Sintering and Copper Wire Bonding: Reducing Failure Rates in High-Temperature Power Modules
Authors: M. Schneider-Ramelow, M. Hutter, H. Oppermann, J.-M. Göhre, S. Schmitz, E. Hoene, K.-D. Lang
Wires: Heavy Aluminum (Al), Copper (Cu), and Cu/Al-Bi metal ribbons
Several diagrams related to thermal cycling and power cycling performance
12 pictures including SEM images, diagrams of failure mechanisms, and test results.
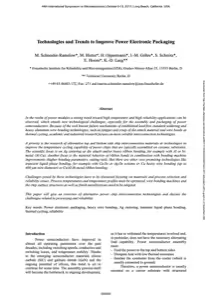
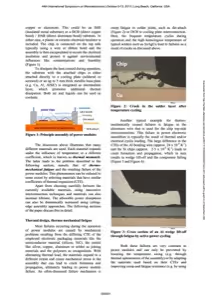
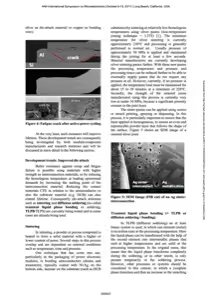
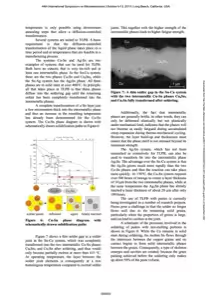
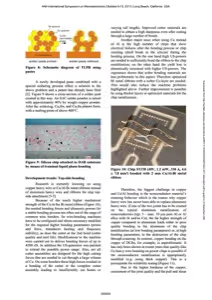
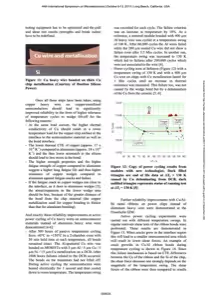
Executive Summary
This paper presents a summary of the advancements in power electronic packaging, with a particular emphasis on the enhancement of reliability and performance under high temperatures. Power electronics are utilized in a multitude of devices to regulate electrical energy, and these systems encounter challenges due to the thermal stresses that are generated during operation. One area of focus is wire bonding, which involves the use of a metal wire to establish a connection between a semiconductor chip and other components.
The researchers investigated alternative materials and bonding methods, including the use of copper (Cu) or silver (Ag) in place of traditional aluminum (Al) wires and the application of sintering (a process involving the fusion of materials under heat and pressure). The objective of these innovations is to mitigate the risk of failures due to thermal cycling, which causes materials to expand and contract, leading to the formation of cracks and eventual breakdowns in power modules.
The findings of the study indicate that copper wire bonds and silver sintering significantly enhance the durability and performance of power modules, particularly under high thermal stresses. The utilization of these materials has the potential to extend the operational lifetime of power electronics, thereby enhancing their reliability for industries such as renewable energy and electric vehicles.
Get your article summary
The summary will be sent to your email address
Main Focus
The research paper is concerned with the enhancement of power electronics packaging, with a particular emphasis on the reliability and performance of such packaging under extreme thermal conditions. The investigation considers alternative interconnection technologies for power semiconductors, including Ag sintering, Cu-heavy wire bonding, and Cu/Al-Bi metal ribbon bonding, as potential solutions to the limitations of traditional Al-heavy wire bonding. The objective of the study is to enhance the fatigue resistance and thermal cycling capabilities of power modules in applications such as renewable energy and electric vehicles.
Background and Motivation
The rapid advancement in power semiconductor materials, such as silicon carbide (SiC) and gallium nitride (GaN), has outpaced developments in packaging technologies, which now represent a significant challenge in achieving higher performance and reliability. Conventional aluminum-heavy wire bonding and solder-based die attach methods have been shown to exhibit a number of well-documented failure modes, including thermo-mechanical fatigue, creep, and crack formation during thermal cycling. As power modules operate at increasingly higher temperatures, there is a pressing need for interconnection methods that can withstand these conditions, thereby extending the operational lifetime and reliability of the modules. The objective of this research is to evaluate and optimize advanced bonding technologies in order to meet the aforementioned demands.
Methodology
The study employed a number of key experimental methods for the purpose of assessing the performance of alternative bonding techniques. Ag sintering was employed for the creation of die-attach materials through a low-temperature joining technique. Silver pastes were applied via screen and stencil printing, and sintering was conducted under a range of pressure and temperature conditions (e.g., 220-230°C with 30 MPa pressure). Experiments were conducted to assess the efficacy of copper wire bonding using copper wires with a diameter of up to 400 µm. The bonding parameters, including force, ultrasonic power, and cutter quality, were optimized to accommodate the mechanical strength of copper. In order to achieve stable bonds, experiments with Cu/Al bi-metal ribbons involved optimizing bonding machines with a particular focus on force and ultrasonic power, particularly at the second bond (wedge). The samples were subjected to accelerated power cycling and thermal cycling tests. Thermal swings of up to 150 K were applied, and the reliability was assessed by measuring shear forces, fatigue crack propagation, and bond lift-off. The samples were then evaluated by scanning electron microscopy (SEM) to ascertain the formation of cracks and the integrity of the bonding interface post-cycling.
Key Findings
- Ag Sintering demonstrated significant improvements in thermal fatigue resistance compared to traditional soldering techniques. The silver sinter joints maintained structural integrity after extensive thermal cycling, with porosity and mechanical strength being key areas of development.
- Cu-Heavy Wire Bonding showed superior reliability compared to aluminum bonding, particularly in power cycling tests. For instance, Cu-heavy wires withstood over 3.5 million power cycles at a temperature swing of 100 K, whereas Al wires failed after 60,000 cycles under the same conditions.
- Cu/Al-Bi Metal Ribbons showed remarkable resistance to thermal cycling degradation. At 120 K thermal swings, the degradation rate of Cu/Al ribbon bonds was four times lower than traditional Al wire bonds.
- TLPB (Transient Liquid Phase Bonding), particularly using Cu-Sn and Ag-Sn systems, further enhanced fatigue strength, transforming Sn into high-strength intermetallic phases, which remained stable above 400°C.
Implications for Future Research and Industry
- For research: The data indicates a need for further investigation into the optimization of Ag sintering pastes, with a particular focus on reducing processing temperatures and pressures. The accelerated expansion of intermetallic phases in TLPB systems, particularly those involving Ag-Sn, necessitates a more comprehensive investigation to enhance the efficiency and reduce the costs of bonding processes.
- For industry: The transition from Al to Cu wire bonding presents an immediate opportunity for power electronics manufacturers to enhance their product offerings. The enhanced thermal conductivity and fatigue resistance of Cu bonds may enhance the reliability of power modules in electric vehicles, wind turbines, and other high-stress applications. Moreover, the advent of pressure-less sintering methodologies has the potential to reduce production costs and facilitate the implementation of sintering in large-scale manufacturing.
Limitations
- Material Compatibility: The use of copper bonding on aluminum metallization continues to present a considerable risk to reliability, particularly due to the high hardness of copper, which can result in the cracking of chips during the bonding process. Further investigation is required to ascertain the efficacy of potential solutions, such as the use of thick Cu metallizations or alternative chip coatings, in reducing the stress on the semiconductor.
- Porosity in Sintering: The issue of porosity in Ag sinter joints remains a significant concern, particularly in the context of high-pressure processing. In order to achieve mechanical strengths greater than 10 MPa, it is necessary to attain lower porosity levels, which represents a current shortcoming of pressure-less sintering techniques.
- Intermetallic Phase Brittleness: The brittleness of intermetallic phases formed during TLPB may result in the emergence of failure mechanisms under conditions of extreme mechanical loading. It is of paramount importance to ensure that these phases are not subjected to excessive stress in order to guarantee long-term reliability.
- Equipment Modifications: The mechanical forces and ultrasonic powers required for Cu bonding are greater than those needed for conventional Al bonding. The current wire bonding machines are not optimized for this process. This results in increased wear on the tools and inconsistent bond quality, particularly at the second bond (wedge). It is imperative that ongoing adjustments be made to the materials used for cutting tools and to the configurations of the machines themselves in order to address these challenges.
Get your article summary
The summary will be sent to your email address