A New Approach to Wire Bond Testing Could Improve High-Power Electronics Reliability
Authors: Bernhard Czerny, Golta Khatibi
US transducer for bond wire excitation
Differential Laser Doppler vibrometer
Silicon with copper metallization
30 µm Cu metallization, 4 µm Al metallization
400 µm Al-Al wedge bonds, 400 µm Cu-Cu wedge bonds
Shear testing
Power cycling tests
Laser Doppler vibrometer measurements
Micro-sectioning techniques for crack growth analysis
1 table with measurement data
8 pictures illustrating testing equipment, fracture surfaces, and test results
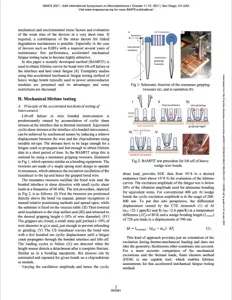
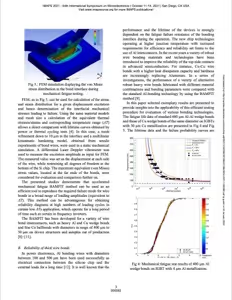
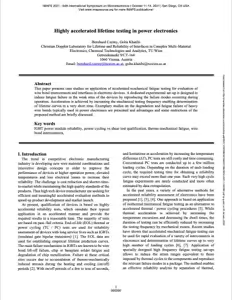
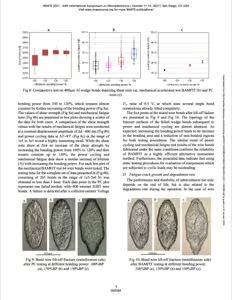
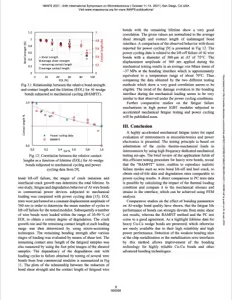
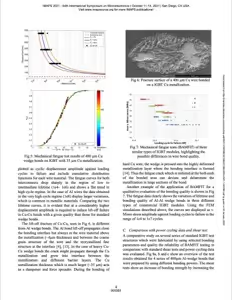
Executive Summary
The objective of this study is to enhance the reliability assessment of wire bonds in power electronics, with a particular emphasis on the Highly Accelerated Lifetime Testing (HALT) methodology. In the context of electronic devices, wire bonding refers to a technique whereby thin wires are used to connect semiconductor components. With the passage of time, these bonds may succumb to failure as a consequence of wear and tear, particularly in the context of extreme temperature fluctuations. The researchers developed a mechanical testing method to simulate the failure that would naturally occur in wire bonds over time, thereby enabling them to predict the longevity of the bonds in real-world conditions.
The method employed accelerates the process by increasing the frequency of mechanical stress applied to the wire bonds. The study primarily investigated the behavior of heavy aluminum (Al) and copper (Cu) wire bonds, which are commonly utilized in high-power electronics, such as insulated gate bipolar transistors (IGBTs). Through this testing, it was determined that while copper wire bonds are more durable than aluminum, they necessitate specific conditions to prevent failure. This research facilitates the enhancement of wire bond durability and reliability in electronic components, thereby optimizing the performance of devices utilized in industries such as automotive and renewable energy.
Get your article summary
The summary will be sent to your email address
Main Focus
The research presented by Czerny and Khatibi introduces a highly accelerated mechanical fatigue testing method, termed BAMFIT (Bond Accelerated Mechanical Fatigue Testing), with the objective of improving the reliability evaluation of wire bond interconnects in power electronics. The objective of the method is to simulate the failure modes of wire bonds through mechanical fatigue testing and to compare the results to those obtained through conventional thermal cycling. The study focuses on heavy wire bonds, particularly aluminum (Al) and copper (Cu) wires, used in insulated gate bipolar transistors (IGBTs), offering a faster and more efficient approach to obtaining lifetime data.
Background and Motivation
In the field of power electronics, wire bonds play a pivotal role in establishing the electrical connection between semiconductor chips and external leads. The reliability of these bonds is of paramount importance, particularly in high-power devices such as IGBTs, where operational stressors include significant thermal and mechanical loads. Conventional qualification techniques, such as power cycling (PC) and thermal cycling (TC) tests, attempt to simulate these stresses but are inherently time-consuming. This is due to the high number of cycles required, which often results in the generation of lifetime curves taking years to produce.
This delay impedes the rapid development and market introduction of advanced semiconductor technologies, which are required to meet exacting reliability standards. To address this issue, BAMFIT introduces a mechanical approach that accelerates fatigue testing by applying cyclic mechanical shear loads at high frequencies, providing an alternative to PC and TC methods. The objective of this research is to validate BAMFIT as a reliable and time-efficient method for evaluating the durability of wire bonds, with a particular focus on Al and Cu wedge bonds.
Methodology
The BAMFIT method employs the use of resonance gripping tweezers to oscillate bond wires in the shear direction at a frequency of 60 kHz. This results in the induction of cyclic shear stresses at the bond interface, which are analogous to those experienced in thermal cycling but at a considerably higher rate. The amplitude of the mechanical excitation is varied in order to simulate different operational stresses, thereby enabling the researchers to evaluate the fatigue life across a wide range of displacement amplitudes.
- BAMFIT Setup: The use of resonance tweezers in conjunction with a US transducer results in the excitation of the bond wire, with sub-micrometer displacements (~200-800 nm for 400 µm Al and Cu wires). This process effectively simulates thermo-mechanical stresses at the wire/substrate interface.
- Finite Element Method (FEM) Simulation: The finite element method (FEM) is utilized to examine the distributions of stress and strain at the bond interface, facilitating a comparison between the effects of mechanical and thermal stressors. The model considers the distribution of von Mises stress at the far ends of the bond, with mesh refinement down to 10 µm.
Furthermore, the study employs comparative analyses between BAMFIT results, power cycling data, and static shear testing to validate the mechanical fatigue method's reliability in replicating real-world conditions.
Key Findings
- Copper Bonds Perform Better Than Aluminum: BAMFIT testing demonstrated that Cu-Cu bonds necessitate considerably elevated cyclic displacement amplitudes to precipitate lift-off failure in comparison to Al-Al bonds. This suggests that Cu bonds may have a superior fatigue life, which is consistent with their increasing use in high-power electronics due to their superior thermal and mechanical properties.
- Similar Trends Between BAMFIT and Power Cycling: The failure modes and fatigue life data obtained from BAMFIT are found to be highly consistent with those observed in power cycling tests. For example, the propagation of fatigue cracks in aluminum bonds during BAMFIT testing was found to occur in a manner similar to that observed in PC tests, thereby reinforcing the validity of the method as a rapid alternative.
- Effect of Bonding Power on Reliability: The study demonstrated that an increase in bonding power enhances the shear strength of wire bonds, with a notable improvement in both BAMFIT fatigue life and power cycling endurance. However, shear tests alone were inadequate for predicting fatigue life under cyclic loads, underscoring the necessity for dynamic testing methods such as BAMFIT.
Implications for Future Research and Industry
By significantly reducing the time required for testing (from years in PC testing to hours using BAMFIT), this approach could facilitate the development and validation of new materials and bonding technologies, such as advanced copper alloys or silver interconnects, in a more expedient manner. The method's capacity to simulate realistic failure modes renders it a valuable tool for evaluating the fatigue performance of wire bonds under complex operational conditions.
For the industry, BAMFIT has the potential to facilitate more expeditious product development cycles, thereby enabling manufacturers to optimize wire bonding processes and materials for enhanced performance and longevity. The methodology is particularly pertinent to sectors such as automotive and renewable energy, where power electronics operate under extreme conditions and require highly reliable interconnects.
Limitations
- Material-Specific Limitations: Although BAMFIT has yielded encouraging outcomes with regard to aluminum and copper bonds, its potential for use with other materials, including advanced alloys and composite wire bonds, remains to be seen and is a subject of further investigation.
- High-Frequency Limitations: Although the 60 kHz excitation frequency used in BAMFIT is an efficient method for accelerated testing, it may not precisely replicate the lower-frequency thermo-mechanical stresses experienced in real-world applications. Further research is required to guarantee the accuracy of the method across a range of frequencies.
- Geometry-Specific Constraints: The study is primarily concerned with the examination of wedge bonds with specific dimensions. The applicability of BAMFIT to other bond geometries (e.g., ball bonds) or different wire diameters may present challenges in scaling the methodology without further refinement.
- Potential for Over-Acceleration: Although mechanical acceleration markedly diminishes the time required for testing, there is a possibility of introducing artifacts that may not perfectly align with the actual operational conditions in the real world. To illustrate, high-frequency excitation may result in disparate failure mechanisms compared to low-frequency thermal cycling.
Get your article summary
The summary will be sent to your email address