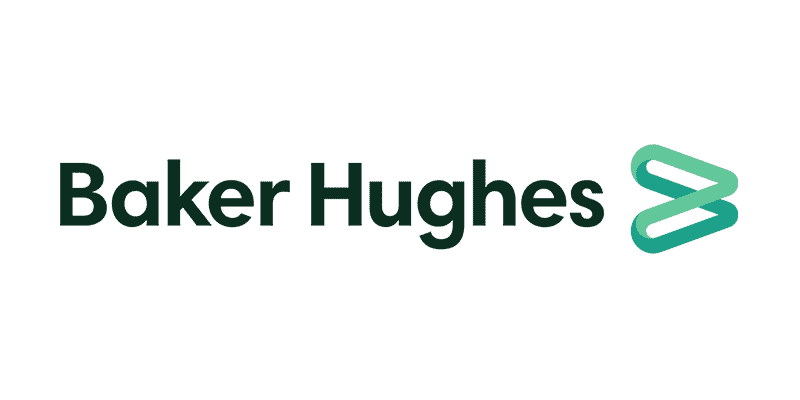
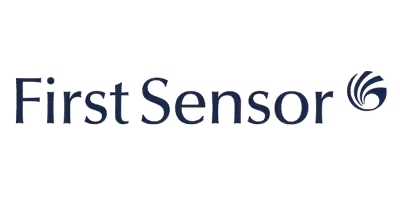
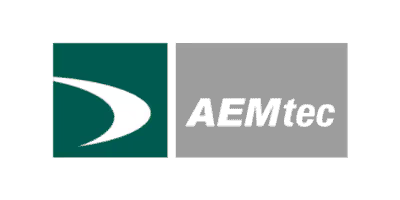

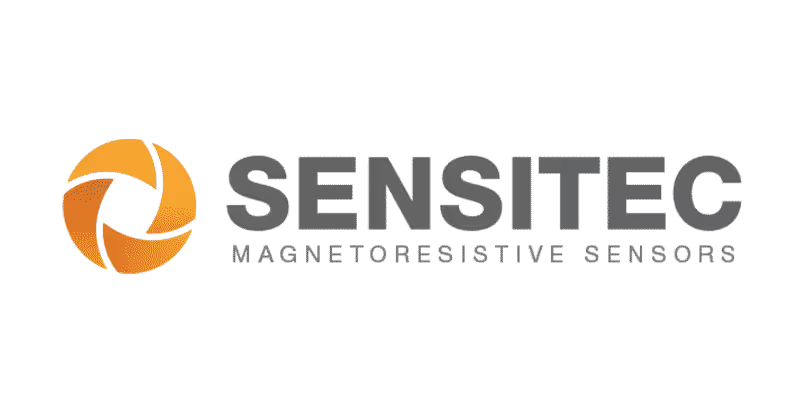
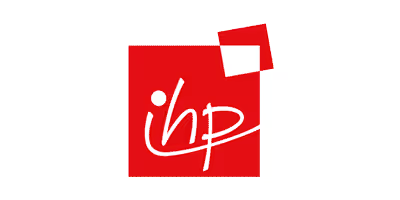
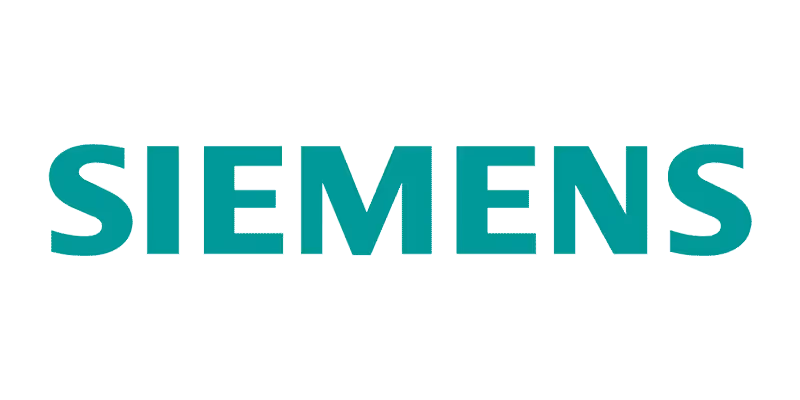
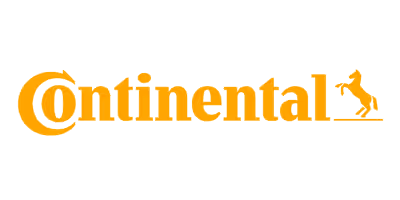
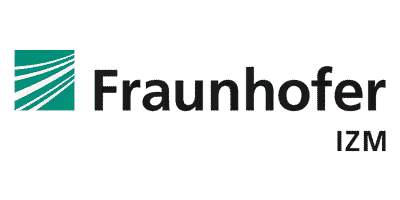
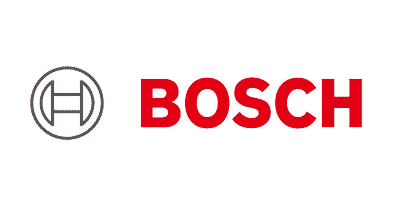
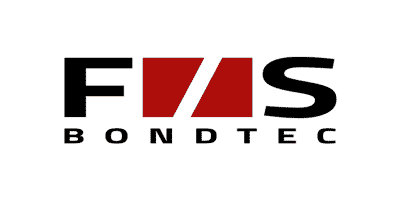
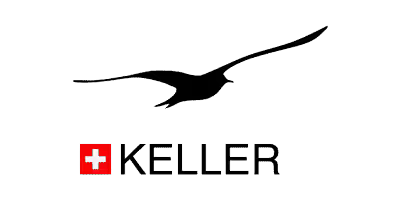
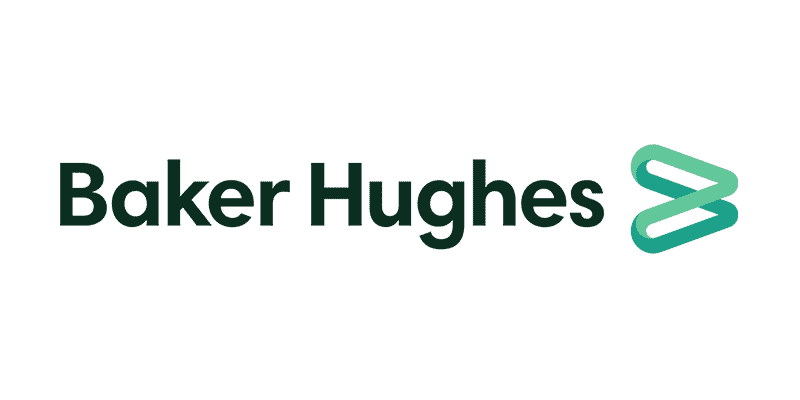
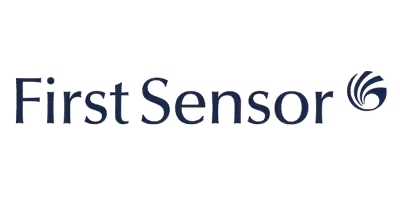
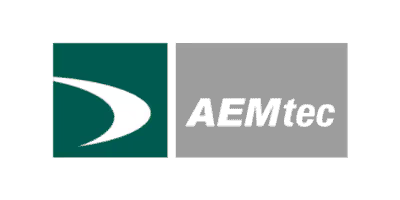

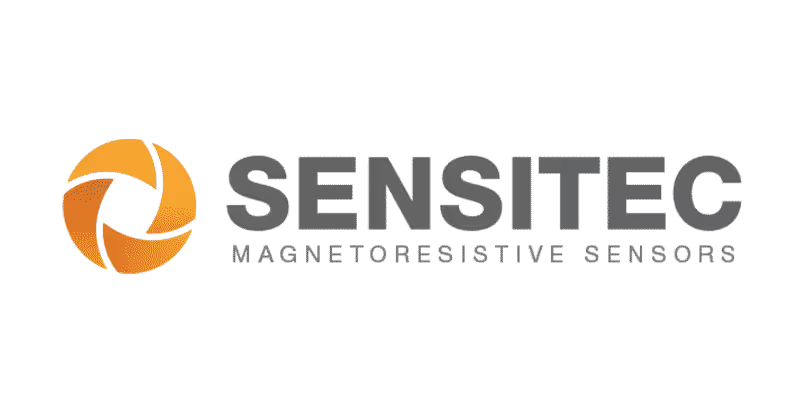
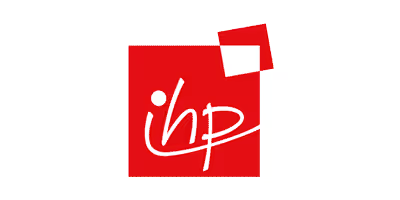
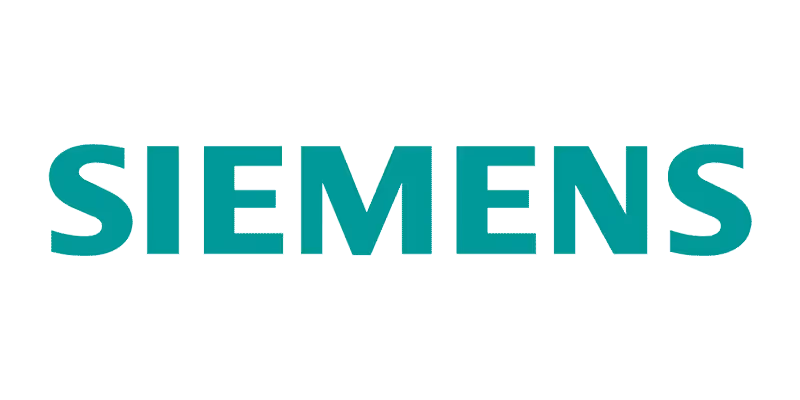
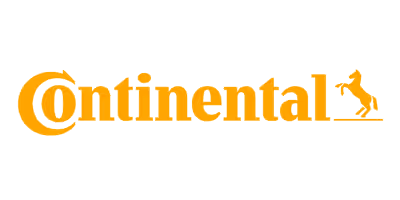
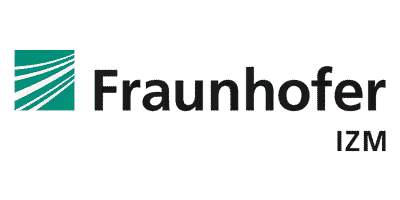
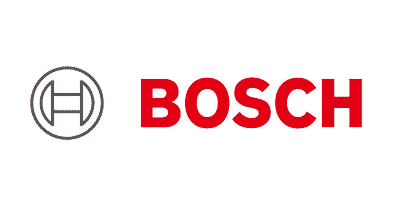
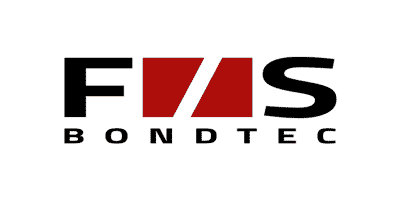
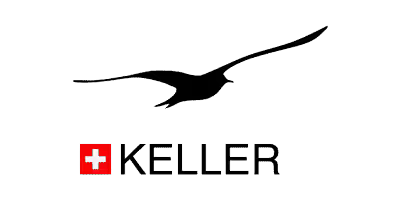
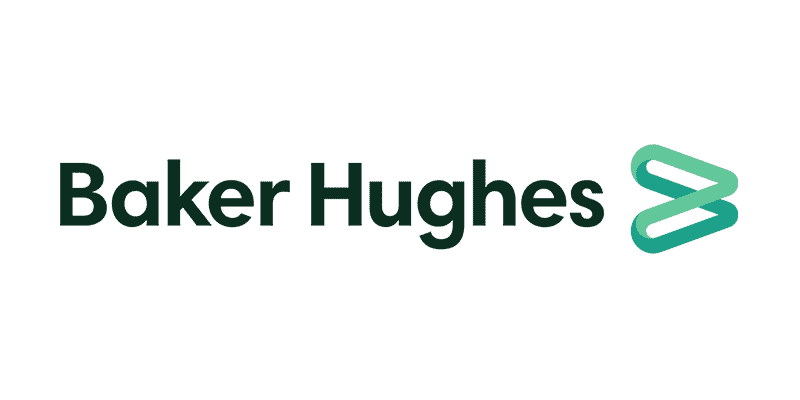
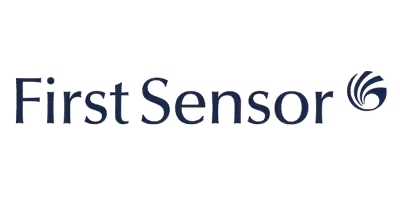
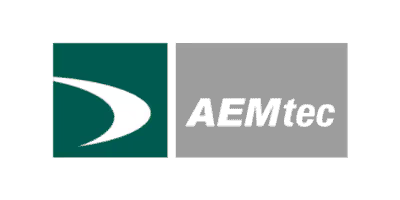

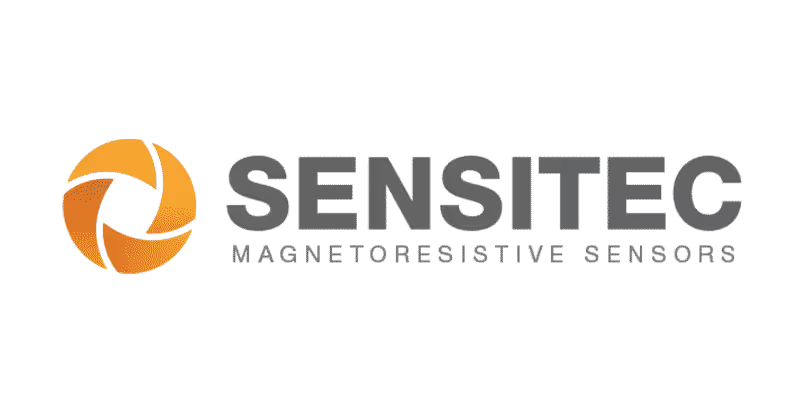
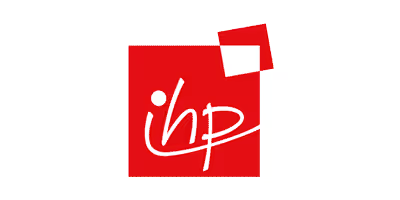
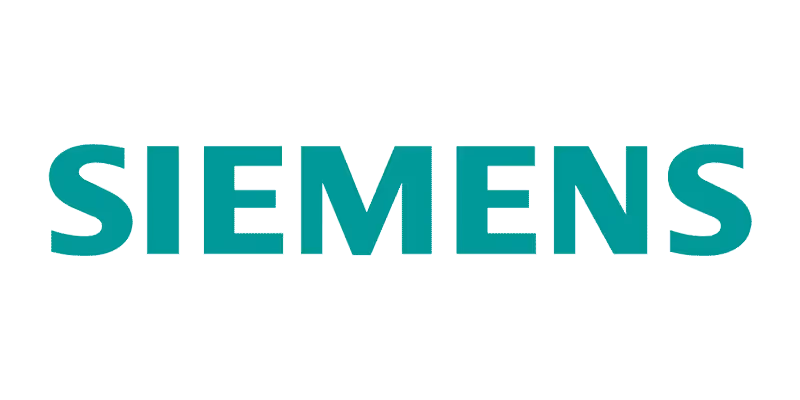
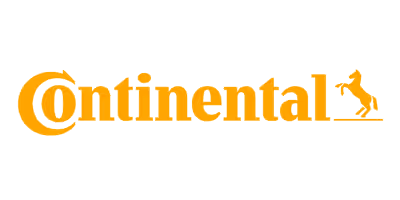
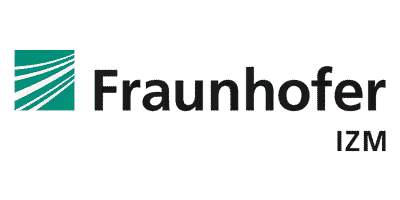
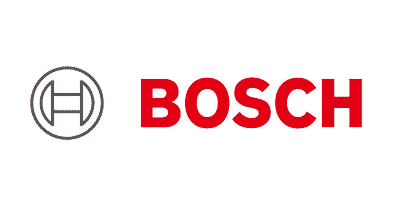
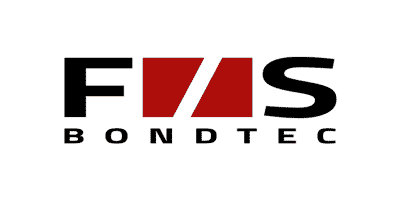
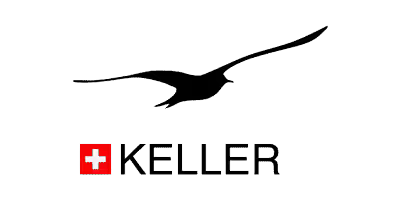
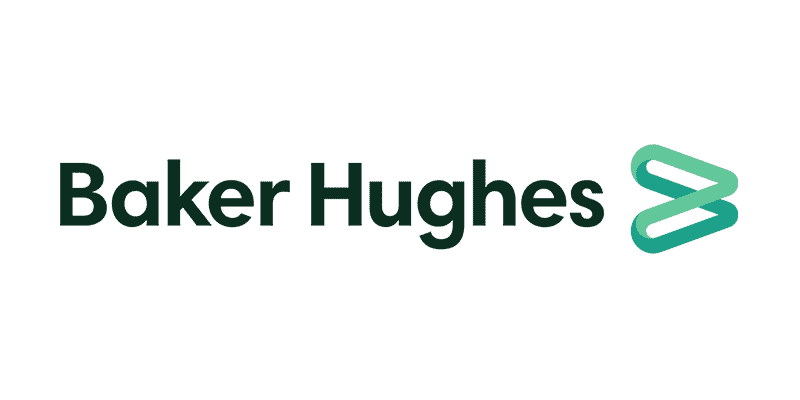
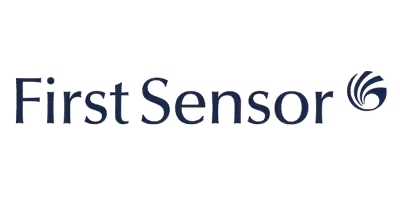
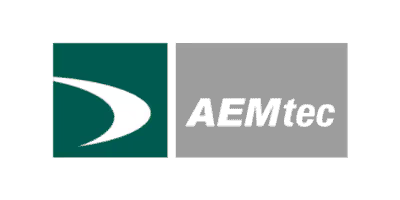

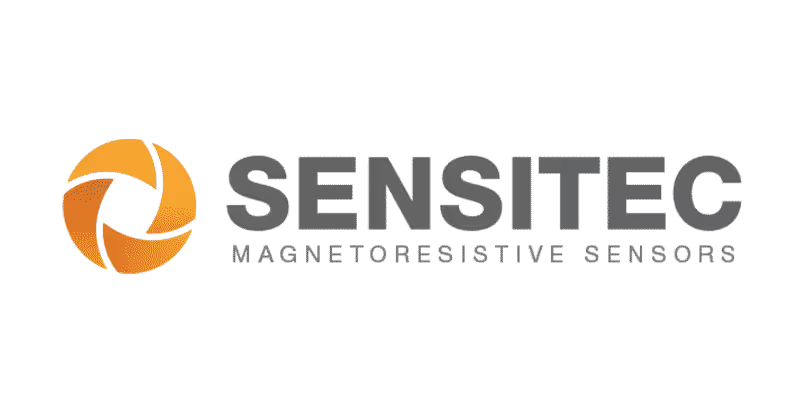
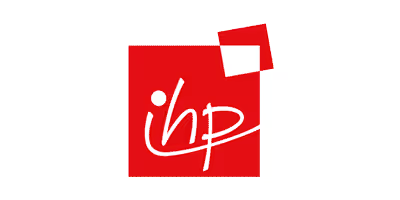
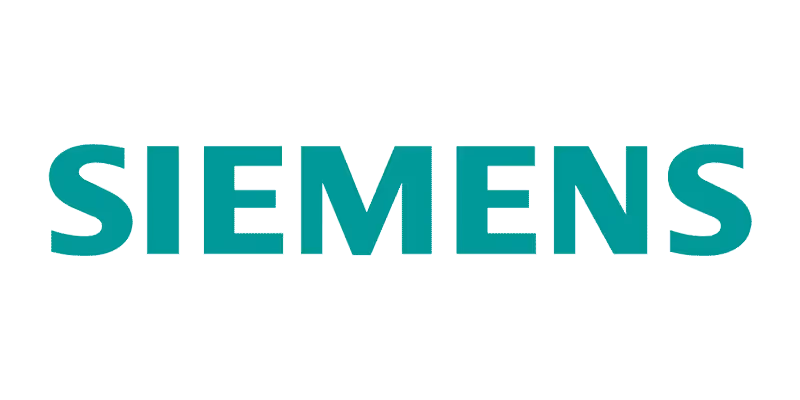
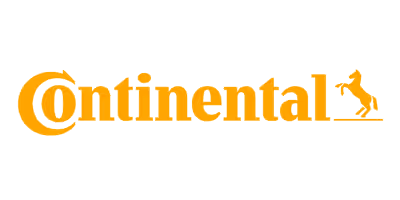
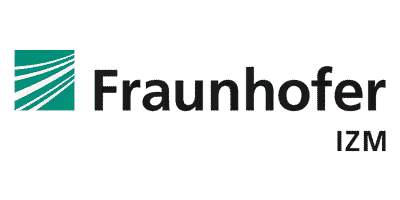
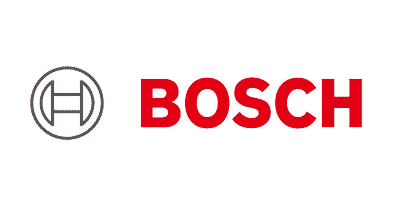
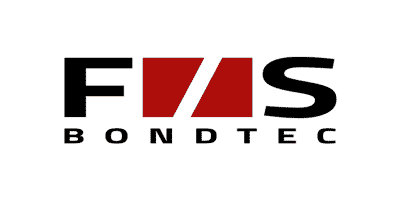
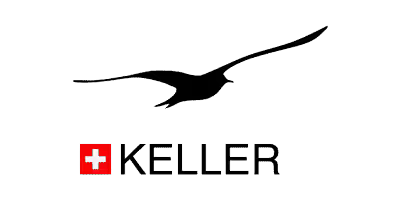
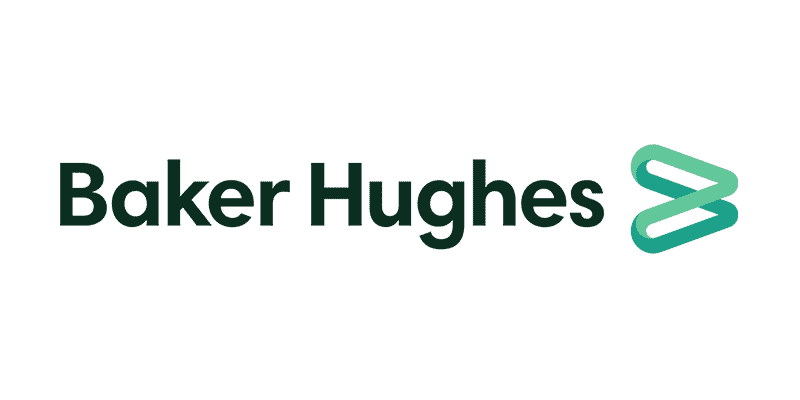
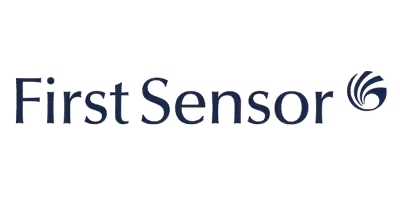
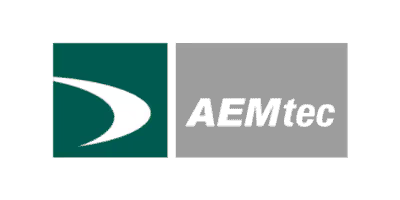

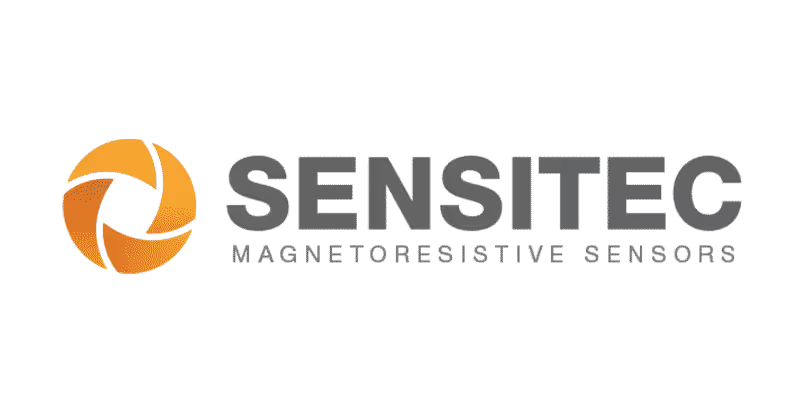
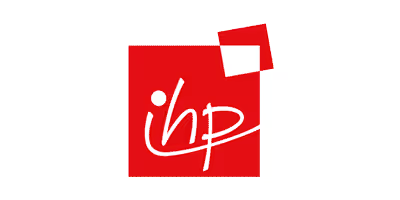
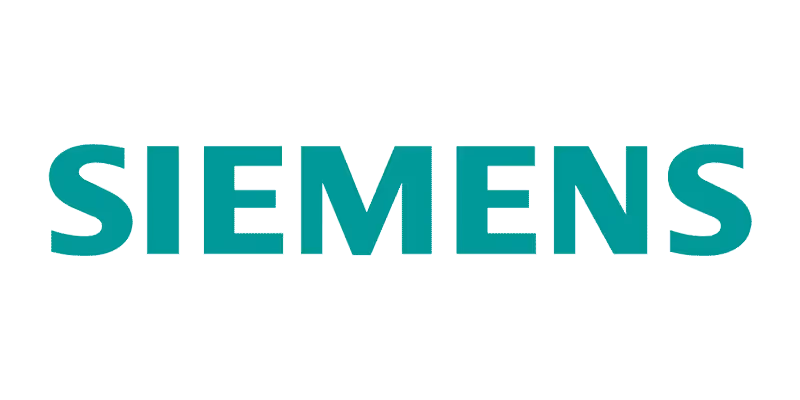
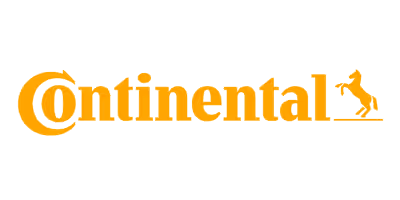
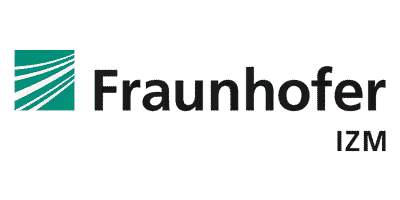
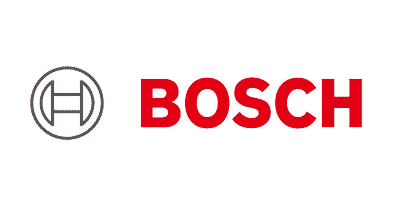
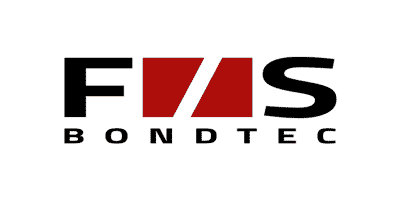
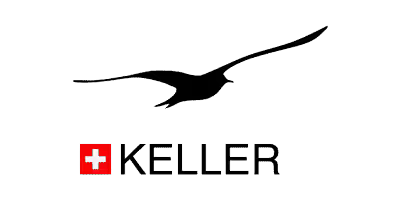
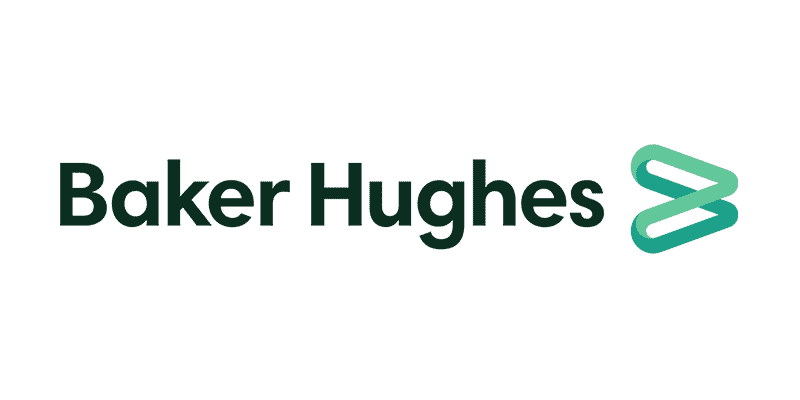
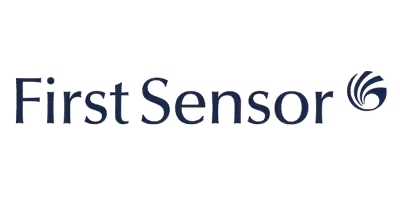
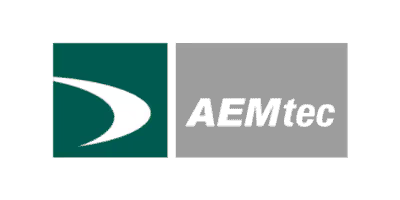

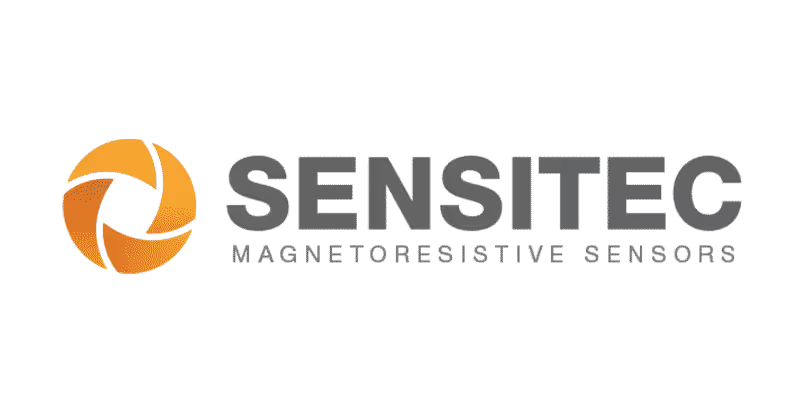
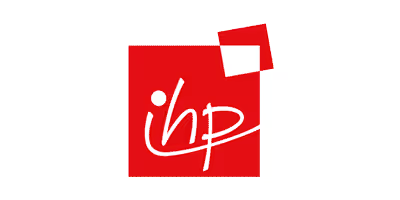
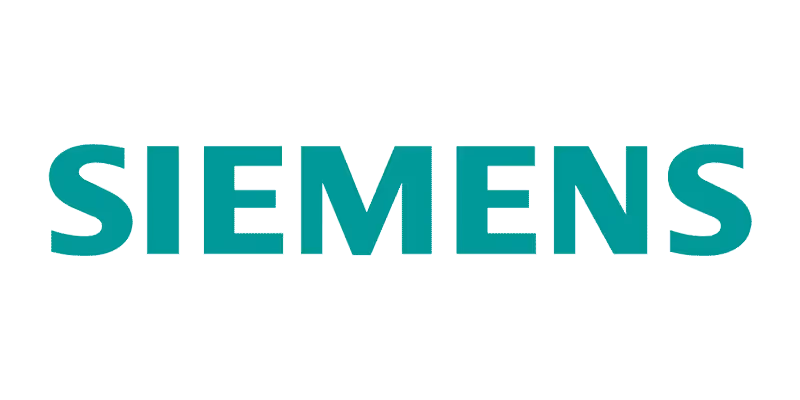
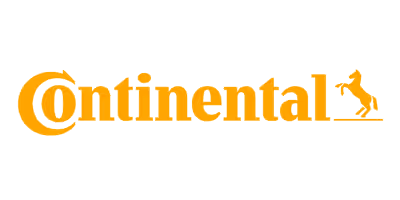
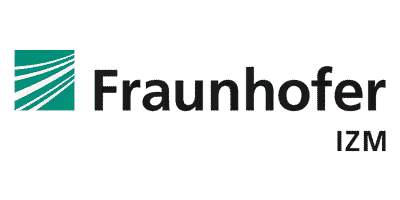
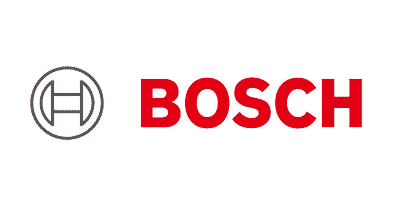
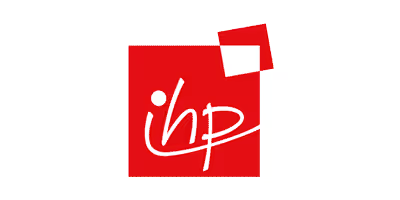
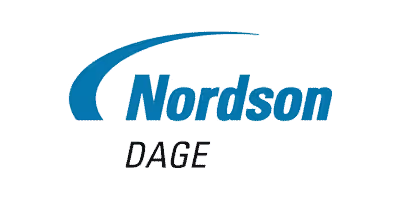
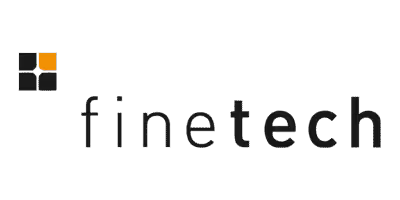
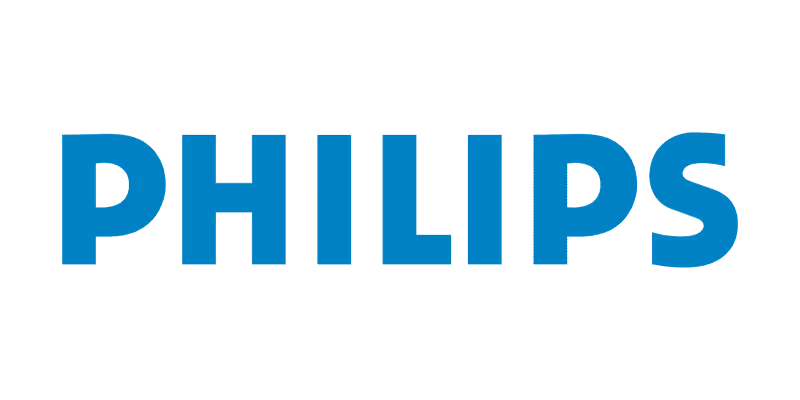
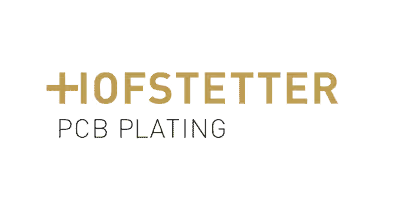
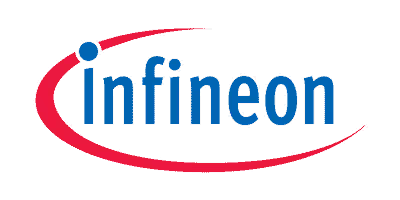
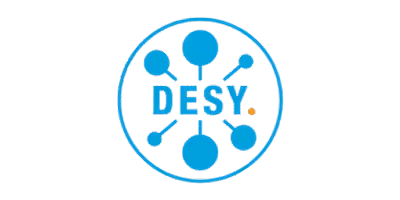
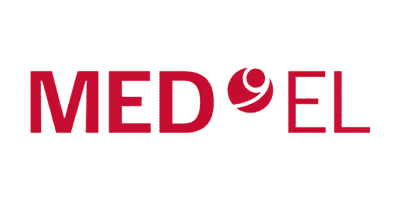
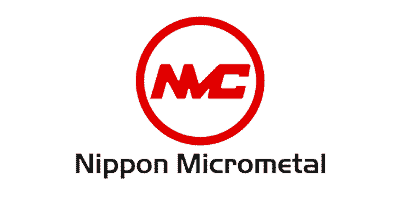
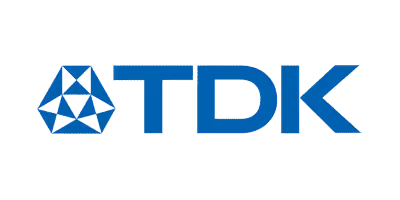
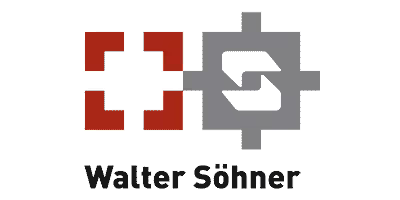
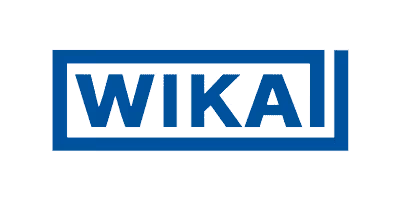
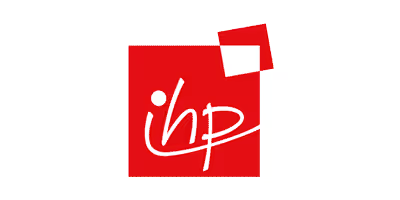
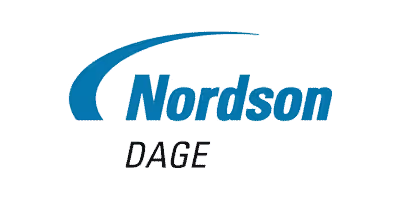
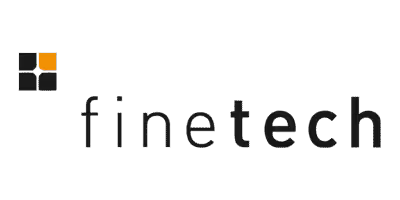
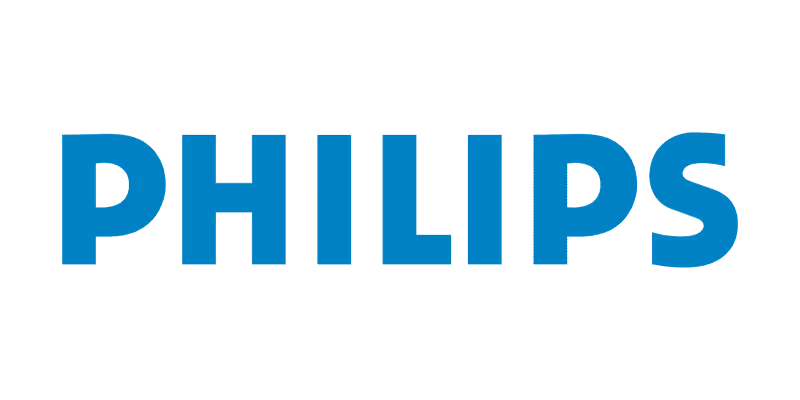
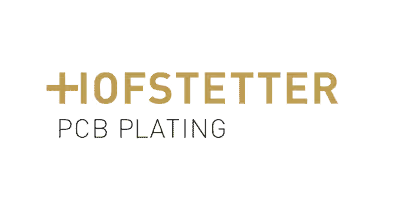
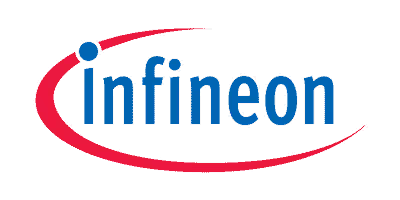
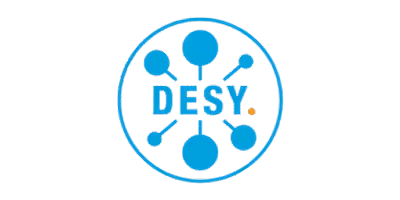
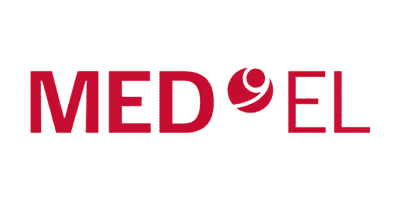
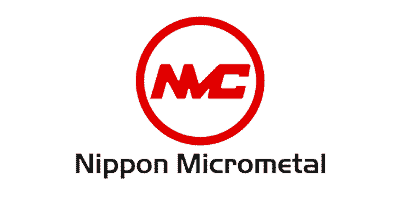
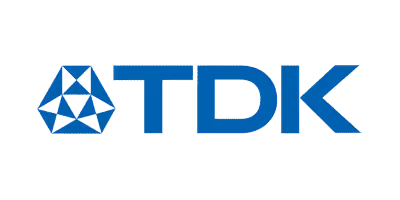
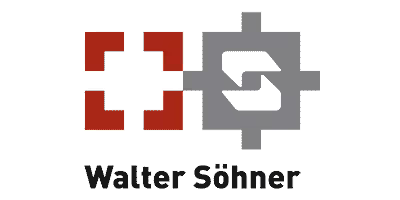
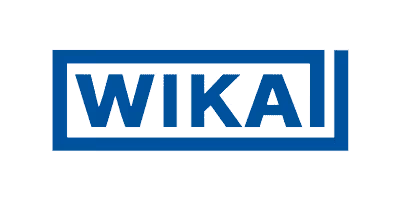
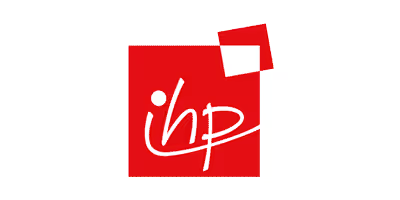
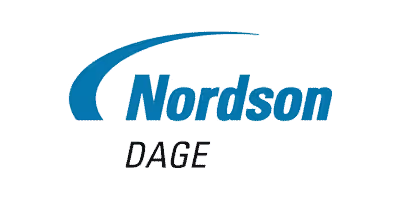
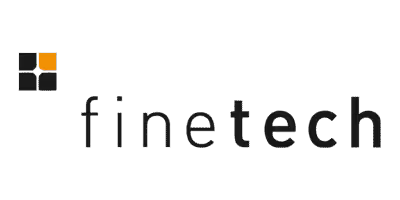
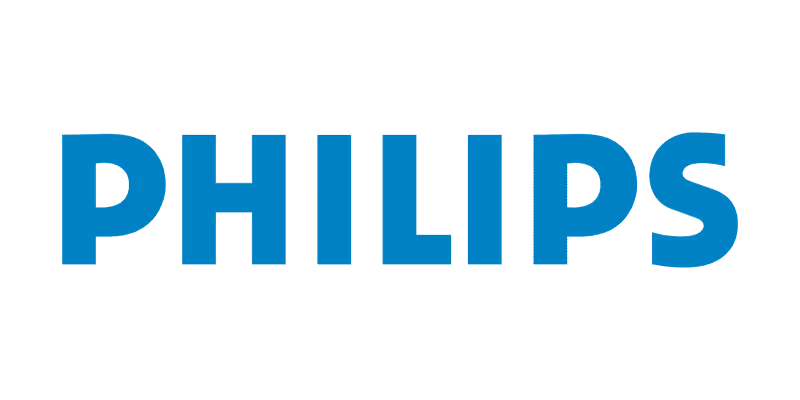
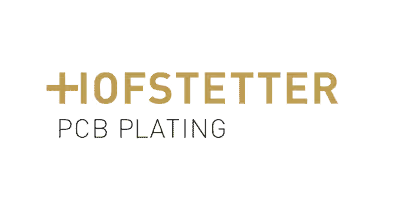
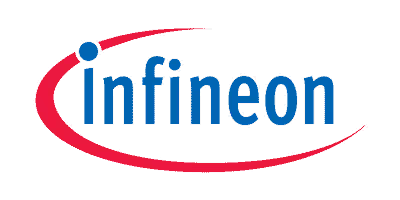
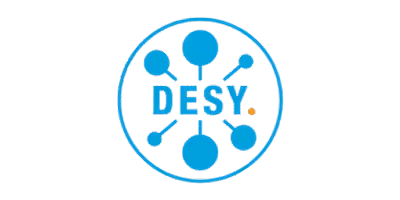
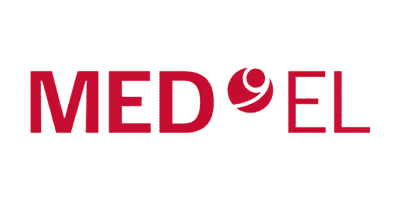
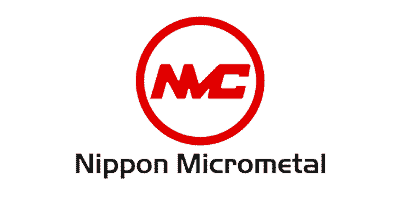
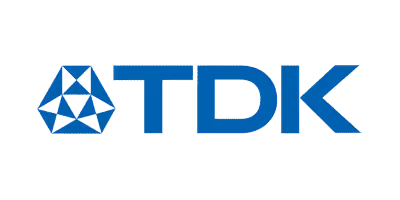
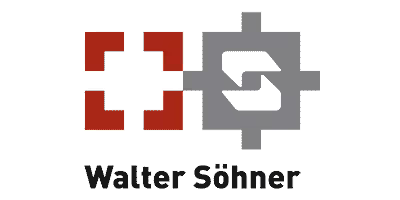
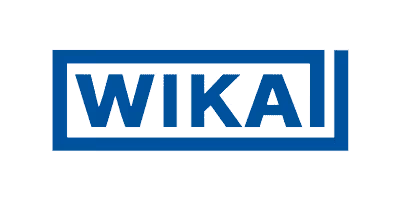
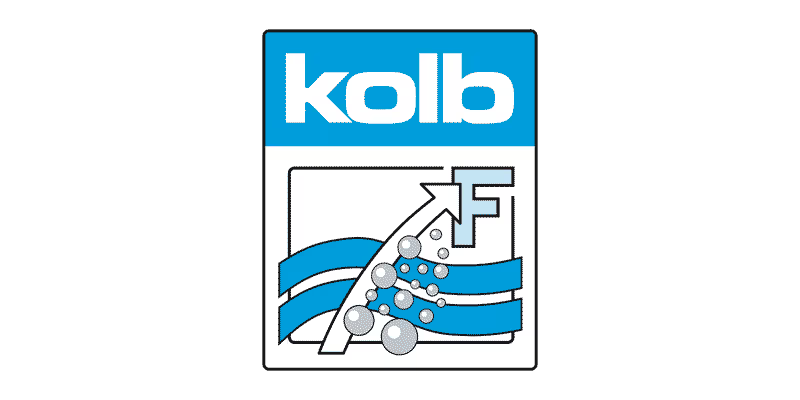
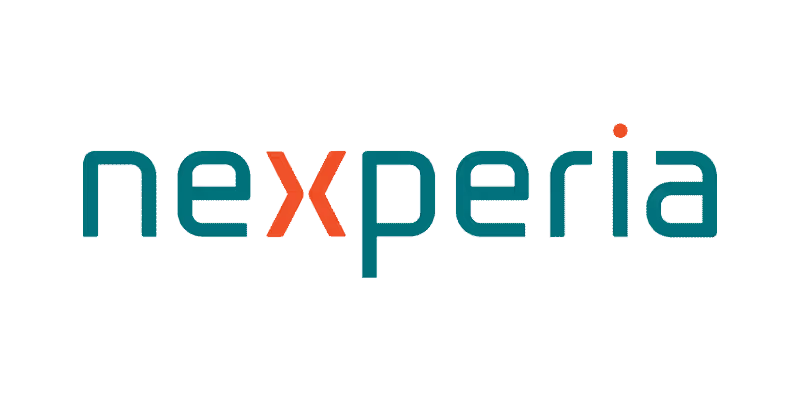
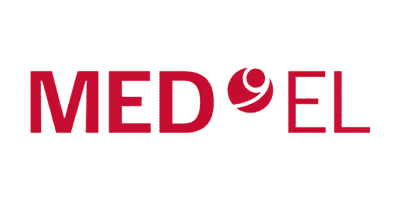
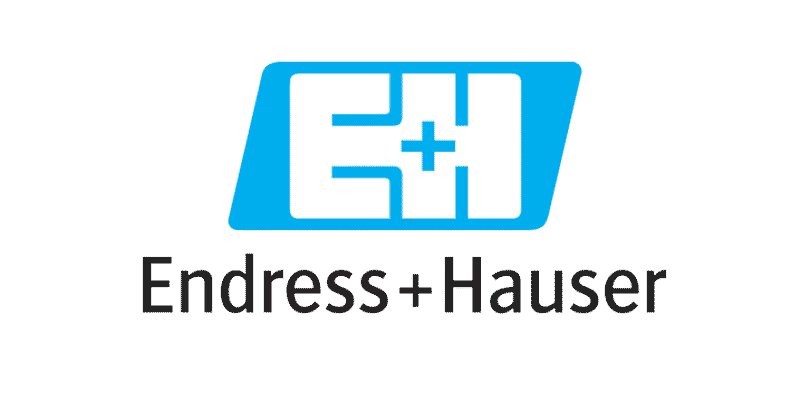
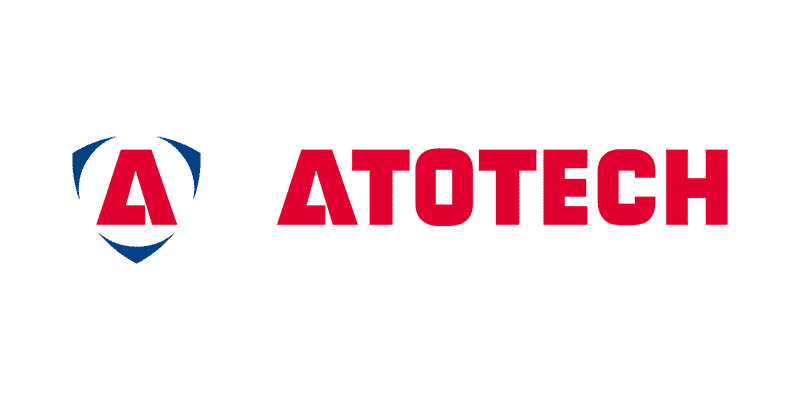
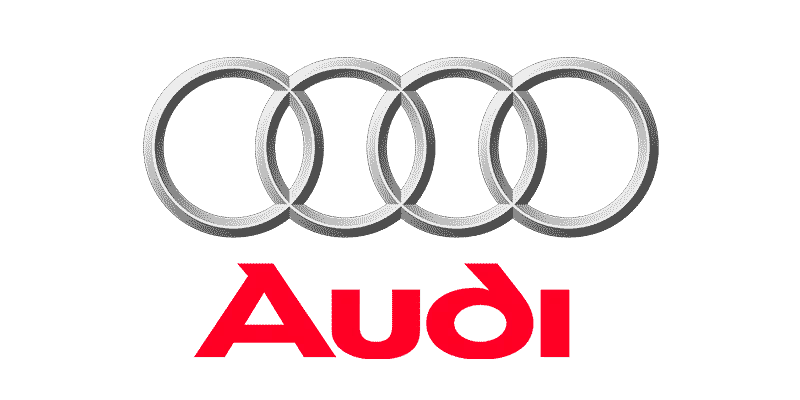
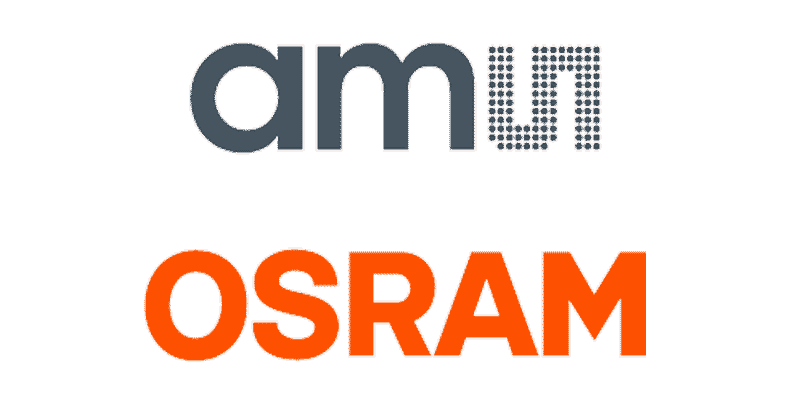
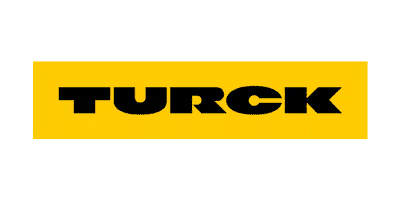
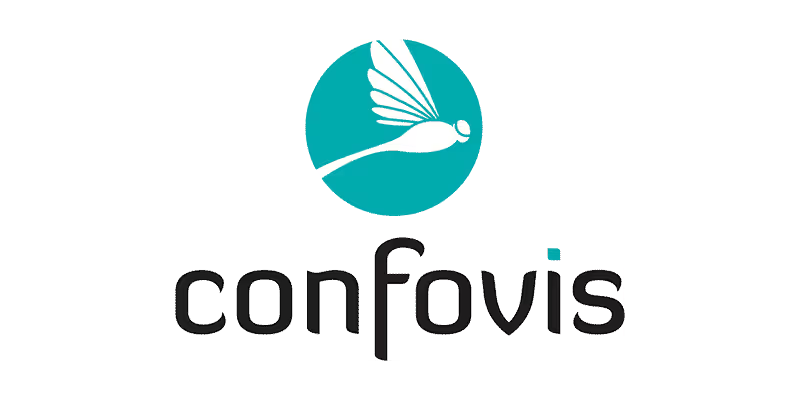
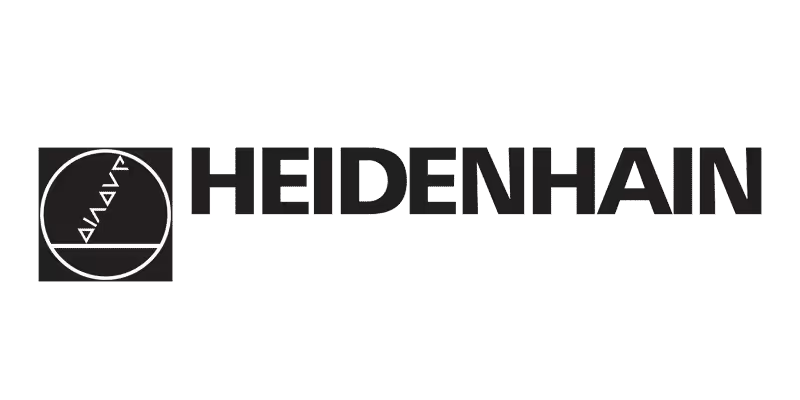
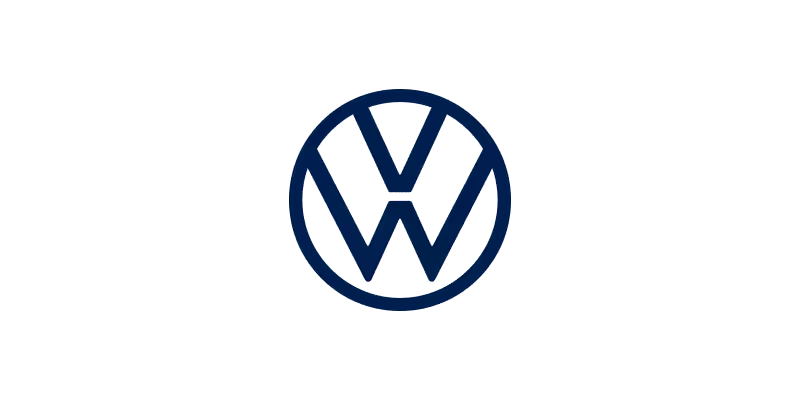
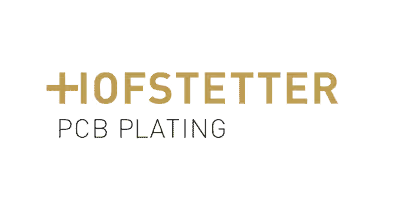
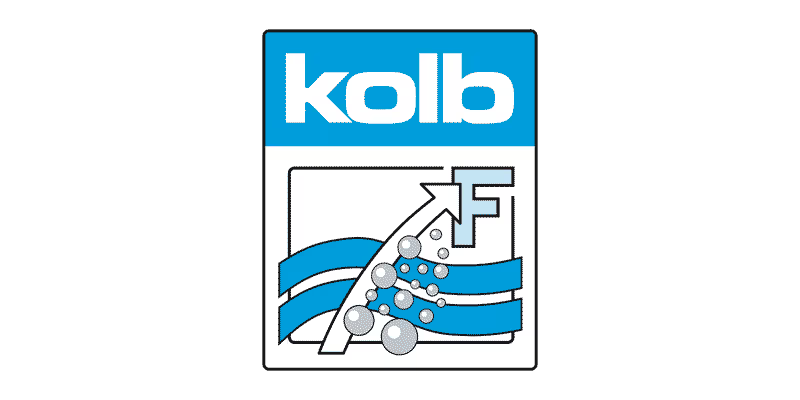
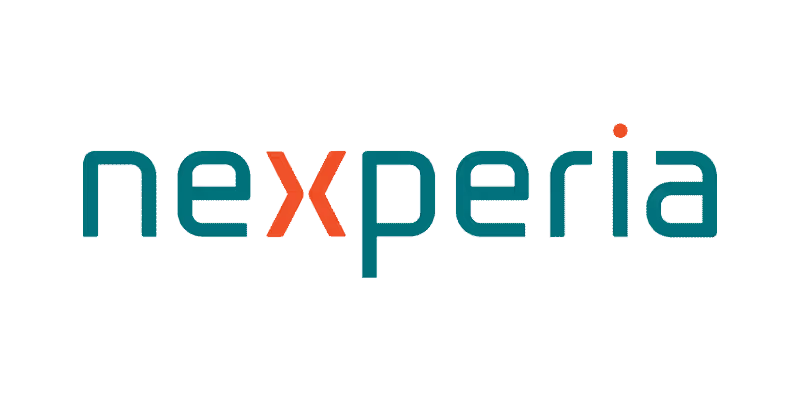
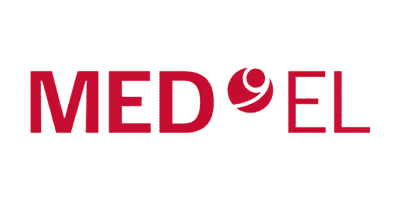
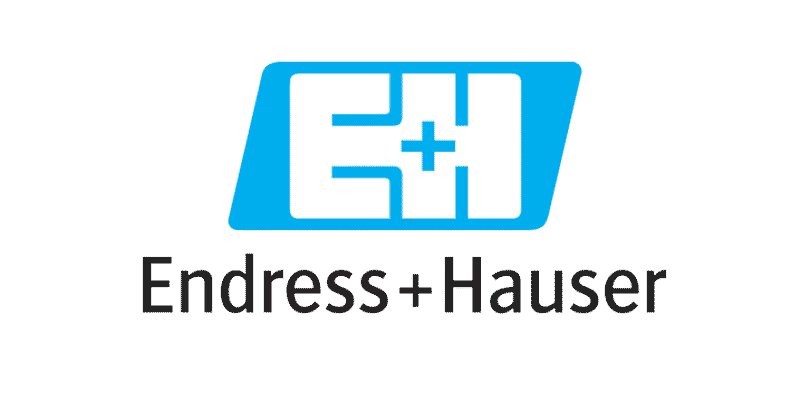
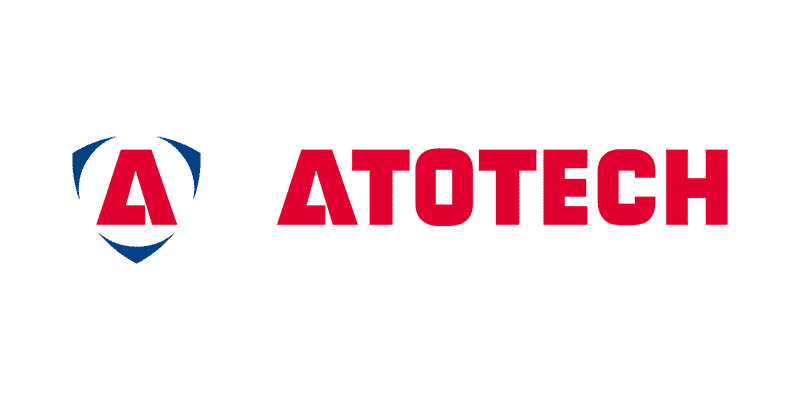
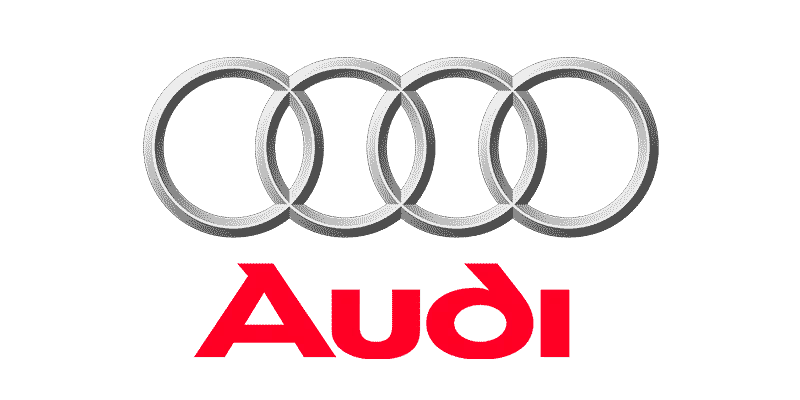
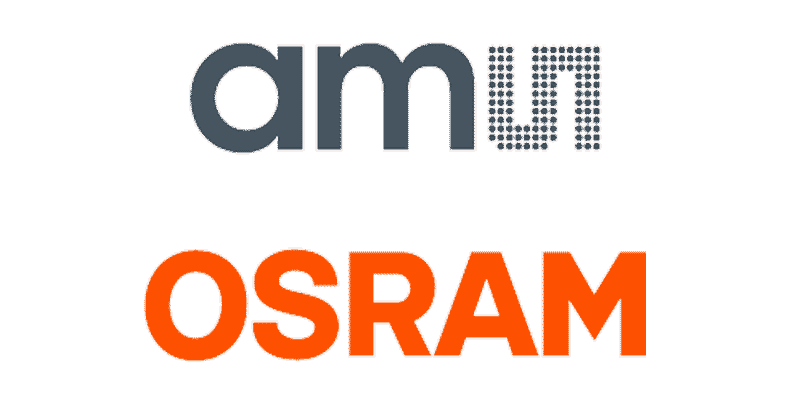
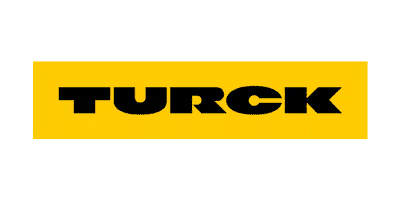
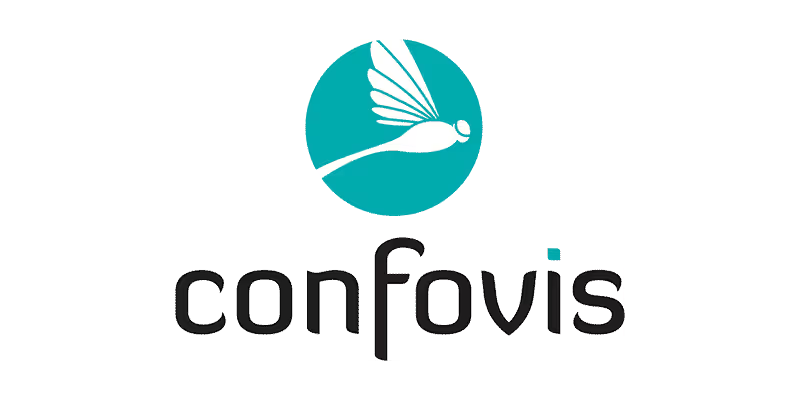
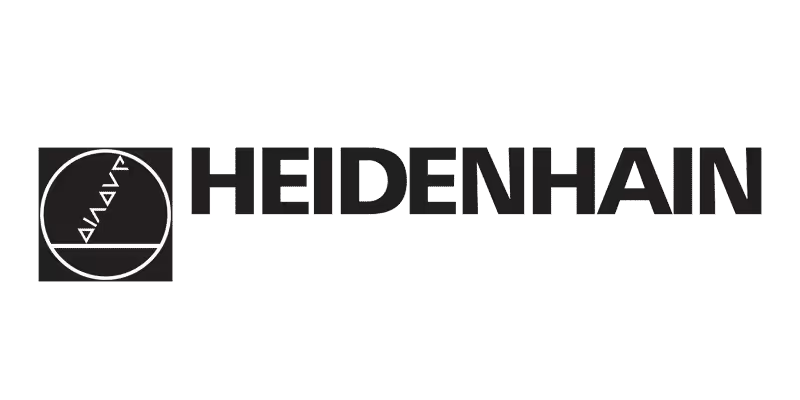
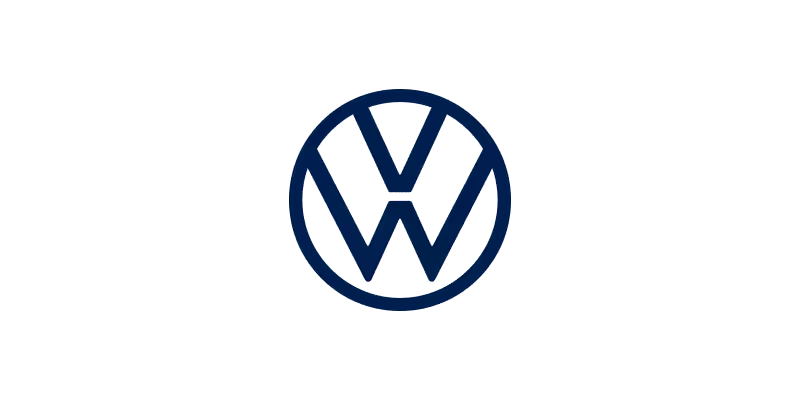
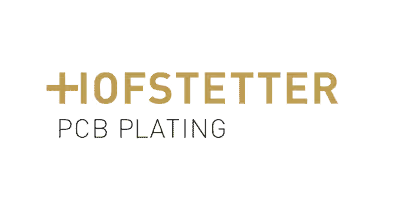
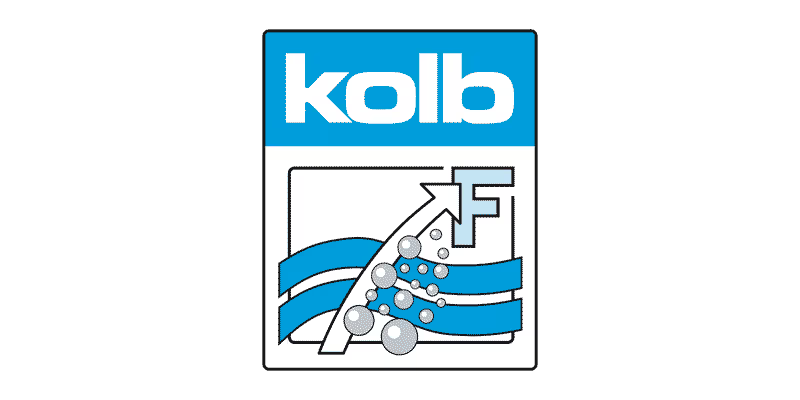
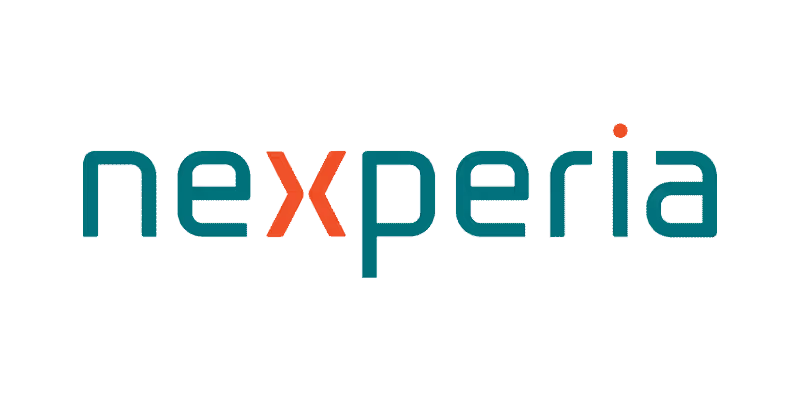
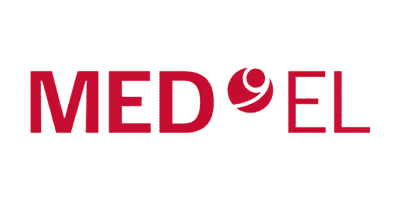
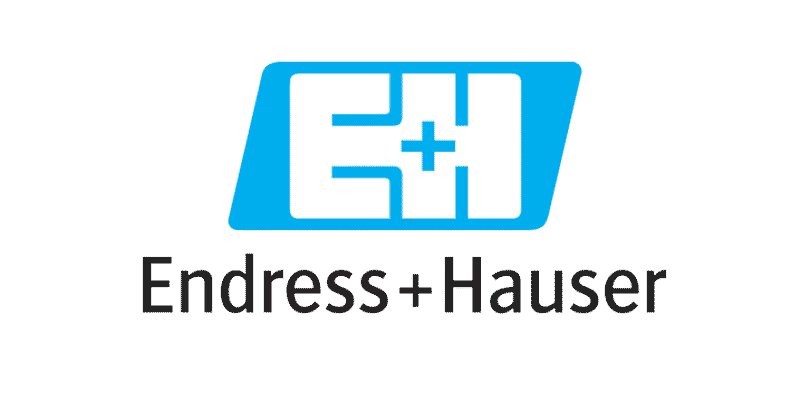
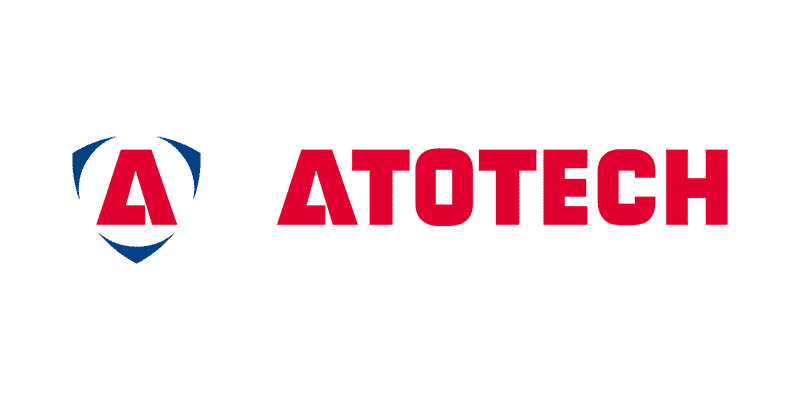
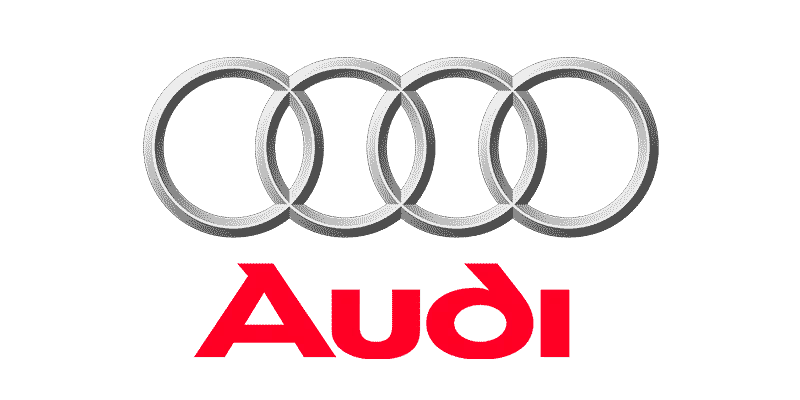
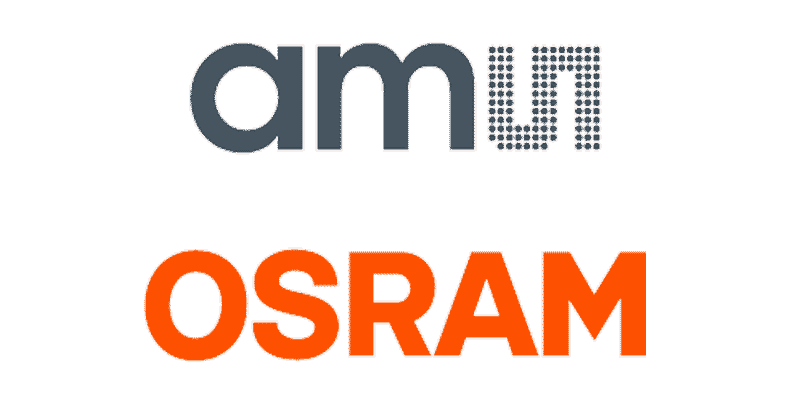
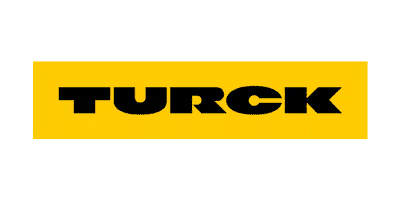
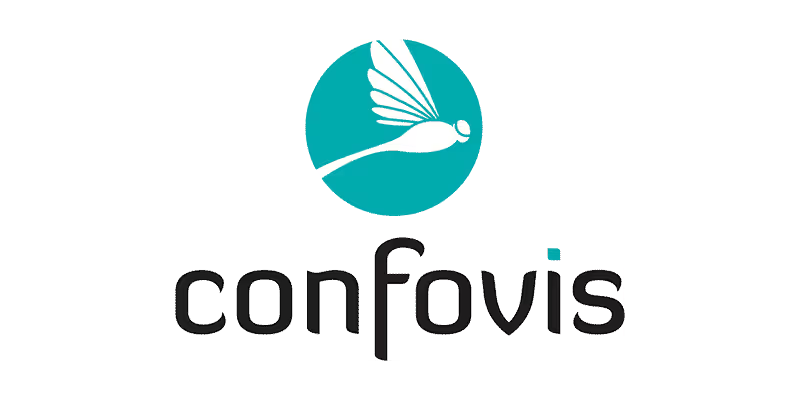
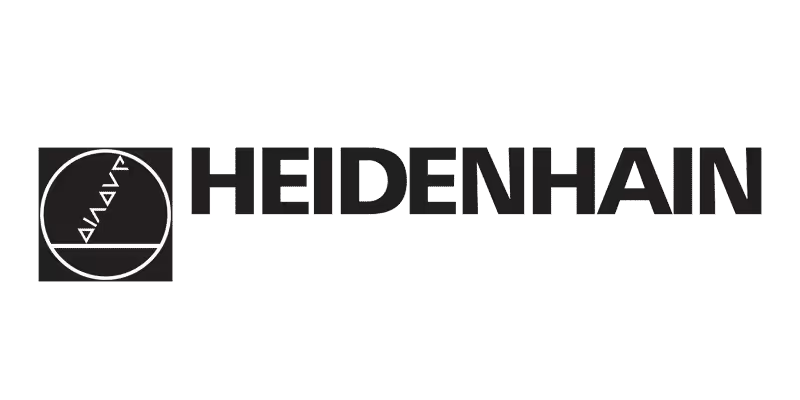
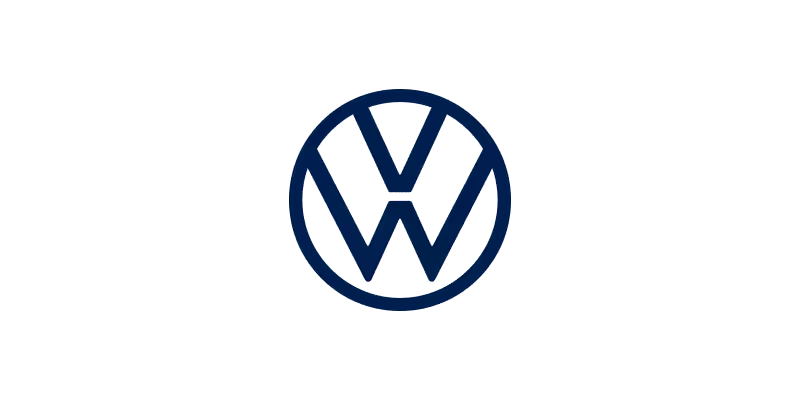
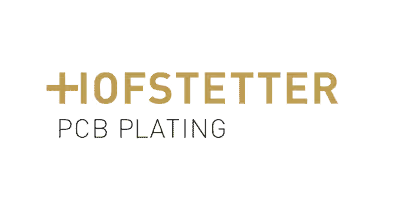
Examples from failure analyses in customer projects
Insights from our customers
Each project represents a unique partnership, and we take pride in the impactful results we achieve together. Below, you’ll find testimonials and case studies from clients who have entrusted us with their goals—whether to drive growth, enhance efficiency, or unlock new potential. Their success stories inspire us to continue delivering exceptional value and building lasting relationships.
Design and process adaptation led to a reduction in process time from 45 min to less than 10 min with a simultaneous reduction in material costs."
— Large German mechanical engineering company
"Development of a comprehensive supplier specification for our printed circuit boards - first version already after 24 h, review and release at our company after only 5 days."
— German automotive supplier
"Inquiry, callback and problem solving within one afternoon. All by phone and within only 30 min despite a tricky challenge."
— Medium-sized contract manufacturer
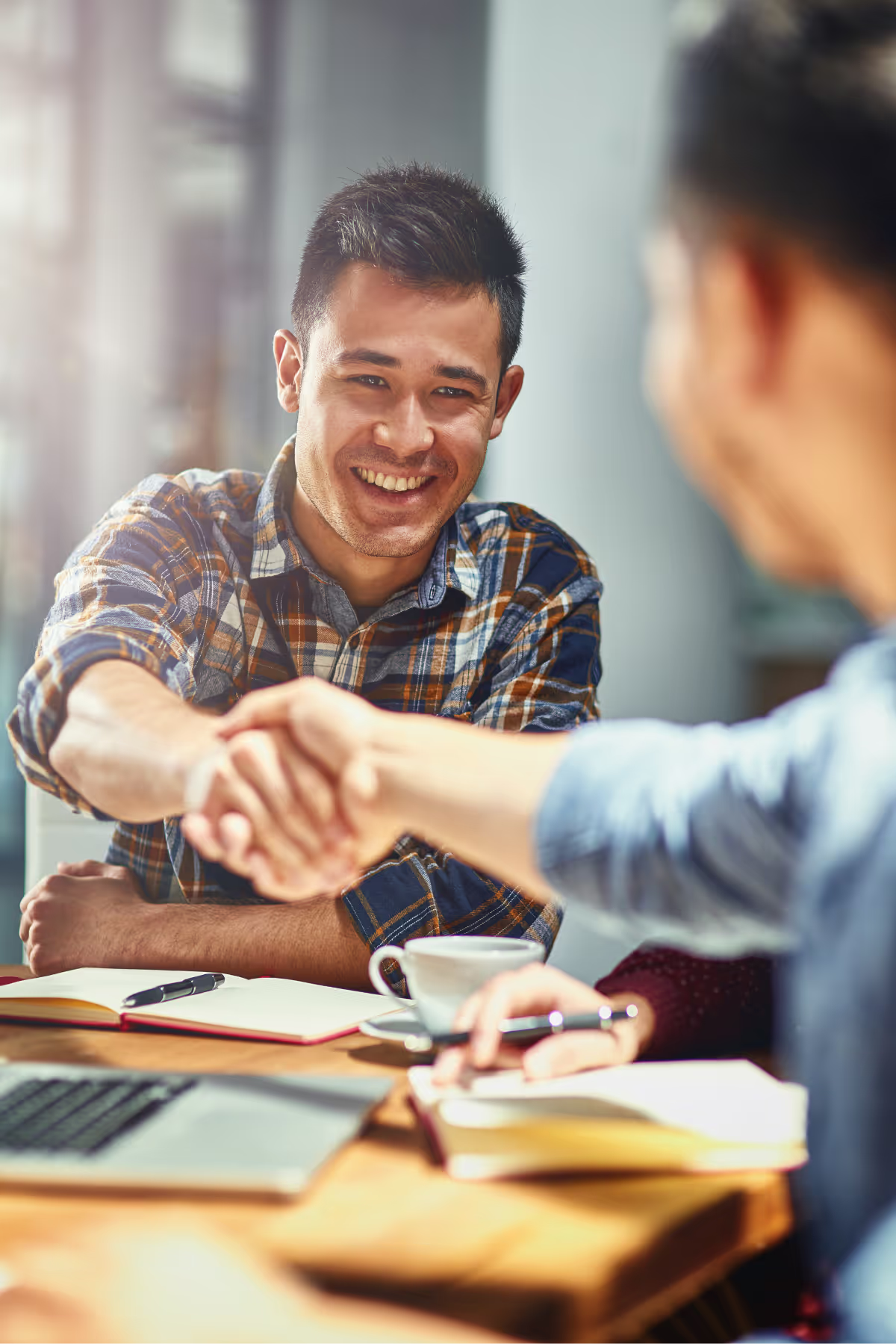
Get in contact for service & support
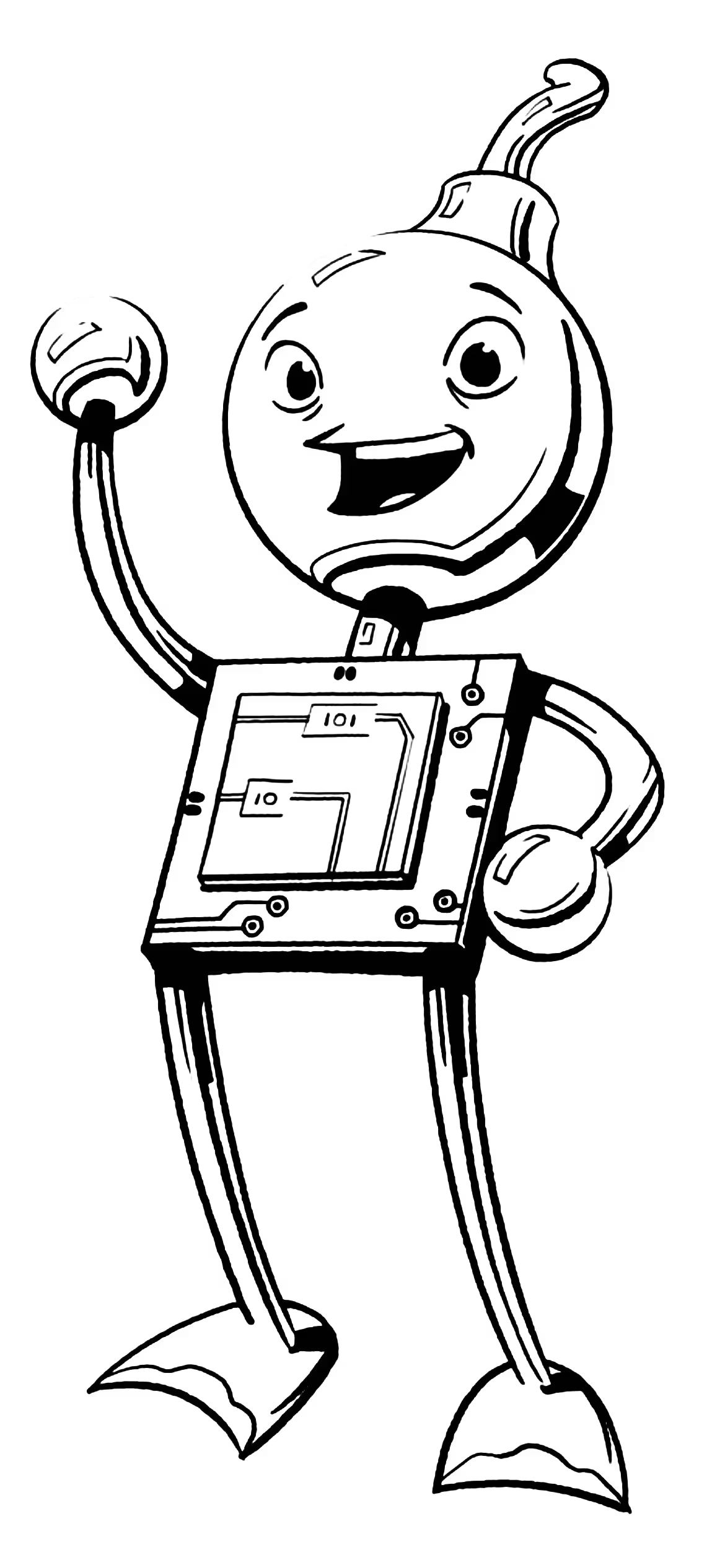
Get in contact for service & support
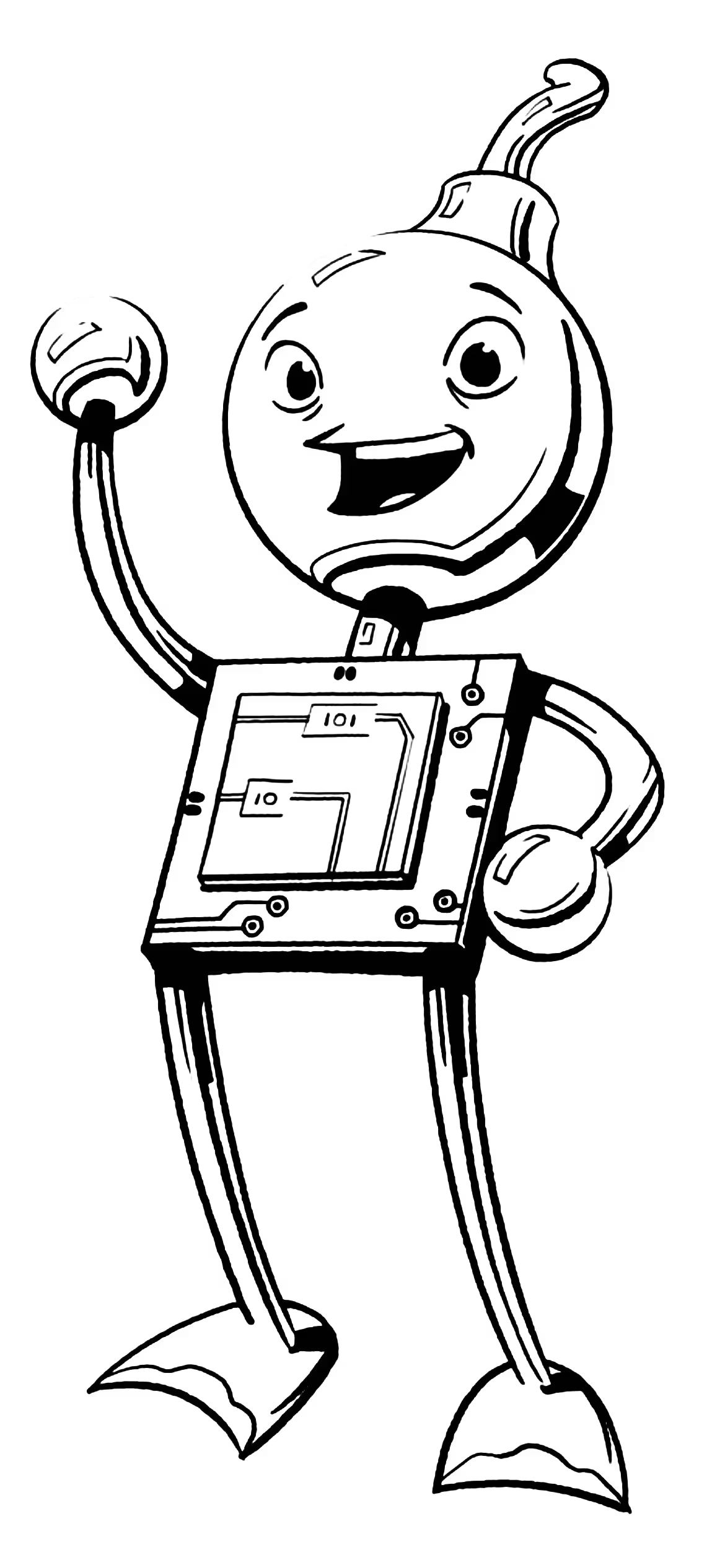
Frequently Asked Questions
Failure analysis involves identifying the causes of defects or performance issues in wire bonding processes or wire bonded devices. This includes examining the bonding process, materials, and environmental factors to determine the root cause of failures, whether they occur during manufacturing or in the field.
Common wire bonding failures include weak or intermittent bonds, wire breakage, bond lift, bond corrosion, heel cracking, and pad damage. These problems can be caused by improper bonding parameters, material incompatibility, contamination, surface defects, or equipment malfunction. Field failures often result from a combination of process shortcomings, material degradation, environmental stress (such as temperature and humidity), mechanical stress, contamination, or improper handling during assembly or shipping. Our analysis is designed to pinpoint the exact cause and provide a path to resolution.
Our failure analysis process begins with a detailed examination of the affected devices and the bonding process. The essential first step is visual inspection of the parts. Scanning electron microscopy (SEM) may follow if necessary. Cross sectioning, FIB (Focused Ion Beam) preparation and material analysis (e.g. TOF-SIMS) are only performed if really necessary and helpful. We review historical data, previous customer complaints, and process parameters to determine the root cause of the failure.
Yes, we often analyze field failures that occur at your customer's site – this is the situation where the pressure is greatest and external support is inevitable. We can help you determine if the problem is due to your wire bonding process, materials used, or external environmental factors, and provide you with a detailed report and recommended solutions.
The timeline for failure analysis depends on the complexity of the failure and the amount of testing required. For most cases, we can provide preliminary findings within a few days, and a detailed report and root cause analysis within 1-2 weeks. Urgent cases may be prioritized. If the situation is still unknown and no other analysis results are available, you can significantly speed up the process by sending us a small selection of parts for visual inspection as soon as possible.
We use a variety of techniques, including visual inspection by optical microscopy, scanning electron microscopy (SEM), energy dispersive X-ray spectroscopy (EDS), bond pull testing, and shear testing. These help us to thoroughly evaluate bond quality and identify potential failure mechanisms.
Absolutely. Once we determine the root cause of a failure, we provide recommendations to improve process control, material selection and equipment settings. We also provide guidance on preventive measures to improve the long-term reliability of your wire bonded devices.
Yes, we provide on-site support when needed. Our team can visit your facility or your customer's site to assess the failure firsthand, perform inspections, and work closely with your team to develop solutions. We also offer remote consulting for less complex cases.
We take confidentiality and privacy very seriously. All findings, reports and client information are kept secure, and we can sign non-disclosure agreements (NDAs) prior to any analysis to ensure that your intellectual property and sensitive data is protected throughout the analysis process.
We work with you to thoroughly investigate customer complaints by reviewing the failed equipment, analyzing the bonding process, and evaluating potential root causes. Once the root cause is identified, we provide corrective actions and recommendations to resolve the complaint and prevent recurrence. We can serve as a neutral party to facilitate discussions and provide feedback on your customer's requirements and specifications for corrective actions. We help you avoid unnecessary analysis, documentation and discussion.
Costs vary depending on the complexity of the failure, the type of analysis required, and whether on-site visits are necessary. After an initial consultation, we provide a quote for the first step, which is typically less than €5,000. After completing this first step, we will be better prepared to provide a quote for subsequent analyses and steps. In every quote, we ensure transparency and a clear understanding of the services you'll receive.
To get started, contact our team with details about the failure or problem you're facing. We'll discuss the scope of the analysis, your specific concerns, and any relevant data or samples we'll need. From there, we'll outline a plan for conducting the investigation and delivering actionable results. This initial contact is free of charge and often includes some useful tips for immediate implementation and problem solving.
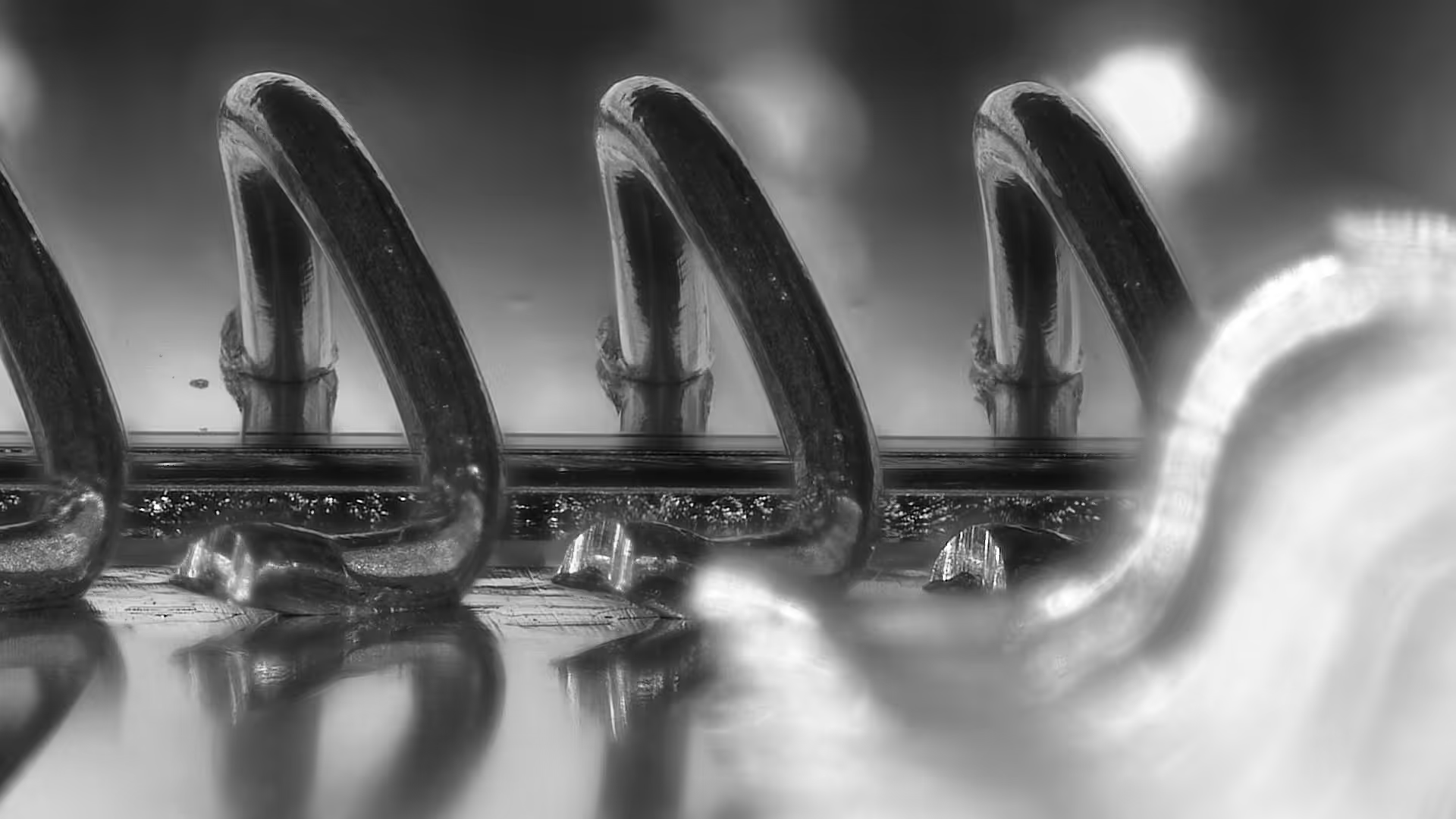
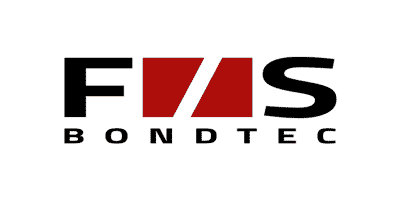
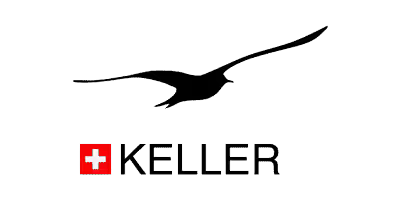
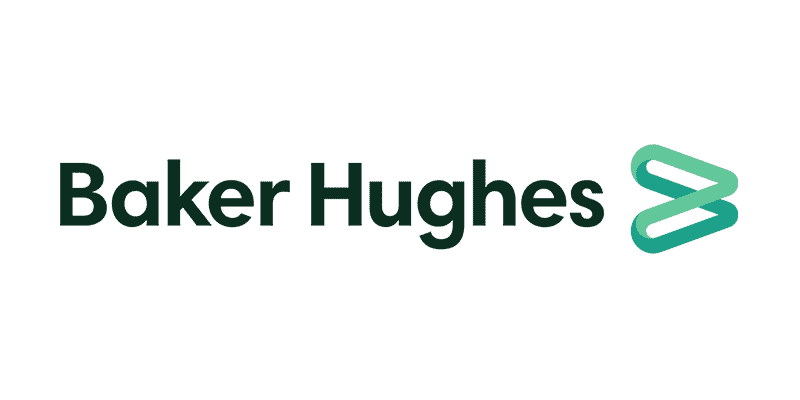
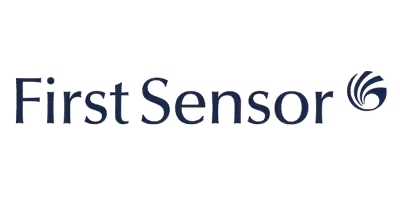
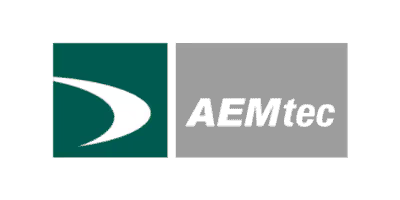

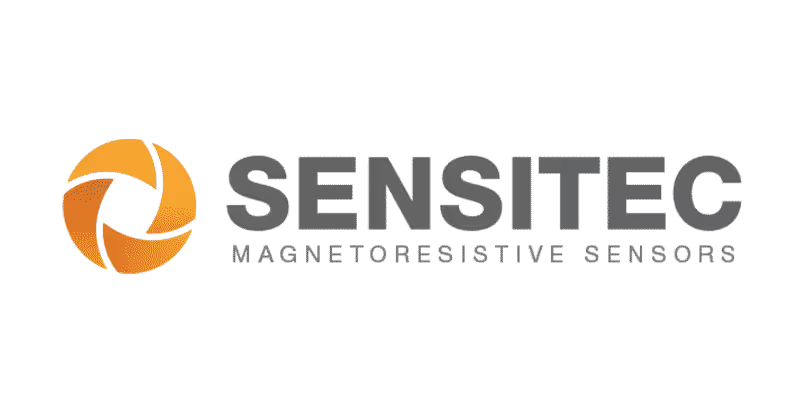
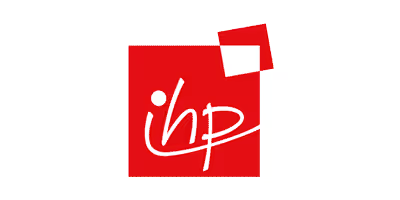
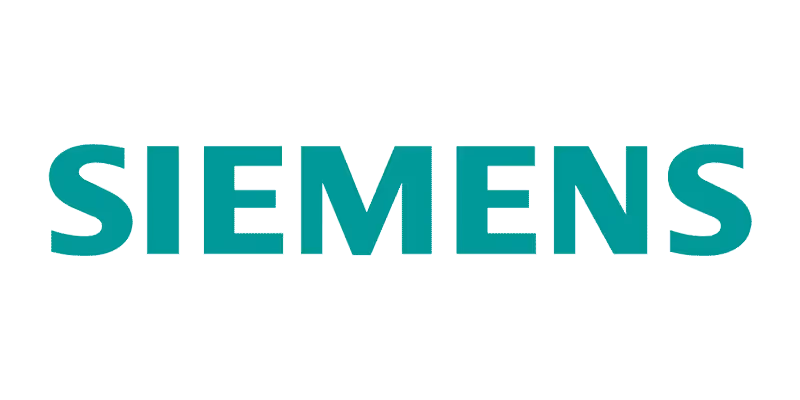
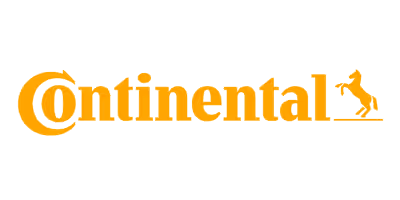
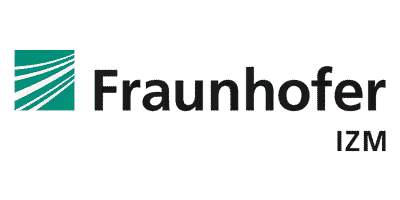
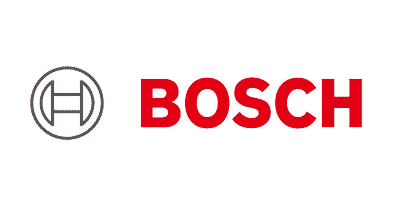
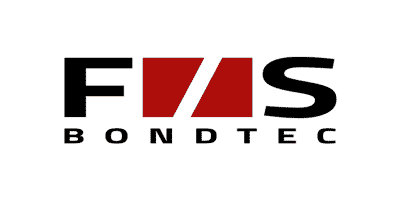
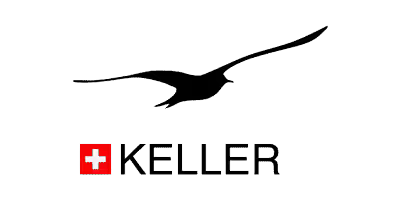
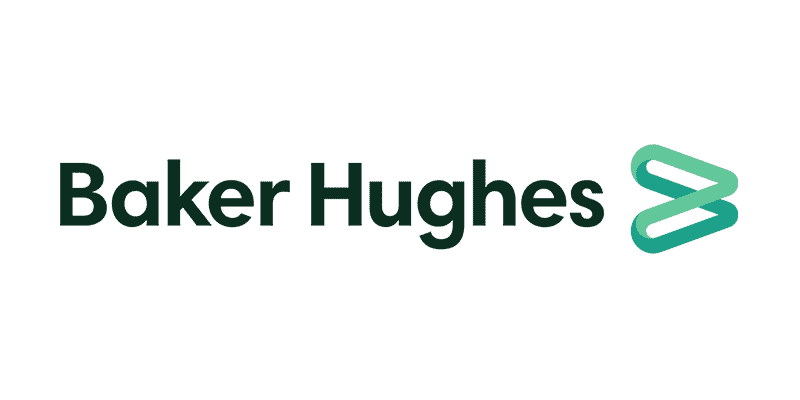
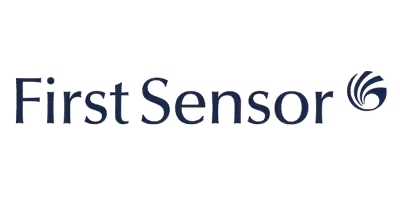
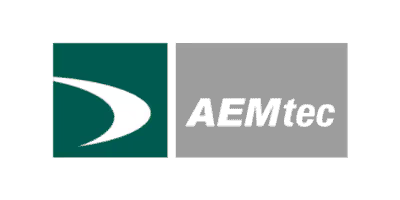

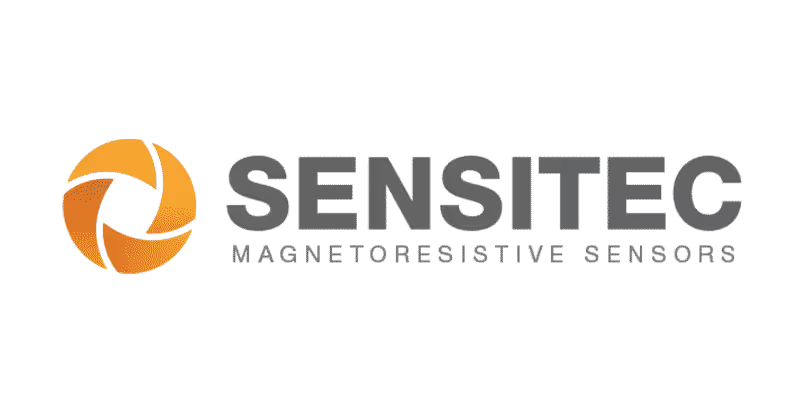
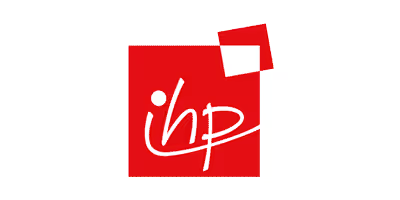
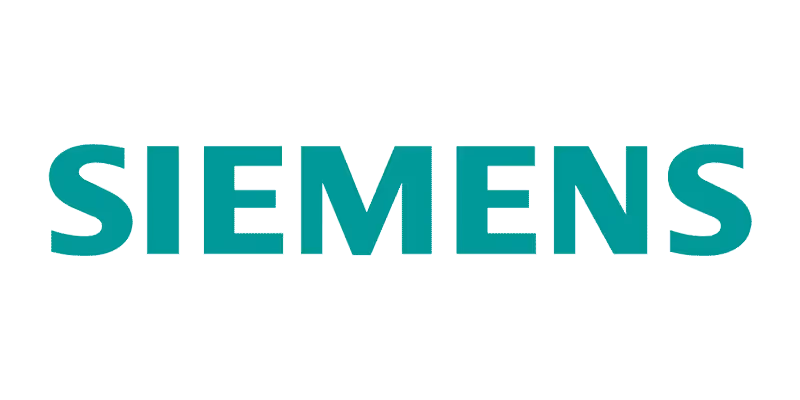
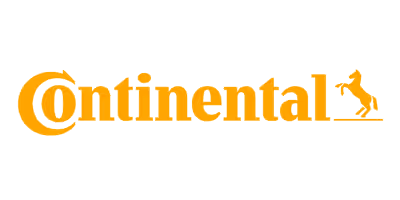
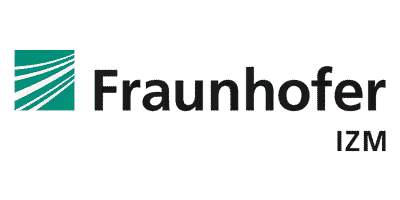
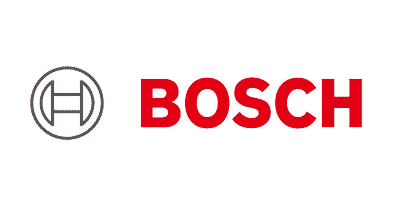
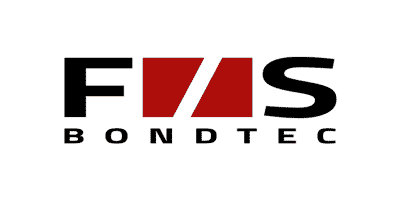
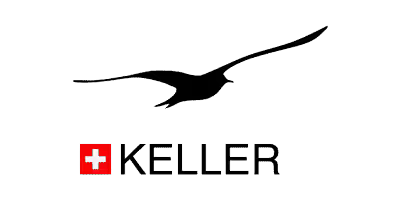
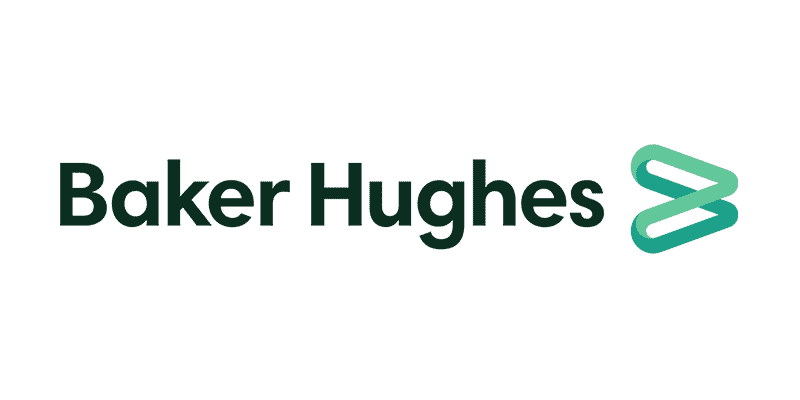
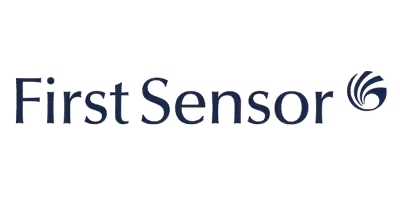
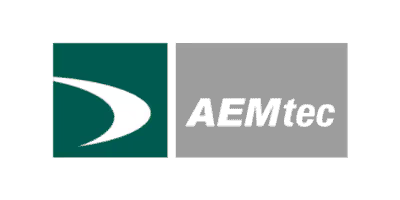

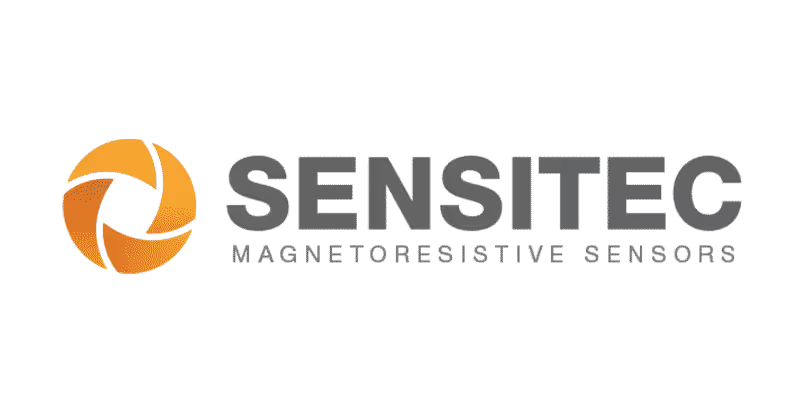
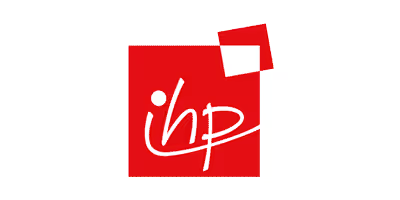
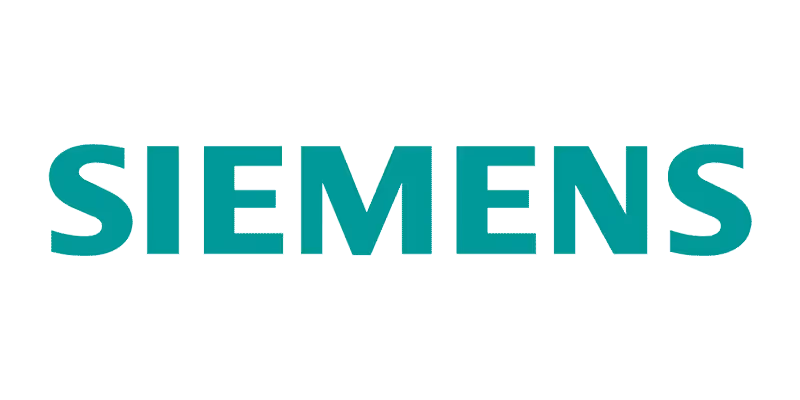
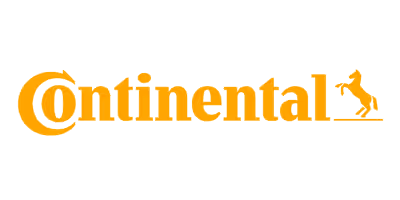
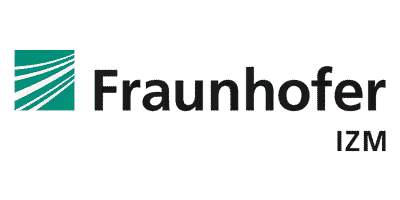
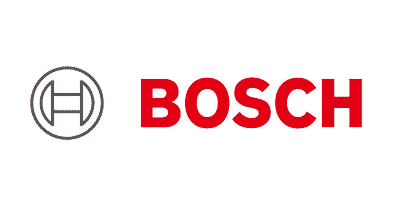