Improving wire bond interface analysis using US vibration
A retrospective on validating the BAMFIT method: A faster, more accurate alternative to shear testing for thick wire bond quality assessment.
.avif)
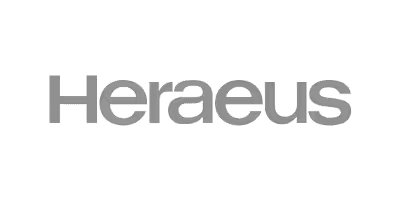
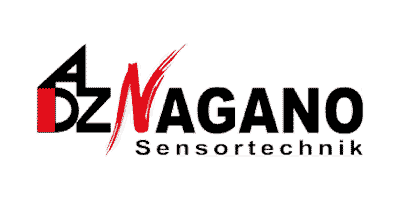
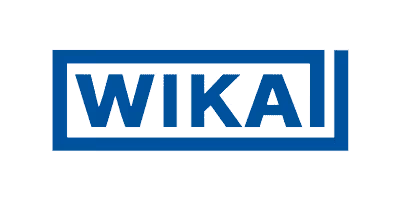
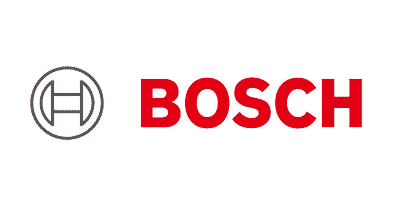
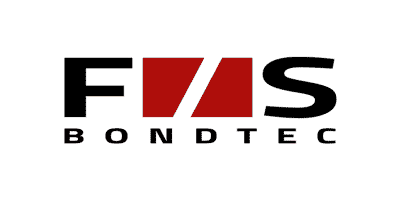
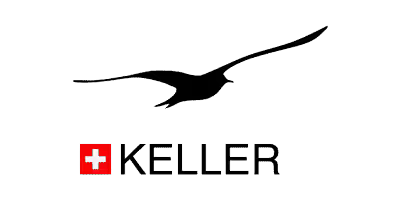
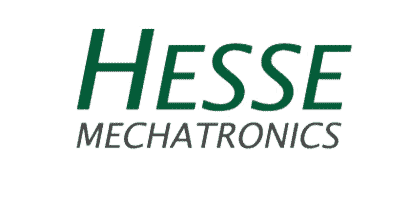
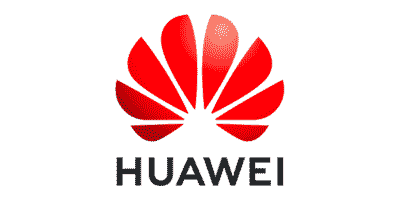
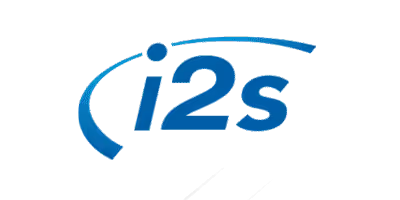
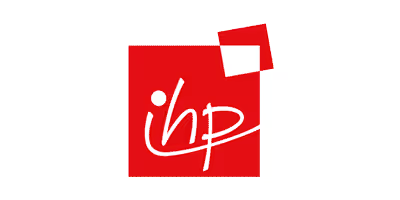
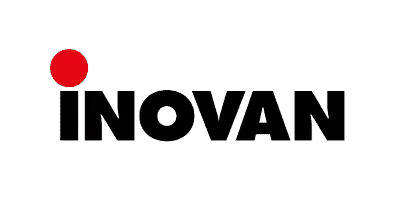
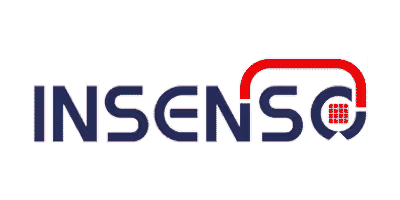
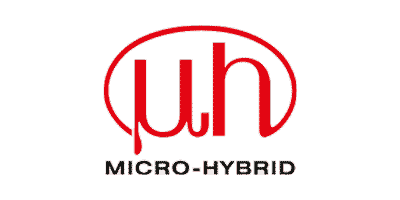
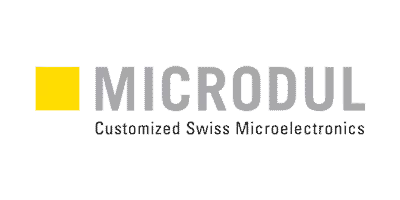
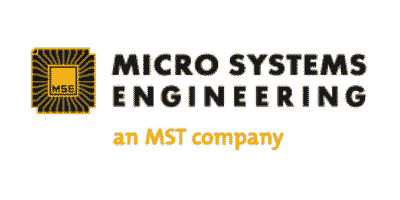
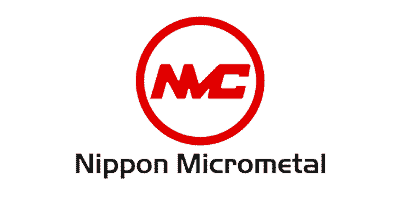
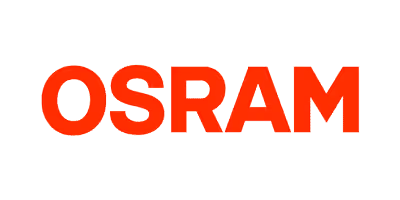
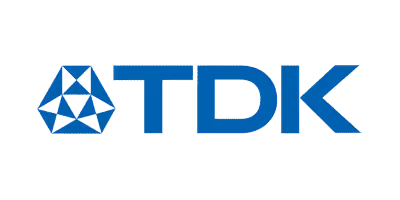
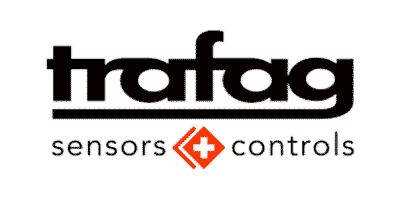
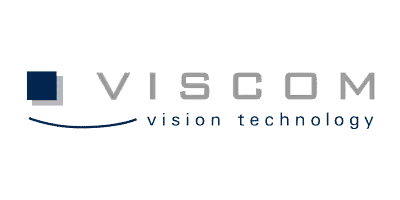
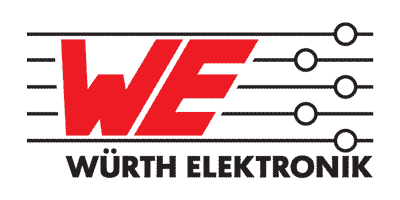
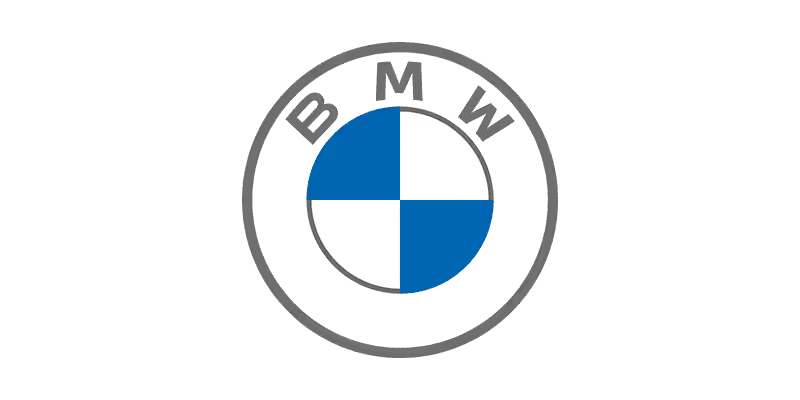
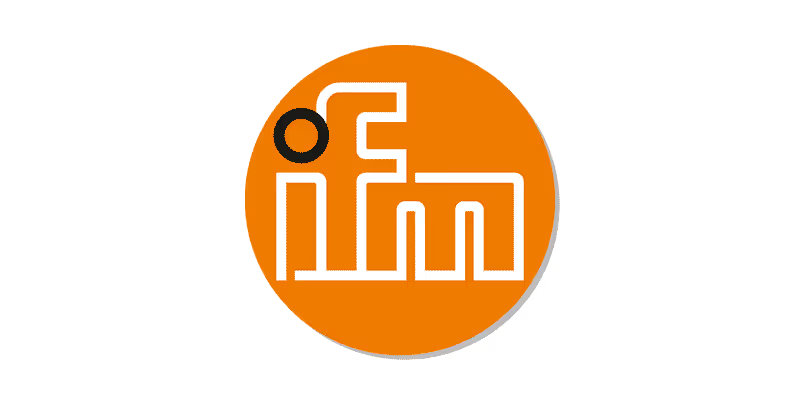
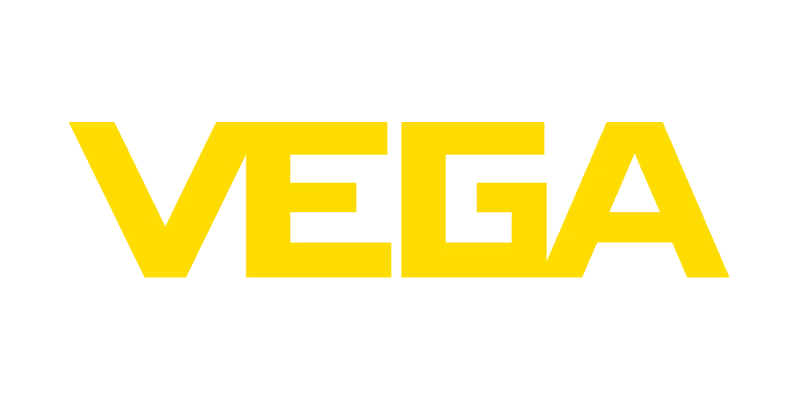
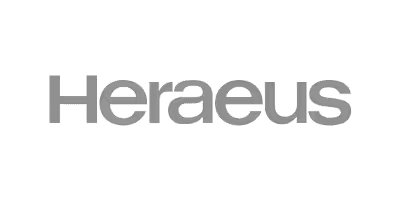
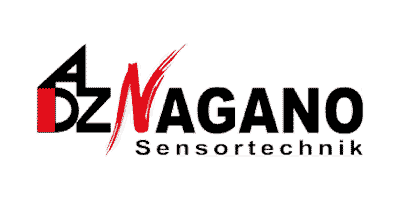
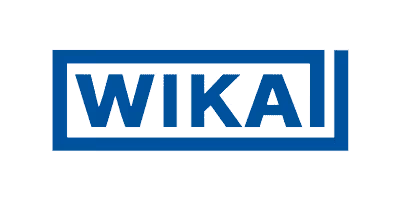
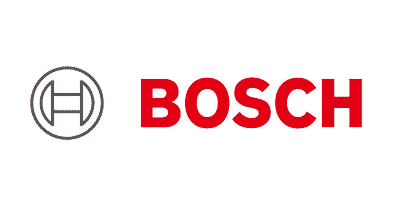
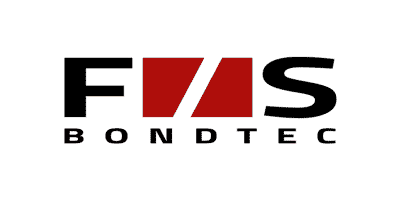
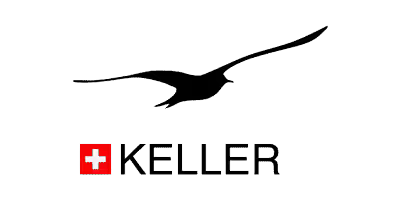
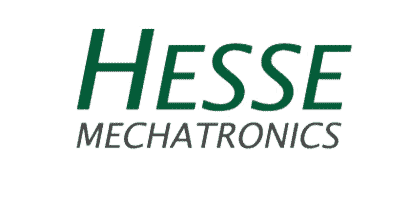
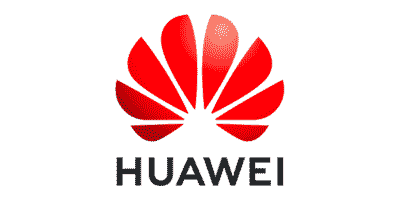
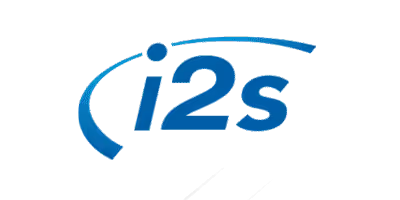
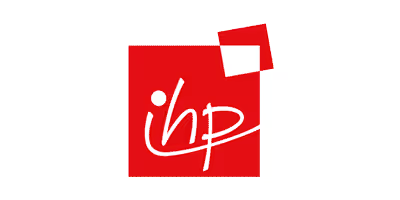
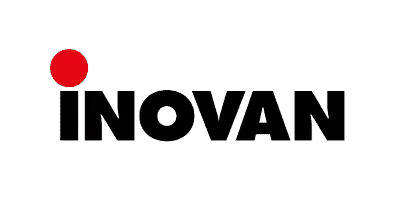
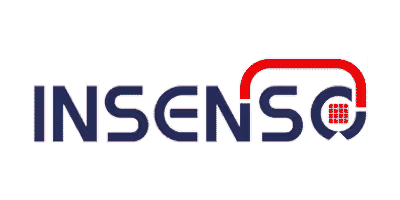
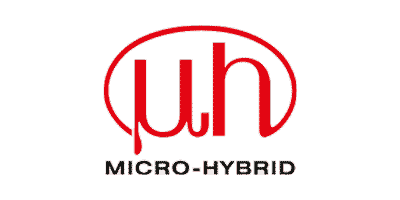
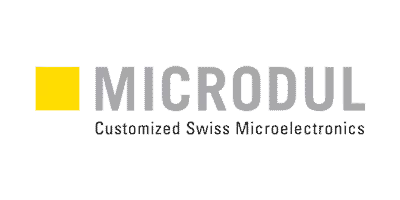
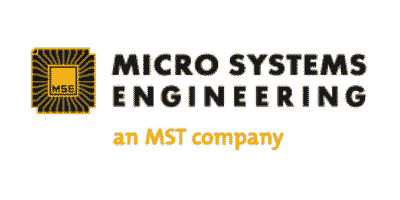
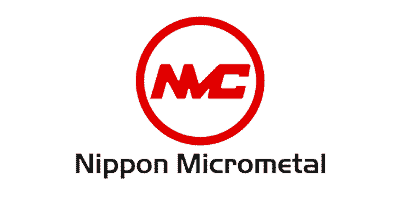
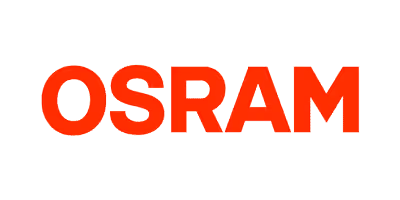
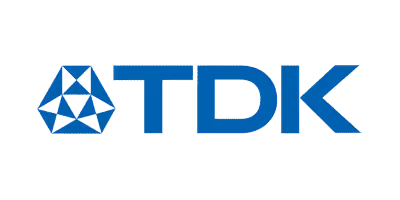
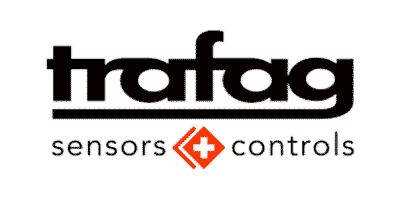
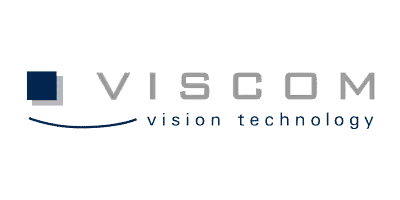
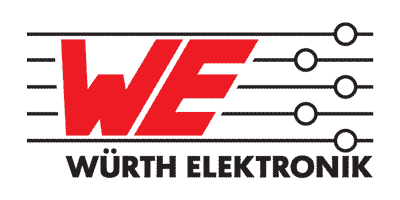
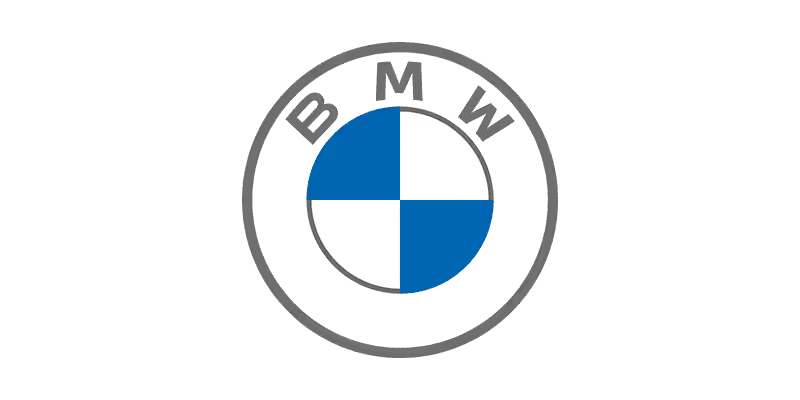
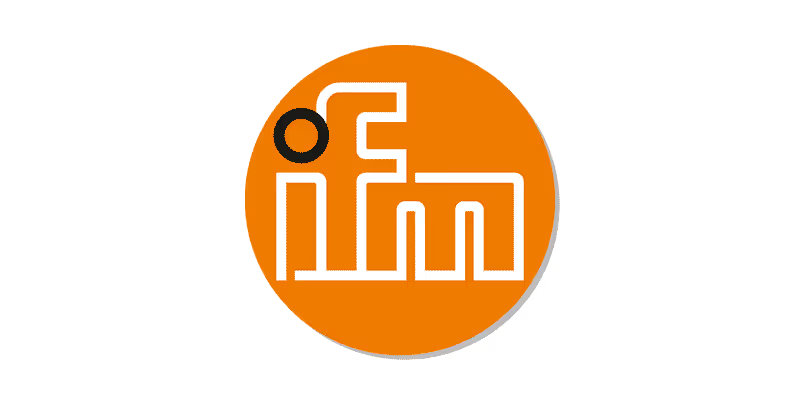
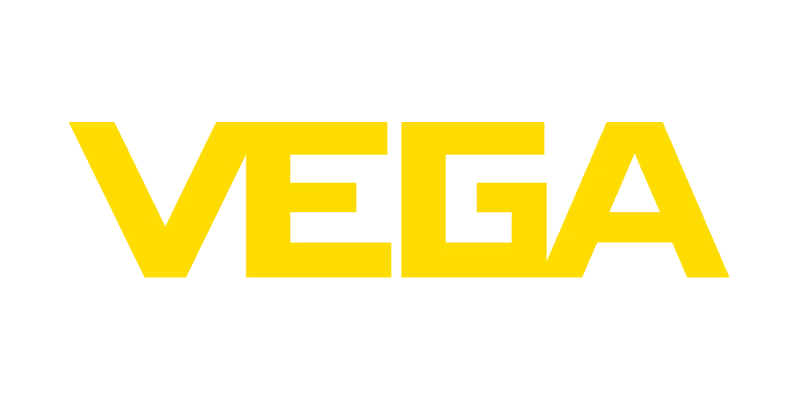
Executive summary
The SpeedCycle project was designed to validate the BAMFIT (Bondtec Accelerated Mechanical Fatigue Interconnect Testing) method as a transformative alternative to traditional shear testing for heavy wire bonds. This initiative attempted to overcome limitations in accuracy and speed while exploring new possibilities for bond quality assessment. Through collaborative efforts and advanced research, the project achieved significant progress, paving the way for improved testing methods.
Key Findings and Achievements:
Validation of BAMFIT as a quality testing alternative: The BAMFIT method demonstrated its ability to provide more comprehensive bond quality data than shear testing, particularly in its ability to identify unbonded regions and variations in material interfaces. Unlike shear tests, which often resulted in smearing and obscured fracture patterns, BAMFIT provided clear, analyzable results, improving diagnostic accuracy.
Crack propagation analysis and interface insights: By analyzing fracture patterns and crack propagation during BAMFIT tests, the project gained critical insight into the behavior of bonded interfaces. Unlike traditional methods, BAMFIT enabled the identification of crack initiation points and crack growth, providing new opportunities for process optimization.
Compatibility with different materials and applications: BAMFIT was particularly effective with aluminum wire bonding, providing reliable crack data and current signal correlation. However, challenges were observed with copper wire, where smearing and interface irregularities limited the analysis. These results highlight the need for material-specific optimizations.
Correlation with real-world stress scenarios: BAMFIT test results correlated closely with fracture characteristics observed in Active Power Cycling (APC) tests, making it a reliable tool for simulating real-world load conditions. This correlation demonstrated BAMFIT's potential for widespread industrial use.
Application of the BAMFIT system for wire bond repair: BAMFIT fracture surfaces showed a very homogeneous topography and a closed surface that could be used as an interface for repair bonds. The BAMFIT system thus combines two features - the fast and automatable removal of wires and the simultaneous creation of defined surfaces for the re-placement of bond contacts.
A pioneering result
The SpeedCycle project not only validated the BAMFIT method, but also highlighted areas for further research, including refinement of copper wire bonding parameters and improved signal analysis techniques. By overcoming traditional test limitations, BAMFIT has set a new standard for evaluating the quality of thick wire bonds, enabling faster development cycles, improved reliability and reduced costs.
Looking back on this journey, the achievements of the SpeedCycle project underscore the importance of innovation and collaboration in advancing the field of bond interface testing. These results provide a strong foundation for future breakthroughs and wider application of BAMFIT technology in modern electronics manufacturing.
At the start of the SpeedCycle project:
The status quo for thick wire bond testing
Prior to the SpeedCycle Project, heavy wire bond testing relied heavily on traditional shear testing, a method that was becoming increasingly inadequate for today's manufacturing requirements. While widely used, shear testing had critical limitations, including surface smear that obscured interface analysis and the inability to provide detailed insight into bond quality or crack propagation. This static method measured mechanical strength but did not reflect real-world dynamic conditions, such as thermal and mechanical stresses.
Process optimization was slow and costly as manufacturers relied on trial-and-error adjustments based on limited shear test data. The method struggled to adapt to varying materials, especially copper wire, where smearing and inconsistent results further complicated analysis. In addition, the growing need for faster, more accurate testing to meet the demands of power electronics and automotive applications exposed the inefficiencies of the existing approach.
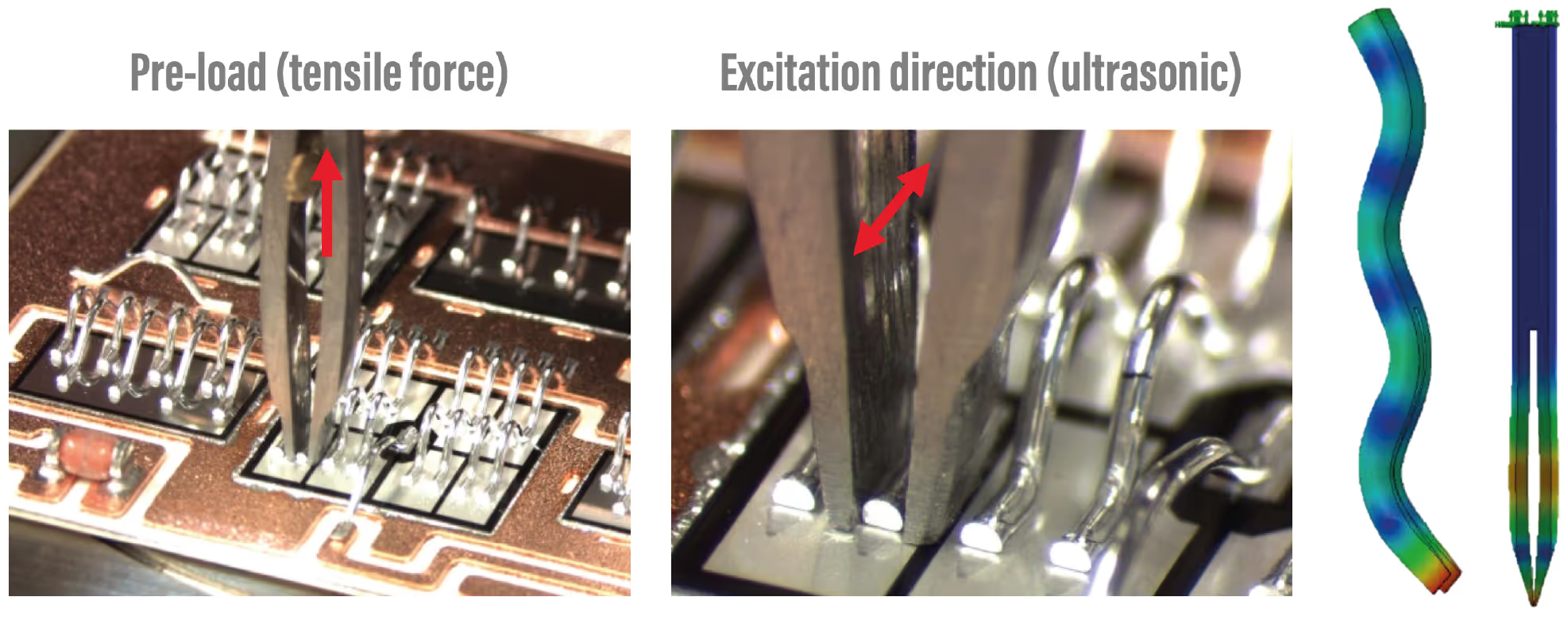
How BAMFIT testing works
The BAMFIT (Bondtec Accelerated Mechanical Fatigue Interconnect Testing) method uses ultrasonic vibration to analyze the quality and integrity of wire bond interfaces. At its core, the method subjects wire bonds to high-frequency mechanical vibrations that simulate the stresses experienced under real-world conditions. This controlled excitation provides valuable data on the performance of the bond, including its ability to withstand mechanical fatigue and maintain integrity.
During a BAMFIT test, the wire bond is clamped and subjected to a preload force while ultrasonic vibrations are applied in a specific direction. These vibrations create dynamic mechanical stresses that progressively challenge the strength of the bond. Sensors within the system monitor key parameters, including ultrasonic transducer current and frequency, and capture real-time data as cracks form and propagate through the bond interface.
The result is a detailed fracture pattern that provides critical insight into the quality of the bond. Unlike traditional methods, BAMFIT allows clear identification of bonded and unbonded regions, providing an accurate map of the interface. This makes it possible to detect weak spots, incomplete bonding regions and areas of surface interaction. In addition, by analyzing changes in system current and frequency during the test, BAMFIT can track the progression of cracks over time, providing a dynamic view of bond durability.
In summary, BAMFIT's innovative approach combines ultrasonic excitation with real-time monitoring to provide a comprehensive assessment of wire bond quality. Its ability to simulate real-world conditions and generate actionable data makes it a groundbreaking tool for modern manufacturing. With this foundation, the benefits and capabilities of the BAMFIT method can be better understood.
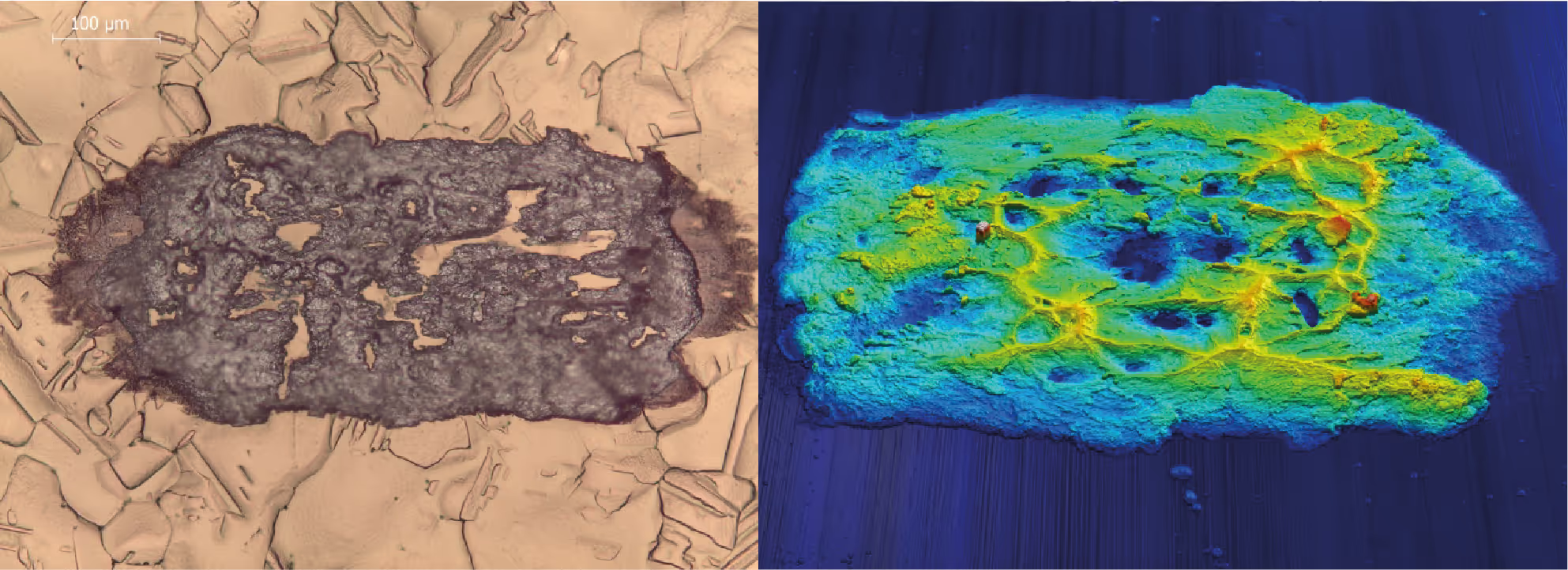
Objectives of the project SpeedCycle
By focusing on different wire materials and bonding surfaces, the project attempted to validate the BAMFIT method as a superior alternative to traditional shear testing. One of the primary objectives was to evaluate the performance of various wire materials under the BAMFIT method:
Aluminum wires: Heraeus Al-H11 served as the reference material, with wire diameters ranging from 125 μm to 500 μm. This material was subjected to varying bonding parameters to analyze how interface formation and microstructural changes affect BAMFIT results. In addition, the behavior of Al-H14 and Al-Mg wires (300 μm) was investigated and compared to the reference Al-H11.
Copper Wires: Tests on Heraeus PowerCu Soft wires (300 μm and 500 μm) were conducted to evaluate the applicability of the BAMFIT method to these high hardness materials, which differ significantly from aluminum-based wires.
Surface and interface studies
To provide comprehensive validation, wire materials were bonded to various surfaces and subjected to BAMFIT and shear tests. These combinations included
Leadframe copper
Direct Copper Bond (DCB) substrates
Printed circuit boards with ENIG plating
Semiconductor surfaces with aluminum coatings
Silver/platinum and silver/palladium pastes
Aluminum sheets with machined surfaces
Key findings and insights
Interface analysis and fracture patterns: BAMFIT revealed distinct bonded and unbonded regions with exceptional clarity. This capability allowed detailed mapping of bond interfaces and provided insight into the effects of bond parameters on interface quality.
Material-specific observations: The project confirmed BAMFIT's ability to handle a wide range of aluminum wire diameters and materials. However, challenges with copper wire, including smearing and complex fracture patterns, highlighted areas for further research.
Dynamic crack analysis: BAMFIT's ability to track crack initiation and propagation in real time provided a significant advantage over shear testing. For CuCorAl and other composite wires, BAMFIT revealed how internal material interactions influence crack behavior.
Work packages
Work Package 1: Investigations on BAMFIT Test Settings
The first work package focused on determining robust test parameters for BAMFIT on a 300 μm Al-H11 wire. This included optimizing parameters such as clamp height, ultrasonic power, and preload force. The results showed that BAMFIT was highly sensitive to parameter variations, with ultrasonic power and preload having the most significant influence on test results. This sensitivity underscored the importance of precise parameter control to ensure reproducibility and accuracy.
Work package 2: Influence of wire diameter on BAMFIT results
WP2 investigated the effect of wire diameter on BAMFIT performance by testing Al-H11 wires of different diameters (125 μm to 500 μm). The study found a clear correlation between wire diameter and BAMFIT results, with larger wires requiring adjusted parameters to maintain test accuracy. Clamping height and ultrasonic power had to be scaled proportionally to wire diameter. This work confirmed that BAMFIT is adaptable to a range of wire geometries, provided that appropriate adjustments are made.
Work Package 3: Sensitivity to Process Variations
This package investigated whether BAMFIT or shear testing is more sensitive to changes in bonding parameters. By varying bond force, ultrasonic power, and bond time, the project demonstrated that BAMFIT consistently provided more detailed and sensitive responses to process changes than shear testing. BAMFIT revealed variations in crack formation and bond quality that shear testing could not detect, particularly in the early stages of interface degradation.
Work Package 4: Crack initiation and propagation
WP4 focused on the analysis of crack initiation and propagation in different wire materials under BAMFIT testing. The study revealed that crack propagation patterns varied significantly between materials. For example, aluminum wires showed predictable crack growth from the edges to the center, while composites such as CuCorAl showed more complex behavior due to internal interactions.
Work package 5: Testing Al-H11 on different surfaces
This work package evaluated the performance of 300 μm Al-H11 wires on different surfaces, including leadframe copper, DCB-Cu, and ENIG plated PCB. BAMFIT effectively highlighted differences in bond quality on these substrates, revealing unbonded regions and subtle variations in interface strength.
Work package 6: CuCorAl wire testing
WP6 investigated the behavior of 300 μm CuCorAl wires under BAMFIT testing. The study confirmed that composite wires present unique challenges due to the presence of distinct interfaces within the material. BAMFIT revealed how intermetallic phases influence crack initiation and propagation, providing valuable insight for optimizing bonding parameters. While BAMFIT was effective in analyzing CuCorAl, the results highlighted the need for further refinement of test settings to handle complex material behavior.
Work Package 7: Testing Copper Wires
In this package, 300 μm PowerCu Soft wires were tested on copper-based substrates. BAMFIT showed its limitations with this material, as smearing and deformation during bonding made interface analysis difficult. While the method could still provide useful data, further adjustments to test settings and analysis techniques were identified as necessary to fully adapt BAMFIT for high hardness materials such as copper.
A Combined Methodology: BAMFIT and Shear Test Integration
The SpeedCycle project has developed a novel methodology that integrates the strengths of BAMFIT (Bondtec Accelerated Mechanical Fatigue Interconnect Testing) and traditional shear testing. This hybrid approach leverages the dynamic, real-time analysis capabilities of BAMFIT with the mechanical insights provided by shear testing. Together, they provide a more comprehensive and reliable assessment of joint quality, overcoming the limitations of each method when used independently.
1.) Initial BAMFIT testing:
Bonds are subjected to BAMFIT to simulate mechanical stresses and dynamically monitor crack propagation.
Key parameters such as transducer current and frequency shifts are recorded, providing insight into the initial bond durability and crack progression over time.
2.) Follow-up shear testing:
After the BAMFIT test, the bond is subjected to a shear test to quantify residual mechanical strength and evaluate the fracture surface.
Shear test data, such as shear force and fracture patterns, complement the BAMFIT results by providing direct mechanical measurements.
3.) Correlation of results:
Data from both tests are combined to identify relationships between BAMFIT indicators (e.g., current drop, crack area) and shear strength.
This correlation provides a deeper understanding of bond behavior under both dynamic and static loading.
Benefits of the combined methodology
Improved accuracy and reliability: BAMFIT alone is highly sensitive, but can have significant scatter in results, especially for certain materials. The addition of shear testing stabilizes the analysis by providing consistent mechanical data, reducing the impact of BAMFIT's inherent variability. Shear testing adds a mechanical benchmark, ensuring that conclusions drawn from BAMFIT are supported by tangible strength measurements.
Comprehensive interface analysis: BAMFIT excels at identifying bonded and unbonded areas within the bond interface, while shear testing provides insight into overall bond integrity and residual strength. The combination provides a detailed understanding of interface quality, crack propagation, and mechanical durability.
Improved insight into crack propagation: BAMFIT dynamically tracks crack initiation and growth, but the addition of shear testing enables precise analysis of fracture surfaces after cracks have formed. This dual approach provides a clearer picture of crack evolution and its ultimate impact on bond strength.
Broader applicability across materials: While BAMFIT faces challenges with certain materials (e.g., copper wire), shear testing is less sensitive to these issues. The hybrid methodology ensures that reliable results can still be obtained for materials that are difficult to analyze with BAMFIT alone.
Optimized process development: By combining BAMFIT's sensitivity to process changes with the mechanical validation of shear testing, manufacturers can better optimize bonding parameters. This results in more robust processes, reduced yield losses, and improved product reliability.