Investigating the Inaccuracies in Wire Bonding Pull Testing and Introducing a New Analytical Model for Improved Quality Control
Authors: S. Schmitz, J. Kripfgans, M. Schneider-Ramelow, Wolfgang H. Müller, K.-D. Lang
ANSYS® 15.0 for FEM simulation
Wire: 300 µm Al-H11 aluminum wire
FEM simulation
Several diagrams illustrating loop geometries and simulation comparisons
Several figures showing loops after pull testing
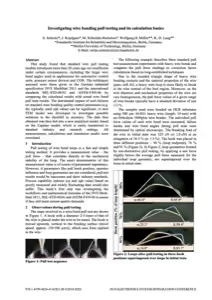
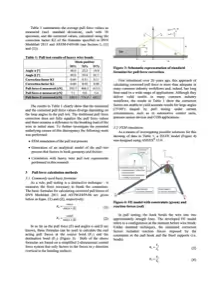
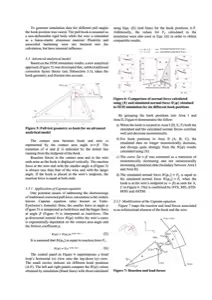
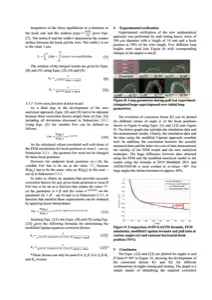
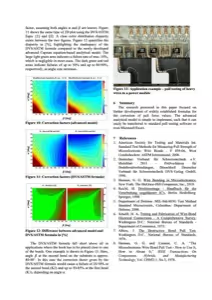
Executive Summary
This study examines the process of wire bonding pull testing, which represents a pivotal quality control step in microelectronics, particularly in fields such as automotive and sensor manufacturing. The process of wire bonding entails the formation of connections between small wires and electronic components. It is of paramount importance to ensure that these bonds are robust in order to guarantee the reliability of the final product. The study demonstrates that conventional pull testing methodologies, as delineated in standards such as ASTM-F459-06 and MIL-STD-883G, are not always reliable, particularly for contemporary applications with substantial wire bond angles.
To address these discrepancies, the researchers developed new simulation models. By employing a method called Finite Element Modeling (FEM) and incorporating a new equation based on the Capstan model, the team achieved more precise pull force calculations. These new approaches could significantly improve the accuracy of pull testing, thereby enhancing the reliability of the process in industries where safety and durability are paramount.
Get your article summary
The summary will be sent to your email address
Main Focus
The paper by Schmitz et al. examines the limitations of conventional wire bonding pull testing techniques, with a particular focus on scenarios involving significant bond angles. These methods are standardized in protocols such as ASTM-F459-06 and MIL-STD-883G and are widely used in the microelectronics industry to ensure bond integrity. Nevertheless, the suitability of these methods for modern applications, such as those found in automotive control units and pressure sensor devices, has been called into question. The research introduces novel finite element modeling (FEM) techniques and an advanced analytical model based on the Capstan equation to enhance the precision of pull testing, particularly for wire bonds with high angles.
Background and Motivation
Wire bonding is a critical process in microelectronics assembly, providing electrical and mechanical connections between chips and substrates. Pull testing is the predominant method for evaluating bond strength, measuring the force required to break a wire. However, traditional methods, such as those described in DVS Merkblatt 2811 and ASTM-F459-06, were developed over two decades ago and are based on simplified models that assume constant geometric conditions. With the increasing complexity of wire bond applications, especially in automotive and sensor technologies where bond angles often exceed 40°, these methods fail to account for non-linear mechanical effects, resulting in inaccurate force measurements. This inaccuracy can affect critical quality control metrics, such as the process capability index (CPK), affecting the reliability and safety of the final product. The study was motivated by the need for a more accurate pull test method that addresses these modern challenges.
Methodology
The researchers conducted a series of pull tests on 300 µm diameter Al-H11 aluminum wires bonded to Direct Copper Bonded (DCB) substrates. Using an Orthodyne 3600plus wire bonder, 30 samples per test were examined with the hook positioned at three different locations: 50%, 76% and 91% of the wire length. The angles formed by the bond loops were measured by optical microscopy.
A Finite Element Method (FEM) model was developed in ANSYS® 15.0 to simulate the pull test.
The model was designed to account for reaction forces at the hook and bond interfaces, unlike traditional simplified two-dimensional models. This allowed the researchers to simulate different wire geometries and hook positions to better understand how forces are distributed across the wire during the test. The study also introduced an analytical model based on the Capstan equation, which accounts for frictional forces and the specific geometry of the pull hook.
To validate the model, the FEM results were compared with actual pull test measurements and traditional correction factors from the ASTM and DVS standards.
Key Findings
- Pull Force Measurements: The study found that traditional correction factors significantly overestimate the pull forces required to break wires, particularly at larger bond angles (above 40°). For example, when the hook was placed at 91% of the wire length (corresponding to a loop angle of 14°), the measured pull force was 413.5 cN, but after applying the traditional correction factor, the adjusted force was 405.2 cN—still far from the breaking load of 325 cN. These inaccuracies become more pronounced as angles increase.
- FEM Simulation Results: The FEM simulation produced more accurate results that closely matched the experimental data, demonstrating that the mechanical behavior of the wire, including the interaction with the pull hook, is more complex than the existing standards account for. The FEM model showed that for larger angles, the discrepancy between the measured and corrected pull forces using traditional methods increased by up to 60%.
- Advanced Analytical Model: The newly proposed Capstan-based model offered a significant improvement over the traditional methods. This model accounted for hook geometry and friction, providing correction factors that aligned more closely with the experimental and FEM data, particularly for bond angles greater than 40°. The study found that the modified Capstan equation could reduce the failure rates in pull testing by 60% in some cases, making it a much more reliable method for quality control.
Implications for Future Research and Industry
The results of this study have significant implications for industries that rely on wire bonding for critical electronic components, such as automotive and aerospace, where reliability is paramount. By adopting the modified capstan-based model, manufacturers can achieve more accurate pull force measurements, leading to better quality control and potentially higher product reliability.
Future research could explore the application of this advanced model in different bonding scenarios, such as different wire materials or more complex bond geometries, and investigate the role of environmental factors such as temperature and humidity. In addition, incorporating this model into existing software systems used in quality control processes could lead to industry-wide improvements in the accuracy of bond testing.
Limitations
While the study successfully demonstrates the inadequacies of traditional pull testing methods and offers a more precise alternative, it also has certain limitations. The FEM model used in this research assumes linear-elastic behavior for the aluminum wire and does not account for plastic deformation or hardening effects, which may play a role in actual bonding scenarios.
Additionally, the study focuses exclusively on aluminum wires and DCB substrates, so the findings may not be directly applicable to other wire materials, bonding methods, or substrate types. Future studies should incorporate a broader range of materials and bonding conditions to fully validate the proposed model.
Get your article summary
The summary will be sent to your email address