New Standards in Wire Bonding: A Detailed Analysis of DVS-2811 for Automotive and Power Electronics
Title: Advanced wire bonding standards for European automotive and power electronics industry
Authors: Stefan Schmitz, Martin Schneider-Ramelow
Non-destructive pull testing
Destructive shear testing
Process-integrated monitoring
Shear strength calculation
Failure mode inspection and classification
5 pictures illustrating failure modes and bond deformation.
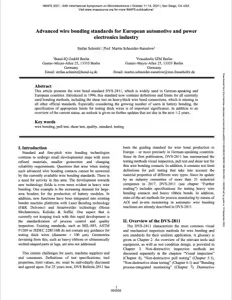
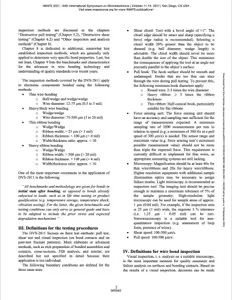
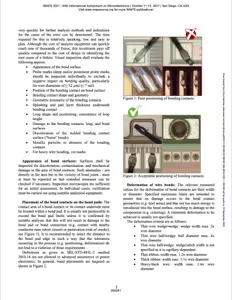
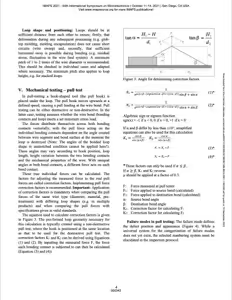
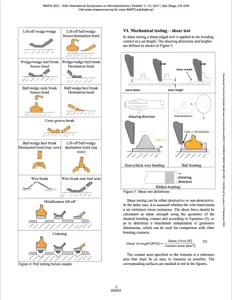
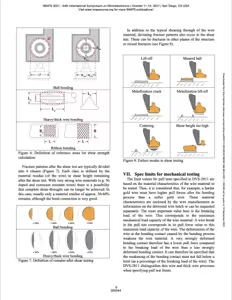
Executive Summary
The authors examine the advancements in wire bonding standards for the European automotive and power electronics industries. Wire bonding is a method of creating electrical connections between semiconductor devices and their packaging using thin wires, which are of critical importance for the production of microelectronics, such as batteries. The study concentrates on the DVS-2811 standard, which provides guidance on the testing and inspection of wire bonds.
A significant area of interest is the handling of thick wires, particularly as the industry transitions to applications that necessitate larger wire sizes, such as battery modules.
While numerous existing standards concentrate on thinner wires, the DVS-2811 standard incorporates testing methodologies for thick wires, including pull and shear tests. These tests evaluate the mechanical strength of the bonds to guarantee that they satisfy quality standards. The research underscores the significance of establishing precise limits for these tests to ensure reliability, particularly in industries such as automotive electronics, where failure can have severe consequences.
Get your article summary
The summary will be sent to your email address
Main Focus
The authors examine the advancements in wire bonding standards, with a particular focus on the DVS-2811 standard. This standard is widely utilized in the European automotive and power electronics industries and addresses the mounting challenges of wire bonding in applications necessitating both thin and thick wires. The study encompasses the methodology for evaluating the mechanical and visual characteristics of wire bonds, introduces updated specifications for thick wire bonding, and delineates prospective avenues for extending the standard to align with the evolving demands of high-reliability applications such as electric vehicles and power electronics.
Background and Motivation
Wire bonding remains a foundational interconnection technology in microelectronics, particularly in domains such as automotive and power electronics, where reliability is of paramount importance. As industries transition towards high-power applications such as battery modules, there is an increasing necessity for bonding standards that can accommodate thick wires (with a diameter exceeding 100 µm). The existing standards, including MIL-883, JEDEC 22B116B, and ASTM standards, provide guidance on the bonding of thin wires but lack specific limits and procedures for thick wires and ribbons.
This paper addresses these shortcomings by presenting updates to the DVS-2811 standard, which was first introduced in 1996 and has since undergone regular revisions. The impetus for this endeavor arises from the necessity to guarantee uniform quality in wire bonding for applications where reliability is a critical determinant of performance and safety, such as in electric vehicles.
Methodology
The DVS-2811 standard encompasses a comprehensive range of mechanical and visual testing methodologies. In the context of mechanical testing, the two principal methods employed are the pull test and the shear test.
- Pull Test – Equipment and Setup: The pull test entails the utilisation of a hook-shaped instrument positioned beneath the wire bond loop, which exerts an upward force at a pre-defined velocity, thereby exerting a tensile load on the wire. The choice between a destructive and a non-destructive pull test is dependent on the specific application in question.
- Pull Test – Mathematical Model: Correction factors (K1 and K2) are calculated in order to adjust the force applied based on the bond angles and loop geometries. This correction enables the precise estimation of the actual forces exerted on each bond in unequal angle geometries. The equations for these correction factors and force calculations are provided in detail, thus ensuring precision in the comparison of test results across different wire geometries.
- Pull Test – Force Sensing: The force-sensing units utilized have a minimum sampling rate of 300 Hz, enabling the capture of data at appropriate speeds (100–500 µm/s). It is of paramount importance to ensure accurate sampling in order to obtain reliable measurements of bond strength.
- Shear Test – Equipment and Setup: A tool with sharp edges is applied to the bond contact at a defined height, and the resulting shear force is measured. The test may be conducted in a destructive or non-destructive manner, depending on whether the bond is subjected to failure or not.
- Shear Test – Calculations: The shear strength is calculated by dividing the shear force by the contact area, thus enabling comparisons to be made across different bond geometries. This enables the standard to provide consistent benchmarks regardless of the dimensions or configuration of the bond.
- Shear Test – Failure Modes: Both tests include a comprehensive failure mode analysis, encompassing wire lift-off, heel breaks, and metallization lift-off, which are pivotal in elucidating bond reliability.
Key Findings
- Thick Wire Bonding: The study underscores the necessity for revised standards pertaining to thick wire bonding, which is pivotal for power electronics and battery module applications. The latest edition of DVS-2811 incorporates pull and shear test specifications for wires with diameters up to 500 µm, thereby addressing a previously unaddressed gap in the standards.
- Force and Strength Metrics: In the case of thin wires, the individual pull test values must not fall below 30% of the wire's breaking load. In contrast, for thick wires, the limit is raised to 80% of the breaking load. Similarly, the shear strength limits for thick wire bonding are set at 35 MPa for individual values and 45 MPa for the sample mean, thereby ensuring the formation of robust wire bonds capable of withstanding operational stresses.
- Non-destructive Testing and AOI: The incorporation of process-integrated monitoring techniques, such as Automated Optical Inspection (AOI), is especially advantageous in high-volume production settings where immediate quality assurance is paramount.
- Failure Mode Analysis: The research offers a comprehensive classification of failure modes, including wire breakage in the heel area, metallization lift-off, cratering, and various shear fracture patterns. This analysis is of paramount importance for the diagnosis of bond failures in critical applications such as automotive electronics.
Implications for Future Research and Industry
The findings indicate that future enhancements to DVS-2811 will necessitate the incorporation of wire diameters that are significantly larger, potentially reaching 625 µm, and ribbon widths of up to 3 mm, which are becoming increasingly prevalent in high-power applications. The incorporation of these enhancements will satisfy the increasing demand in sectors such as electric vehicle batteries, where the dimensions and dependability of wire bonds are crucial for optimal performance and safety.
Furthermore, the study underscores the necessity for the establishment of more material-specific testing limits.
For example, while aluminum and gold wires have been extensively characterized, new materials such as bi-metal wires (e.g., copper core with aluminum cladding) require further research to establish appropriate testing criteria. This is particularly crucial in the context of high-reliability applications, where failure could have significant ramifications.
The paper advocates for the establishment of more precise definitions of failure modes, accompanied by high-resolution microscopy images, in alignment with methodologies observed in other standards, such as JESD22-B116B. An enhanced comprehension of failure patterns will enable manufacturers to enhance their processes and diminish failure rates.
Limitations
- Material-Dependent Limits: The current standard does not fully address the nuances of material properties for newer wire materials, such as copper and bimetallic wires, which require further investigation. Additional empirical data is required to refine these limits.
- Shear Test Data for Thick Ribbons: The standard currently lacks validated test data for thick ribbon bonds, particularly as the dimensions of the ribbons increase in order to accommodate applications such as battery modules. Further detailed studies are required in order to establish reliable benchmarks for these bonds.
- Complexity in Statistical Models: Although the pull test correction factors offer more precise force calculations, their implementation in diverse loop geometries and bond configurations can be intricate and may necessitate further optimization for broader industrial applications.
- Limited Visual Representation: Despite the categorization of failure modes, the dearth of comprehensive, high-resolution visual exemplars constrains the expediency with which manufacturers can discern and rectify bond-related concerns. The paper proposes the inclusion of more detailed microscopic images in future revisions, with the aim of assisting users in accurately assessing bond quality.
Get your article summary
The summary will be sent to your email address